Every day, problems are part of the workplace’s dynamics. Solving minor issues is indeed uncomplicated, but how about the major incidents impacting an organization’s safety, quality, and productivity? Unraveling the cause and applying accurate techniques like root cause analysis for assessing the issue takes more than time.
To address these problems and prevent them from continuing, any delegated organizational teams must learn and use root cause analysis techniques. This method can lead to a more productive, efficient, and safer workplace.
So, what is root cause analysis? How can an individual implement the understanding and have the practical experience to perform RCA analysis better? This article will cover everything you need to start your journey to gain the skill of RCA that is applicable to your workplace.
What Is Root Cause Analysis?
Root cause analysis (RCA) is a systematic method for identifying the underlying causes of problems in order to implement effective solutions. Unlike approaches that merely address the symptoms, RCA dives deeper into the problem, investigating its core factors. The goal is to uncover the true sources of an issue to prevent it from reoccurring, ultimately leading to more sustainable solutions.
The RCA process involves several steps, including gathering relevant data, analyzing information, identifying potential causes, and taking corrective actions. This approach not only resolves the immediate problem but also reduces the risk of similar issues arising in the future.
Industries such as petroleum, petrochemicals, engineering, electricity, and manufacturing rely heavily on RCA due to the complexity of their operations. These sectors often face significant risks of accidents and failures due to the intricate systems and mechanics they manage daily.
The challenge of RCA lies in considering technical complexities, environmental factors, and human errors. However, by accurately identifying and addressing the root causes, RCA can greatly improve the overall quality, safety, and efficiency of industrial operations.
What Is The Objective of Root Cause Analysis?
Aside from preventing problems and mishaps from reoccurring, RCA can benefit organizations with an in-depth understanding of how to address, mitigate, and finally get a learning process from the issues. Systematically blocking future accidents and drawbacks while reaping success is possible to achieve if the organizations carry out the correct way of RCA.
For instance, an explosion occurred at an oil refinery resulting in multiple fatalities, injuries, and damage to the equipment and surrounding areas. A root cause analysis can be a robust process to analyze the incident, such as interviewing witnesses, examining the incident details, reviewing the maintenance documents, and conducting a detailed assessment of the equipment involved.
The design failure triggering the explosion becomes the root cause. The RCA personnel could finally summarize and give recommendations to prevent the incidents from happening again.
What Are The 5 Steps of Root Cause Analysis?
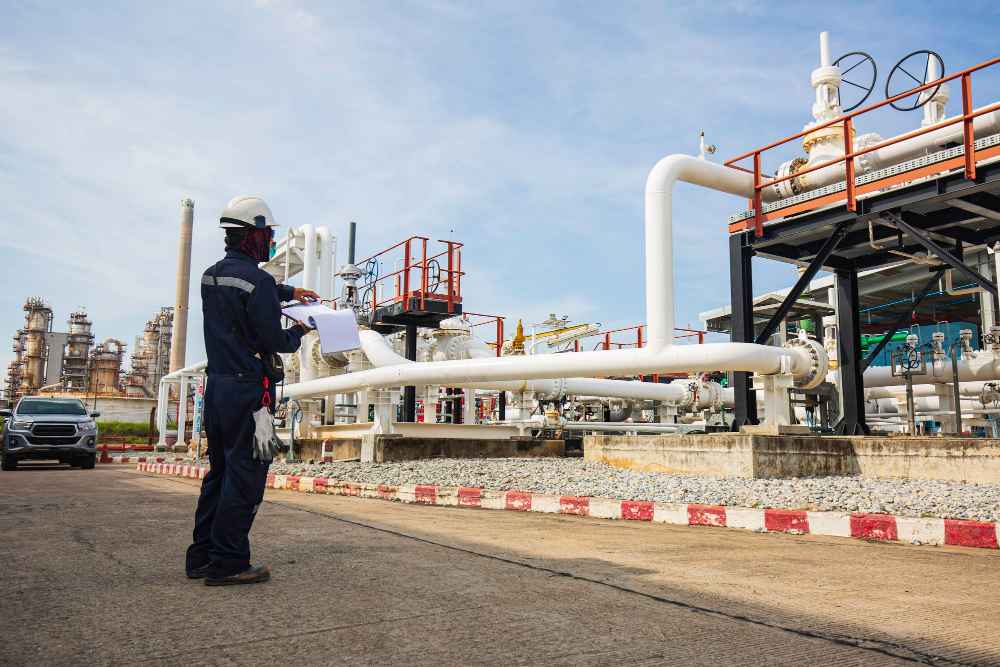
If the root cause analysis (RCA) process is messy or lacks structure, the results may not be thorough or accurate. This can happen when the steps of the analysis aren’t followed in the right order, or important details are missed. To ensure RCA delivers high-quality results, it’s crucial to follow the five key steps outlined below:
1. Define the Problem
The first step is to clearly identify and define the problem at hand, specifying its scope and impact.
