Welding repair is an important task in industries that use heavy equipment like pressure vessels. It involves connecting metal parts using heat, pressure, and sometimes filler material. Proper welding repair requires specialized skills, knowledge, and equipment to ensure the welding repair is performed accordingly. In this article, we will cover the fundamentals, techniques, and process of welding repair.
What is Welding Repair?
Welding repair is a commonly used method where the damaged material is eliminated through arc gouging and then the element is welded to reconnect the material on either side of the crack. By exposing both sides to high-temperature heat until they reach their melting point making a strong and robust bond.
In the case of welding repair, the damaged portion of the structure is typically removed, and a replacement piece of metal is welded in its place. The process may involve various welding techniques depending on the nature of the damage and the type of metal being used.
For specific industries like oil and gas, welding repair is a vital technique when it comes to repairing pressure equipment. With the existence of ASME PCC-2, engineers can follow the guidelines for repairing pressure equipment using various methods, including welding repair.
What Are Welding Repair Techniques?
ASME PCC-2 guides the selection of welding procedures for repairing damaged pressure equipment. It outlines the necessary procedures to ensure safe and effective welding repair and recommends the appropriate technique based on the metal and damage type. Below are some of the welding repair techniques that are recommended by the standard.
1. Shielded Metal Arc Welding (SMAW)
Stick welding or SMAW is a welding process where a consumable electrode coated with a flux that melts and provides a gas shield during welding is used. This welding process is versatile and can be utilized to weld different types of metals and alloys.
2. Gas Tungsten Arc Welding (GTAW or TIG)
TIG welding or Gas Tungsten Arc Welding (GTAW) is a welding process where a non-consumable tungsten electrode is utilized to create the weld. It usually requires a separate filler metal to join the two metal parts.
3. Gas Metal Arc Welding (GMAW or MIG)
MIG welding or Gas Metal Arc Welding (GMAW) is a welding process that utilizes a continuous wire electrode and a shielding gas to prevent the weld from being contaminated. GMAW is a fast and efficient welding process and is frequently utilized in industrial and automotive applications.
4. Flux Cored Arc Welding (FCAW)
Flux Cored Arc Welding (FCAW) is a welding process that utilizes a tubular wire containing flux to provide a protective gas shield and additional filler metal. FCAW is a versatile process and can be applied to weld different types of metals, such as aluminum and stainless steel.
5. Submerged Arc Welding (SAW)
Submerged Arc Welding (SAW) is a welding process that employs granular flux to provide a protective gas shield and an additional filler metal source. SAW is commonly used in heavy industrial applications and is renowned for its high deposition rates and deep penetration.
What Are Welding Repair Procedures?
The welding procedures provide step-by-step directions for the repair process. The main purpose of welding repair procedures is to ensure that the repaired component meets the required quality and safety standards.
In general, there are three steps in the welding repair procedure:
- Preparation for welding
- Repair welding
- Postweld operation
What Are The Steps in Preparation for Welding?
The steps in preparation for welding include the following:
1. Safety
Prior to repair welding, ensure safety compliance by inspecting the designated area, removing flammable materials, and addressing potential hazards like toxic substances.
2. Cleaning
The immediate work area must be thoroughly cleaned from all contaminants such as dirt, grease, oil, rust, paint, and plastic coverings. The cleaning method varies based on the material and workpiece location. Options include steam cleaning, solvent cleaning, abrasive blast cleaning, pickling, solvent dip cleaning, and power tool cleaning.
3. Disassembly
For more complex repair jobs, disassembly may be necessary. This includes components like lubrication lines, instrument tubing, wiring, and even major machinery from machinery frames.
4. Protection of adjacent machinery and machined surfaces.
During machinery repair welding, it is essential to protect unremoved parts from weld spatter, flame-cutting sparks, and other debris. Sheet metal guards or baffles can shield adjacent machinery, while asbestos cloth is suitable for machined surfaces.
5. Bracing and clamping
For complex repair jobs, bracing or clamping is required to support heavy parts or handle external loads on the weld-repaired component. Temporary braces can be welded to the structure undergoing repair.
6. Lay out repair work
In repair jobs, metal removal is needed for a full-penetration weld. A layout is prepared to indicate the metal to be cut or gouged for welding preparation, aiming for minimal removal while ensuring balanced and comfortable welding positions.
7. Preheating
Preheating and flame cutting or gouging are integral to welding preparation and can be seen as part of the welding process. Preheating should match welding requirements, although its significance might be slightly less due to smaller stresses. Nevertheless, both flame cutting and gouging can subject the metal to thermal shock, similar to welding.
8. Cutting and gouging
The oxygen fuel gas-cutting torch with special gouging tips is commonly used. Cracks can be detected during flame gouging by observing heated edges. Air carbon arc cutting is also widely used. Mechanical chipping and grinding may be used for unsuitable metals.
9. Grinding and cleaning
Prior to welding, the surfaces should be ground to clean bright metal, although they may not be perfectly smooth. For critical work or suspected additional cracks, magnetic particle inspection is recommended to ensure all defects are removed.
What Are The Steps in Repair Welding?
The steps in repair welding include the following:
1. Welding Procedure
In this step, the welding procedure should be readily available for welders and must outline the specific welding process and joint technique required. Common techniques include arc welding, gas welding, and TIG welding.
2. Welding Equipment
Sufficient welding equipment should also be provided to avoid delays, and standby equipment may be necessary. This includes welding equipment, holders, grinders, wire feeders, cables, etc.
3. Materials
Adequate materials, including filler metals stored properly, should be accessible for the entire job. This also includes insert pieces, reinforcing pieces, and other materials. Additionally, fuel for preheating and interpass temperature, shielding gases if used, and fuel for engine-powered welding machines must be available.
