Risk analysis plays a vital role in the oil and gas, petrochemicals, and power plants industry. The risk analysis approach is essential for identifying and mitigating potential risks, and ensuring the safety, reliability, and efficiency of operations in these sectors. By conducting a thorough risk analysis, the in-charge engineers can proactively manage and address potential hazards, protecting personnel, assets, and the environment.
What Is Risk Analysis in the Oil and Gas Industry?
Risk analysis is the process of identifying and evaluating potential future events that can negatively affect a company. By conducting a risk analysis, an organization performs risk management to better understand what may occur, the financial implications of that event occurring, and what steps it can take to mitigate or eliminate that risk
In oil and gas industry, this approach involves examining the potential risks associated with the equipment or components, determining the likelihood of failure, and evaluating the potential consequences of failure.
Oil and gas industries face several types of risks such as operational, financial, technical, environmental, and regulatory risks. Equipment failure, natural disasters, security breaches, commodity price fluctuations, regulatory changes, and geopolitical instability are some of the causes of the risks.
What Are The 5 Most Common Responses to Risk?
The five most common responses to risk are:
1. Risk Avoidance
Risk avoidance is a strategy used to reduce risk by refraining from engaging in activities that could have adverse effects on the organization. In the context of the oil and gas industry, this could mean not pursuing certain investments or refraining from launching specific product lines to steer clear of potential losses and unfavorable outcomes.
2. Risk Reduction
This approach to risk management aims to reduce potential losses instead of entirely eliminating them. By acknowledging the risks involved, the focus lies on containing any losses and preventing their escalation. An analogy in this sector would be implementing preventive measures to ensure safety and minimize the impact of potential incidents.
3. Risk Sharing
In the context of the oil and gas industry, risk sharing involves distributing the possibility of loss among multiple stakeholders. This practice is akin to how a corporation operates, where various investors pool their resources, and each only assumes a portion of the risk associated with potential setbacks in the enterprise.
4. Transferring Risk
One way to handle risk is by contractually transferring it to a third party, such as obtaining insurance coverage to safeguard against potential property damage or injuries. By doing so, the risks associated with the property shift from the owner to the insurance company, providing added protection and peace of mind.
5. Risk Acceptance and Retention
Even after employing various risk sharing, risk transfer, and risk reduction strategies within the oil and gas industry, some level of risk will persist. It is practically impossible to eliminate all risks entirely, except through risk avoidance. The remaining risk that persists despite these measures is known as residual risk.
How To Do Risk Analysis?
In general, there are two main steps in doing risk analysis.
1. Hazard Identification
In risk analysis, it’s crucial to identify potential hazards that could endanger personnel, equipment, or the environment. This process, known as hazard identification, plays a critical role in the analysis. Effective hazard identification in the oil and gas industry helps to ensure the safety of workers and facilities.
2. Risk Analysis / Risk Evaluation
The first step in risk analysis is to identify the equipment that is subject to RBI and the potential damage mechanisms that can affect it. Next, actively determine the likelihood of failure by considering the probability of each damage mechanism occurring and the equipment’s susceptibility to the damage.
Following this, actively determine the consequences of failure by evaluating the potential impact of equipment failure. To calculate the risk, actively combine the likelihood of failure and the consequences of failure. Finally, actively prioritize inspection equipment based on the calculated risk and develop an inspection plan that includes the frequency and type of inspection.
How To Do Inspection Planning Based on Risk Analysis?
The process of inspection planning based on risk analysis involves identifying and assessing potential risks linked to a system or process. The goal of this activity is to ensure that the system or process operates safely, efficiently, and effectively by prioritizing and focusing on critical components that are more likely to fail or pose a higher risk. Below are the common steps of inspection planning after doing the risk analysis.
1. Inspection Plan
After performing risk analysis, the involved personnel can create an inspection plan that details the type and frequency of inspections required for each component, utilizing the risk analysis results. Additionally, establish criteria for determining when an inspection is necessary.
2. Plan Execution
Then, the personnel executes the inspection plan by scheduling inspections, delegating responsibilities, and ensuring the appropriate resources are available to implement the inspection plan.
3. Inspection Plan Tracking and Assessment
Continuously monitor and evaluate the effectiveness of the inspection plan, making any necessary changes or adjustments based on feedback and any modifications made to the system or process being inspected.