2. Collect Relevant Information
Next, gather all relevant data related to the issue, such as past records, observed symptoms, and any other useful information.
3. Identify Potential Causes
Use methods like brainstorming or cause-and-effect diagrams to explore possible root causes, based on the data you’ve collected.
4. Analyze the Data
Examine the collected information through statistical analysis or process mapping to pinpoint the most likely root cause(s).
5. Implement Solutions
Once the root cause(s) are identified, create and put into action solutions that tackle the problem. Continuously monitor and refine these solutions to ensure they remain effective in the long run.
What Are The 5P Approach of Root Cause Analysis?
However, these five steps should always pay attention to the 5P approaches. The 5P in RCA includes parts, positions, paper, people, and paradigms are explained down below:
1. Parts of the mechanics
The first approach involved in the incidents must be preserved.
2. Positions
In the next approach, positions are recorded in photos to have accurate access to incident conditions.
3. Paper
The third approach named paper symbolizes the latest inspection report and the company’s regulations regarding the matter.
4. People
People refer to those who are involved in the incidents (including the engineer, technician, and the last inspector assessing the safety).
5. Paradigms
Paradigms or perception of the issue.
Performing the RCA approach in the correct steps with the 5P fundamentals above can lead to accurate results in examining the root cause.
What Are The 5 Whys Approach of Root Cause Analysis?
For effective use of the 5 Whys method, it is crucial to adhere to a systematic approach. Here’s a detailed, step-by-step outline:
Step 1: Define the problem
Start by clearly defining the problem you want to solve and who it affects. Gather information, talk to people involved, and confirm the issue’s importance.
Step 2: Ask “Why?” until you find the root cause
Begin by asking why the problem occurred, then repeat the question for each answer you get. Keep asking “Why?” until you reach the root cause. For example:
- Why did the machine break down?
- Why was the lubricant insufficient?
- Why did the machine not get enough lubrication?
- Why was the system not corrected?
- Why did technicians not follow the manual?
By asking “Why?” multiple times, you can uncover the underlying causes. In this example, inadequate training for maintenance technicians emerges as the root cause.
Step 3: Analyze the root cause
Once you’ve identified the root cause, analyze it thoroughly. Consider possible solutions and seek input from others. Write down your findings to stay organized.
Step 4: Implement corrective actions
Based on your analysis, develop practical solutions to address the root cause. Make adjustments to prevent the problem from recurring in the future. This step turns your insights into tangible improvements, enhancing overall effectiveness.
Following these steps will help you effectively apply the 5 Whys approach to identify and address root causes of problems.
How To Improve RCA Quality?
Improving the quality of Root Cause Analysis (RCA) in high-risk industries like oil and gas, petrochemical, and energy requires careful attention to several key practices:
1. Focus on correcting and remedying root causes rather than just symptoms
Instead of addressing only the surface-level issues, delve deeper to identify the underlying reasons behind the problem. This ensures that solutions are effective and sustainable in the long term.
1. Exclude Involved Parties from RCA Sessions
It i crucial not to include individuals directly involved in an incident during the RCA process. Instead, conduct one-on-one interviews with them to gather information objectively. Invite representatives from relevant departments, such as engineering or operations, to participate in the RCA exercise to ensure a more impartial analysis.
Don’t ignore the importance of treating symptoms for short term relief. While it’s essential to address root causes, sometimes it’s necessary to alleviate immediate symptoms to prevent further damage or disruptions. Balancing short-term fixes with long-term solutions is key.
2. Focus on HOW and WHY Something Happened, not WHO Was Responsible
Avoid assigning blame and instead focus on understanding the processes and circumstances that led to the problem. This encourages a collaborative approach to problem-solving and prevents a culture of finger-pointing.
3. Frame Questions Based on Facts, Not Hypotheses
When questioning participants, avoid leading them toward predetermined conclusions. Focus on gathering factual information about equipment, procedures, and actions taken rather than suggesting potential causes.
4. Engage Industry Experts and Leadership
Ensure that physicians and key industry leaders are actively involved in the RCA process from the beginning. Their input and expertise can lead to more meaningful insights and sustainable process improvements.
5. Distinguish Between The Problem and The Cause
Shift the focus of the RCA from the adverse outcome to the actions or factors that led to it. For instance, in the case of a safety incident, identify specific actions or oversights that contributed to the incident rather than solely focusing on the outcome itself.
6. Provide Enough Information To Inform A Corrective Course of Action
Ensure that your RCA report includes sufficient details about the identified root causes and their implications. This helps stakeholders understand the problem and implement effective solutions.
5. Form A Diverse, Multidisciplinary Team
Assemble a team with representatives from various departments and disciplines, including those not directly involved in the incident. This diversity ensures a comprehensive analysis and brings different perspectives to light.
6. Rely on Documented Evidence for Timelines
Base timelines and sequences of events on reliable documentation rather than relying solely on personal recollections. Utilize records and data from operational logs, equipment readings, and incident reports to establish an accurate timeline of events.
