Pneumatic testing is a commonly employed technique in the oil and gas industry to assess the integrity of pressure vessels, pipelines, and other components. Pneumatic testing has various benefits making it become a preferable technique. In this discussion, we will explore the basics of pneumatic testing, its benefits and limitations, and the importance of following proper safety procedures according to ASME PCC-2.
What Is Pneumatic Testing?
Pneumatic testing is the process of using gas to verify a vessel’s ability to withstand normal usage pressures under normal usage. It ensures that the system can withstand pressures beyond its designed pressure limit and be safely subjected to its maximum operating pressure.
Pneumatic testing is essentially utilized to confirm the leak-tightness and structural soundness of pressure vessels, pipelines, and other similar components that are designed to contain or transport fluids or gases under pressure. This type of testing involves using compressed air or another gas to simulate the pressure that the component is expected to experience during normal use.
Pneumatic testing is commonly used in various industries, including oil and gas, chemical, and petrochemical, to verify that pressure vessels, pipelines, and other equipment are structurally sound and safe to operate before being put into service. This testing is typically performed in accordance with industry standards and regulations, such as ASME Section VIII or API 510.
What Are The Limitations of Pneumatic Testing?
The ASME PCC-2 standard provides guidance on pneumatic testing of pressure vessels, piping, and other pressure-containing components, while also addressing the limitations of this type of testing to guarantee its safe and accurate execution.
1. Safety Measures
One of the limitations of pneumatic testing is the potential danger posed by the energy stored in compressed gases if the component being tested fails catastrophically. To mitigate this risk, ASME PCC-2 recommends venting pressure vessels to the atmosphere or installing safety devices such as rupture discs or relief valves to protect personnel and equipment in case of an unexpected pressure release.
2. Materials Selection
Another limitation of pneumatic testing is that the test gas used may not be compatible with the materials or process fluids contained in the component. To avoid adverse reactions or contamination, ASME PCC-2 suggests carefully selecting the test gas and ensuring its thorough cleaning and drying.
3. Test Pressure and Duration
ASME PCC-2 also offers guidelines for selecting the appropriate test pressure and duration to avoid damaging or overstressing the component while still ensuring adequate testing. The standard advises keeping the test pressure below 1.5 times the maximum allowable working pressure (MAWP) of the component and setting the test duration long enough to identify any leaks or deformations, but not so long as to cause permanent damage.
By following these guidelines, ASME PCC-2 ensures that pneumatic testing is conducted safely and accurately, despite its limitations, thus guaranteeing that pressure-containing components are tested effectively and suitable for their intended applications.
What Are The Benefits of Pneumatic Testing?
Compared to hydrostatic testing, pneumatic testing has several benefits, such as the ability:
1. Small Leaks Detection
Pneumatic testing can detect small leaks by pressurizing the system and measuring the pressure drop over time. As the pressure drops, it indicates the presence of a leak and the rate of pressure drop can also help in identifying the location and size of the leak.
2. Specific Components
Pneumatic testing can test components that cannot be filled with liquid by applying compressed gas to the component and detecting any pressure drops, which can indicate leaks or other defects.
3. Non-corrosive and Non-conductive Usage
Pneumatic testing is advantageous because it can use non-corrosive and non-conductive gases, which do not require special disposal procedures, for conducting testing. This is beneficial for testing components that cannot be filled with liquid, and it also allows for the detection of small leaks. Additionally, the use of compressed air in pneumatic testing allows for faster testing compared to hydrostatic testing.
Moreover, compared to hydrostatic testing, pneumatic testing is generally quicker and more cost-effective and can test components at higher pressures, although it also poses safety risks and limitations that need to be carefully managed to ensure safe and accurate testing.
The American Society of Mechanical Engineers (ASME) provides guidelines for conducting pneumatic testing in ASME PCC-2. This standard addresses the limitations and safety concerns of pneumatic testing, providing recommendations for safe and accurate testing.
Under ASME PCC-2 standards, engineers can have the proper guidelines for selecting the appropriate test pressure and duration, choosing the right test gas, and addressing the potential hazards of the energy stored in compressed gases during testing. By following these guidelines, pressure-containing components can be effectively tested to ensure their safe and reliable use.
PetroSync offers ASME PCC-2 training that is not only valuable for maintenance engineers, but it’s also beneficial for other engineering disciplines such as design, operations, and inspection engineers.
By attending PetroSync’s 3-day ASME PCC-2 Repair of Pressure Equipment training course, you will acquire not only proficiency in performing pneumatic testing but get a deeper understanding of pressure equipment repair in general.
The training aims to familiarize you with the standard’s fundamental concepts and principles, as well as its diverse methods for repairing pressure equipment and piping, including the pros and drawbacks of each approach. Enroll in PetroSync’s ASME PCC-2 and enhance the safety of your pressure equipment with us!
Credit Header Image: Freepik
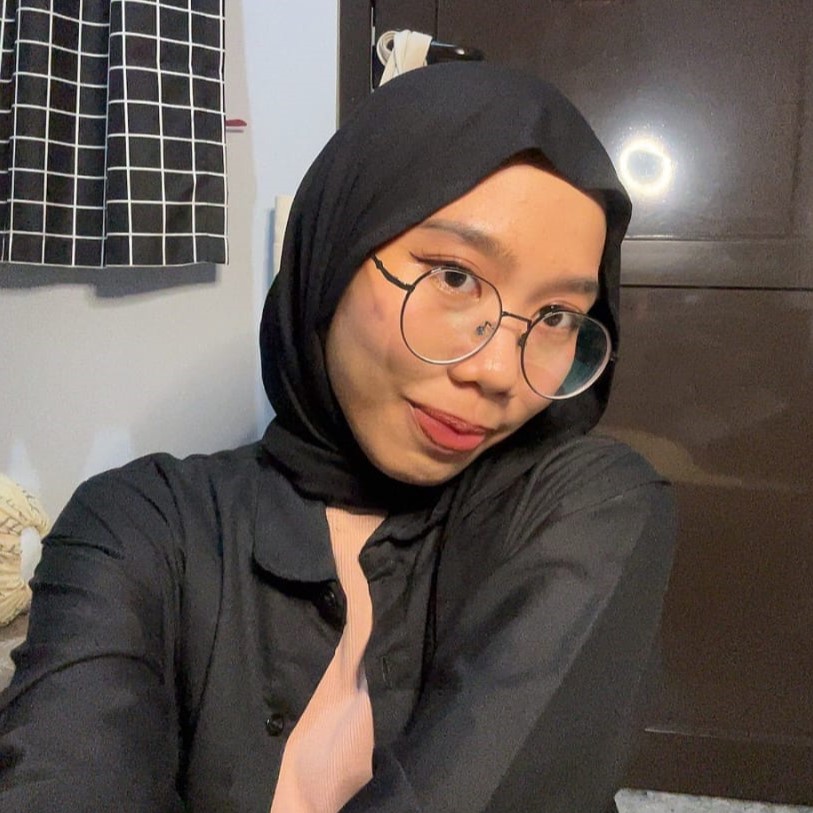
SEO specialist by day, fact-checker by night. An avid reader and content writer dedicated to delivering accurate and engaging articles through research and credible sources.