Corrosion protection is a vital practice in the petrochemical and energy industry. It prevents safety hazards, reduces costs, and maintains compliance with regulations. Corrosion can cause equipment failure, reduce efficiency, and result in legal liabilities. In this article, we will discuss corrosion protection and some related standards regarding corrosion protection procedures.
What Is Corrosion Protection?
Corrosion protection is a process of preventing or reducing the degradation of materials caused by chemical reactions to their environment. This natural process occurs when metals are exposed to oxygen and moisture, leading to rust and other forms of degradation.
Storage tanks tend to have corrosive properties and can cause harm to the metal structure of the tanks. This is why corrosion protection is vital for storage tanks, as it can deteriorate their structural integrity, resulting in potential leaks, spills, and catastrophic failures.
Various corrosion protection methods must be utilized to prevent rust and other types of corrosion on the tank’s surface, including coatings, cathodic protection, and corrosion inhibitors. These measures effectively prolong the storage tank’s lifespan, reduce maintenance expenses, and avoid environmental harm or safety risks.
Corrosion protection is essential to maintaining aboveground storage tanks, as addressed in API 653. The standard provides guidelines for assessing corrosion and other forms of deterioration, selecting appropriate protective measures, and inspecting and maintaining corrosion protection systems.
How To Perform Corrosion Protection for A Tank?
Choosing a corrosion protection method depends on various aspects, including the kind of metal used, the surrounding conditions it encounters, and the anticipated lifespan of the material. Efficient corrosion protection measures aid in improving the endurance and longevity of materials, decreasing the requirement for expensive repairs and replacements.
One of the widely known corrosion protection methods is cathodic protection. It is a specific type of corrosion protection that uses electrochemical principles to prevent corrosion. Cathodic protection is a technique that involves applying a direct electrical current to the tank to prevent corrosion. There are two types of cathodic protection: sacrificial anode and impressed current that exist under API RP 651
1. Sacrificial Anode Cathodic Protection
According to API RP 651, it is recommended to use high-potential magnesium anodes or aluminum anodes with a minimum aluminum content of 0.05%. The anodes should be installed evenly around the tank and their placement should be based on the tank’s design and size. The standard also provides guidance on the installation and monitoring of sacrificial anode cathodic protection systems.
2. Impressed Current Cathodic Protection
Impressed current cathodic protection is a technique that prevents corrosion of a metal surface by utilizing it as the cathode of an electrochemical cell.
This method involves linking the metal that needs protection to a sacrificial metal that corrodes more easily, which functions as the anode. The anode is typically made of a more reactive metal than the structure being protected and is placed in an electrolyte solution that surrounds the structure.
What Are Further Study Materials for Corrosion Protection in The Storage Tank?
Advances in materials science, engineering, and technology continually introduce new corrosion protection techniques, necessitating ongoing study, and research in the field. There are several study materials available for corrosion protection in storage tanks. Some of these resources include.
1. The Lining of the Bottoms of Storage Tanks (API RP 652)
API RP 652 advises that the selection of lining systems for aboveground storage tank bottoms should be based on specific service conditions, such as the type of product stored, temperature, and exposure to corrosive substances.
It is also recommended to design the lining systems to have a minimum service life of ten years, but this duration may differ based on the specific service conditions and the type of lining materials used.
2. API RP 577 and Welding Inspection
API RP 577 and Welding Inspection offer guidance on inspection practices for welding and related activities. The standard gives guidance on different types of welding and related processes, such as brazing, soldering, and cutting.
The main goal of API RP 577 and welding inspection is to promote safe and efficient welding practices and ensure the durability of welded structures across a range of industries.
3. Rules Imposed by ASME Section V for Various NDE Techniques Final Examinations
ASME Section V provides a set of regulations governing the use of different NDE techniques for conducting final examinations. These methods include visual inspection, liquid penetrant testing, magnetic particle testing, radiographic testing, ultrasonic testing, and eddy current testing.
The rules specify the qualifications for personnel performing the examinations, acceptance criteria for the assessments, and calibration and maintenance requirements for equipment used.
Learning about corrosion protection and its accurate handling requires knowledge of many API standards. Having sufficient knowledge of API standards will provide guidelines and recommendations for various aspects related to corrosion protection, such as material selection, design and construction practices, inspection and testing procedures, and maintenance and repair requirements.
PetroSync provides API 653 training that will equip you with the necessary knowledge and skills not only to perform corrosion protection but also to conduct storage tank inspections in compliance with industry standards and regulations.
Our training program consists of in-depth course materials, study guides, and practice exams that cover all aspects of the API 653 exam to help you prepare better for storage tank inspection.
Our 5 days training program is designed with detailed discussions on engineering knowledge for in-service storage tanks, with a focus on API’s syllabus. The program covers six areas and includes practical case studies to provide you with hands-on experience. Join PetroSync’s API 653 – Tank Inspection, Repair, Alteration, and Reconstruction training course and build your confidence in making informed decisions regarding storage tank inspection and storage tank repair. Wait no more, reserve your spot now!
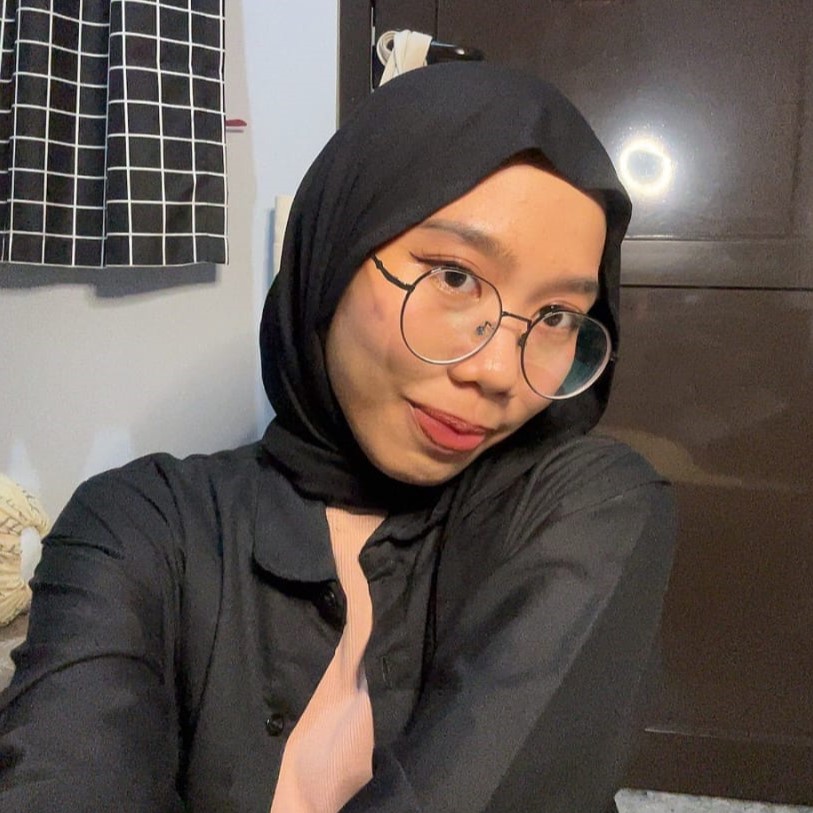
SEO specialist by day, fact-checker by night. An avid reader and content writer dedicated to delivering accurate and engaging articles through research and credible sources.