Risk Based Inspection is proactive strategy plays a pivotal role in preventing catastrophic failures, minimizing downtime, and optimizing maintenance costs. Risk-based inspection is applied across industries due to its systematic approach to managing the integrity of equipment and assets.
Let’s embark on a journey to understand the key aspects of Risk Based Inspection.
What Is Risk-Based Inspection?
The Risk-Based Inspection (RBI) methodology is a quantitative technique used to develop an inspection plan based on risk assessment principles for stationary pressurized equipment, which includes items like pressure vessels, pipes, tanks, pressure relief devices, and heat exchanger tube bundles.
As the name suggests, RBI involves inspecting assets based on their risk levels. It’s a data-driven approach using risk matrix that assesses the likelihood of equipment failure and its consequences. By prioritizing inspections, organizations can allocate resources efficiently, focusing on critical components that pose the highest risk.
What Are The Key Components of Risk-Based Inspection?
To implement RBI effectively, it’s essential to understand its key components:
1. Risk Assessment
Risk assessment is an important process where we carefully evaluate the possible dangers associated with equipment failure. This evaluation considers several factors, such as how old the equipment is, its current condition, and the particular environment where it operates.
2. Probability of Failure
Risk-based inspection (RBI) uses a meticulous method to evaluate the likelihood of equipment failure. It can be achieved by studying historical data and applying advanced predictive analytics. Through this analysis, RBI identifies components at greater risk of failing. These high-risk parts then undergo more detailed inspections, ensuring efficient resource allocation to resolve issues and prevent costly breakdowns.
3. Consequence Analysis
During this stage, we assess what could happen if an asset fails. This includes looking at safety risks, environmental impact, and financial losses. When it comes to items with high potential consequences, we conduct more frequent and thorough inspections.
What Are The Benefits of Risk-Based Inspection?
Risk-Based Inspection (RBI) offers several key benefits that highlight its significance in diverse industrial applications.
1. Cost Savings
RBI streamlines how often we inspect equipment, which cuts down on unnecessary checks and the costs tied to them. It ensures that we allocate resources to the areas that require them the most, preventing excessive maintenance.
2. Enhanced Safety
Risk-Based Inspection (RBI) plays a pivotal role in enhancing safety by concentrating on high-risk components, allowing us to detect and address potential failures before they materialize. This proactive approach significantly reduces the likelihood of unexpected equipment breakdowns and associated safety risks.
3. Increased Asset Reliability
Consistent inspections and maintenance of critical components are key practices that extend the lifespan of assets while minimizing unplanned downtime. These routine checks help identify and address potential issues before they escalate, ensuring the continued reliability and efficiency of equipment and systems.
How Is Risk-Based Inspection Applied in The Real World?
RBI is widely used in industries such as oil and gas, petrochemicals, and manufacturing. Let’s explore some real-world applications:
1. Oil Refineries
Within the oil and gas industry, Risk-Based Inspection (RBI) assumes a critical role in preserving the safety and reliability of equipment. RBI is primarily employed to assess the potential risks associated with equipment such as pipelines, storage tanks, and valves. This process serves to prioritize inspection activities by focusing on components with the highest risk levels, thereby decreasing the workload on less critical elements.
The advantages of RBI within the oil and gas sector are substantial. It substantially diminishes the occurrence of unforeseen shutdowns by proactively addressing potential failures. Moreover, RBI augments safety standards significantly by identifying and mitigating high-risk areas, thus averting accidents and protecting the environment.
Furthermore, RBI contributes to the extension of equipment lifespans by identifying areas necessitating immediate attention and those capable of extended, secure operation.
2. Power Plants
In the petrochemical industry, Risk-Based Inspection (RBI) is an indispensable instrument for evaluating the risks associated with equipment such as reactors and storage tanks. Its primary application revolves around ensuring the secure operation of petrochemical plants. RBI enables the methodical assessment of the condition of diverse components, essential for accident prevention and equipment integrity preservation.