4. Alignment Markers
Before welding, alignment markers are occasionally employed, often as simple center punch marks made across the joint at different locations.
5. Welding Sequences
The welding sequence, such as block welding, back-step sequence welding, wandering sequence welding, and peeling, should be clearly outlined in the welding procedure.
6. Weld Quality
Continuously inspect the weld quality, ensuring a smooth final weld with no notches or reinforcing. If needed, perform grinding to maintain smooth contours.
What Are The Steps in Postweld Operation?
The steps in post weld operation include the following:
1. Inspection
Inspect the completed weld for its smoothness and overall quality, which may involve nondestructive testing methods like magnetic particle, ultrasonic, or X-ray. It is essential for the repair weld to be of high quality as it is replacing the original high-quality metal.
2. Clean Up Operation
This involves removing strong backs and their attachment points, as well as other bracing and protective covers. All weld stubs, spatter, slag, and residue must be thoroughly cleaned from the repair area to ensure it is cleaner than its original state. Special attention is required to remove all grinding dust as it can be abrasive and cause future problems if it enters working joints or bearings.
3. Repainting
Once the weld and surrounding repair area have been thoroughly cleaned, they should be repainted, and other areas should be re-greased to prepare the machinery for re-operation.
4. Reassembly
After the cleaning and painting process, the components of the machinery that were removed are reinstalled, which includes the reassembly of the machinery.
What Are The Standards That Regulates Welding Repair?
Numerous standards govern welding repair to prioritize safety, quality, and compliance with industry norms. The mentioned standards are some of the key standards that offer guidelines and procedures for conducting welding repairs on different equipment, piping, and pipelines in the oil and gas industry.
1. ASME B31.3 – Process Piping
ASME B31.3 addresses requirements for the design, materials, fabrication, inspection, examination, and testing of process piping systems. It includes guidelines for welding processes used in these systems.
2. ASME BPVC Section VIII – Rules for Construction of Pressure Vessels
ASME Section VIII outlines the welding and fabrication requirements for pressure vessels used in various industries.
3. ASME PCC-2
ASME PCC-2 offers guidelines for repairing pressure equipment. Although it doesn’t directly govern repair welding, it does provide suggestions and steps for utilizing repair welding as one of the methods to fix pressure equipment.
Welding repair is a complex process that requires specialized knowledge and expertise. With the safety of personnel and the integrity of pressure equipment at stake, it’s critical that welding repairs are performed properly. That is why understanding welding repair thoroughly is essential for anyone involved in repairing pressure equipment and piping.
By taking ASME PCC-2 Repair of Pressure Equipment training course, you can gain not only the knowledge and skills needed for repair welding but also all related knowledge regarding repairing pressure equipment.
PetroSync’s ASME PCC-2 training aims to introduce you to the standard’s basic concepts and philosophy, as well as its various procedures for repairing pressure equipment and piping. The advantages and disadvantages of these procedures will also be discussed.
You will also learn about the correlation of this standard with other in-service codes and standards such as API 510/API 570/API 579/API 580. This course will be beneficial not only to maintenance engineers but also to supporting disciplines such as design, operations, and inspection engineers.
It will aid in collectively troubleshooting and resolving problems related to temporary or permanent repairs of equipment and piping at the site. Join us and master the repair of pressure equipment knowledge and skills by learning practical things from PetroSync’s expert instructor!
Credit header image: swensonwelding.net
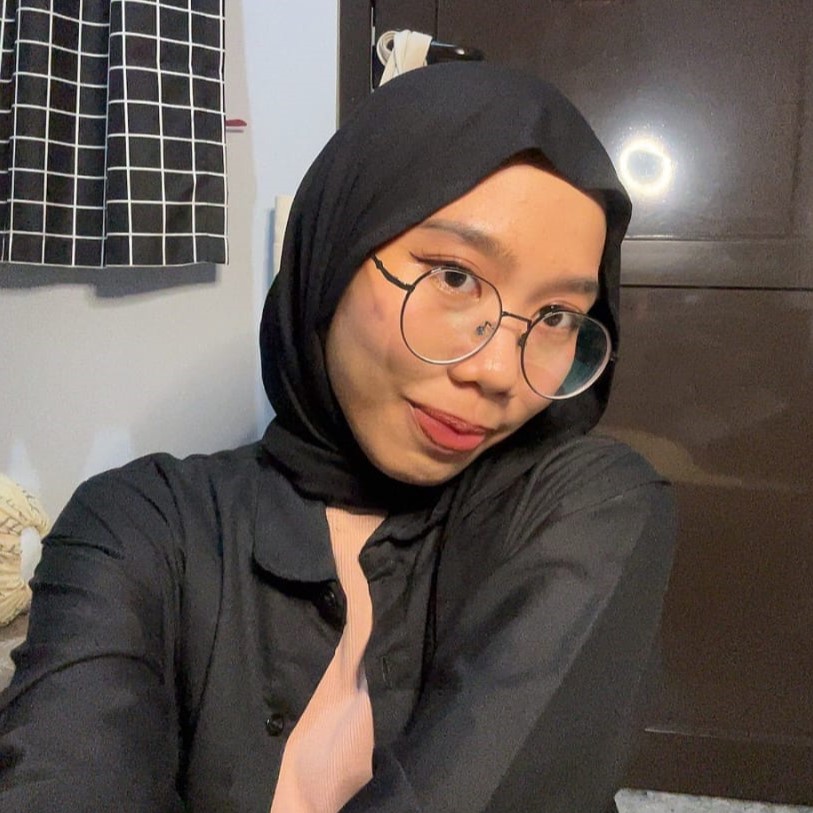
SEO specialist by day, fact-checker by night. An avid reader and content writer dedicated to delivering accurate and engaging articles through research and credible sources.