7. Consider How A Root Cause Can Be Prevented (or replicated) In The Future
Use insights gained from the RCA process to develop preventive measures that mitigate the risk of similar issues occurring in the future. Additionally, consider how successful practices can be replicated to improve overall performance.
By adhering to these practices, you can enhance the effectiveness and reliability of RCA in high-risk industries, leading to more robust safety measures and improved operational efficiency.
What Are Some FAQ About Root Cause Analysis?
Let’s explore some frequently asked questions (FAQ) about this essential problem-solving technique.
How Do I Learn Root Cause Analysis?
Nowadays, almost every field of work needs an RCA approach. You can independently learn root cause analysis by following the guidelines and how-to discussed before. RCA is a critical skill to master, with many online resources available to self-learn.
However, biases and blind spots are hard to combat, as doing self-learning results in justifying subjective assumptions frequently. Taking RCA training, especially for those working in high-risk sectors, is the right first step in mastering this skill.
Join PetroSync Training for Expert-Level Industry Knowledge and Certification
Root Cause Analysis Training Course by PetroSync offers a comprehensive and structured approach, relevant study cases, group discussion, and recognized certification for you to build your credibility in RCA. We can help you better understand how to apply root cause analysis to real-world problems. Reserve your RCA training spot and develop your problem-solving skills with PetroSync.
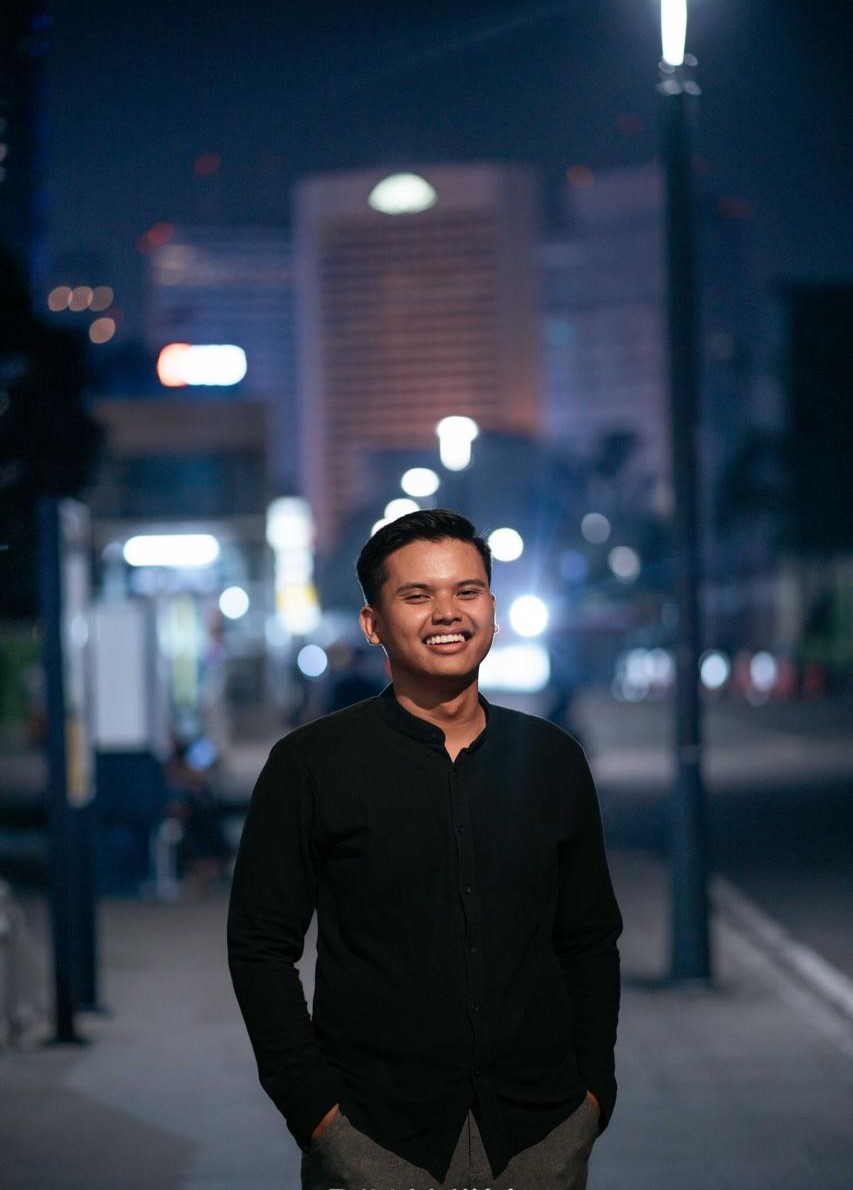
Results-oriented and thorough SEO specialist with extensive experience in conducting keyword research, developing and implementing digital website promotion strategies and plans, managing campaigns to develop company websites in the digital world, excellent knowledge of marketing techniques and principles, and attentive strong attention to detail.