The inspection plan outlines the frequency and type of inspections required for each component and also specifies the criteria for determining when an inspection is necessary. This process enables organizations to identify potential risks actively, develop an effective plan to manage them and reduce the likelihood of failures, thus improving the overall safety and reliability of the system or process.
Inspection Effectiveness
In Risk-Based Inspection (RBI), inspection effectiveness plays a crucial role in managing risk by ensuring that the inspection and maintenance activities are targeted to high-risk areas and equipment.
The effectiveness of the inspection is the extent to which it can identify and evaluate the damage, defects, or degradation of the equipment or asset. If the inspection is ineffective, the organization may overlook potential problems, leading to increased risk and potentially severe consequences.
Therefore, as a part of the risk analysis process, RBI evaluates the effectiveness of the inspection. This evaluation considers various factors such as:
- Inspection Frequency
- Inspection Techniques’ quality, and
- Personnel Qualifications Performing the Inspection.
Through the RBI analysis, areas and equipment that require more frequent and effective inspection and maintenance are identified. This ensures that resources are allocated to the high-risk areas and equipment, and inspection and maintenance activities are concentrated on addressing potential issues.
Joining API 580 and 581 – Risk-Based Inspection & Base Resource Document course can be very advantageous if you are working in the oil and gas sector. PetroSync’s API 580 and API 581 training covers the basics of risk-based inspection and highlights the significance of inspection planning.
Risk-based inspection (RBI) is a well-organized approach that involves evaluating the risks linked with equipment failure and giving priority to inspection tasks based on the level of risk.
If you are either engineer, supervisor, or manager in the oil and gas industry can develop a thorough understanding of the RBI process by taking PetroSync’s API 580 and API 581 training. This includes learning how to recognize, evaluate, and control risks efficiently. In addition, you will also learn how to develop and implement an RBI program, including inspection planning, which is a critical component of the process.
Inspection planning, which involves deciding on how often and what type of inspections are required for each piece of equipment, and setting inspection priorities based on risk levels are also covered in the training. Enroll in PetroSync’s Risk Based Inspection training and optimize your inspection methods with us!
Credit Header Image: Freepik
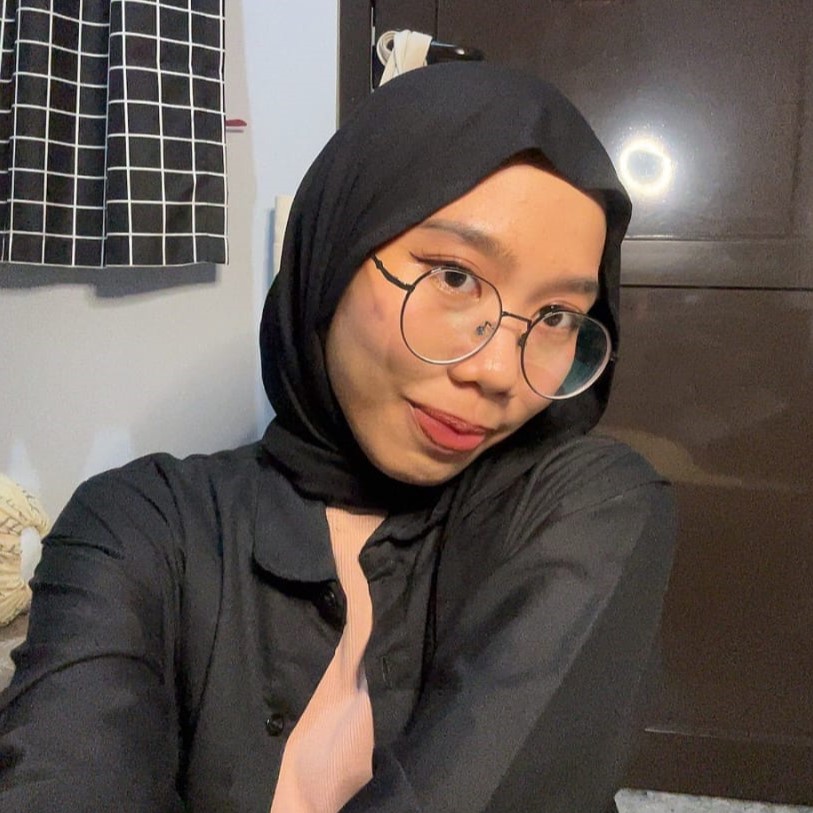
SEO specialist by day, fact-checker by night. An avid reader and content writer dedicated to delivering accurate and engaging articles through research and credible sources.