The advantages of RBI within the petrochemical sector are noteworthy. It significantly enhances safety standards by recognizing high-risk areas and ensuring the implementation of appropriate risk mitigation measures. This proactive approach serves to prevent accidents, minimize environmental impact, and protect both personnel and neighboring communities.
3. Petrochemical Plants
In the power and energy industry, Risk-Based Inspection (RBI) plays a fundamental role in evaluating the condition of critical components, such as turbines, generators, and boilers. The primary application of RBI in this sector is to ensure consistent and uninterrupted energy production. RBI accomplishes this by systematically assessing the risks associated with each piece of equipment.
The benefits of RBI in the power and energy industry are extensive. It helps prevent unanticipated failures, thereby ensuring a stable and uninterrupted energy supply. RBI enhances safety standards by identifying and addressing potential risks, reducing the likelihood of accidents with potentially catastrophic consequences.
Additionally, RBI plays a vital role in minimizing operational costs by optimizing maintenance efforts, extending the longevity of equipment, and reducing unplanned downtime. These cost-effective strategies are essential for the profitability and reliability of the power and energy sector.
4. Chemical Plants
Within the chemical industry, Risk-Based Inspection (RBI) stands as a critical instrument for evaluating the potential risks associated with equipment such as vessels, pumps, and piping. Its primary application is to guarantee the secure handling and processing of chemicals within chemical plants. RBI conducts a systematic evaluation of equipment condition and risk potential, making it a pivotal aspect of chemical plant operations.
The advantages of RBI within the chemical sector are far-reaching. It significantly reduces the potential for chemical accidents, which can have severe consequences for both human safety and the environment. By enhancing safety standards, RBI helps maintain a safer work environment for employees and minimizes the impact on the surrounding community.
5. Aviation Industry
In the aviation industry, Risk-Based Inspection (RBI) is employed to assess the condition of aircraft components such as engines, landing gear, and fuel systems. The primary application of RBI in aviation is to ensure the safety and efficiency of flight operations. RBI systematically evaluates the risks associated with each component, aiding in the prevention of unexpected failures that could lead to accidents.
The benefits of RBI in the aviation sector are profound. It enhances aviation safety by identifying potential risks before they can lead to accidents, ensuring a higher level of confidence among passengers. By proactively addressing risks, RBI results in fewer flight disruptions, which is critical for maintaining flight schedules and customer satisfaction.
What Are FAQs Related to Risk-Based Inspection?
Here are some commonly asked questions regarding Risk-Based Inspection.
1. What Is The Primary Goal of Risk-Based Inspection?
The primary goal of RBI is to optimize inspection strategies by focusing resources on high-risk components, thereby enhancing safety and reducing maintenance costs.
2. How Does RBI Differ from Traditional Inspection Methods?
Unlike traditional time-based inspections, RBI prioritizes inspections based on risk assessments, ensuring that critical components receive more attention.
3. Is Risk-Based Inspection Suitable for All Industries?
While RBI applies to various industries, its effectiveness depends on the complexity and criticality of the assets involved.
4. Can RBI Prevent All Equipment Failures?
While RBI significantly reduces the risk of failures, it cannot guarantee complete prevention. However, it minimizes the likelihood of catastrophic incidents.
5. Are Specialized Tools or Software Required for Implementing RBI?
Yes, specialized software and expertise are essential for performing risk assessments and optimizing inspection plans effectively.
6. How Often Should RBI Assessments Be Conducted?
The frequency of RBI assessments varies depending on the industry and asset type but typically ranges from annually to every few years.
Risk Based Inspection is a proactive and data-driven approach that plays a vital role in asset integrity management. By prioritizing inspections based on risk assessments, organizations can enhance safety, reliability, and cost-effectiveness. Embracing RBI is a smart move for industries that prioritize the well-being of their assets and the safety of their workforce.
PetroSync understands the significance of RBI and offers specialized training to empower you with the knowledge and skills needed to master RBI methodology. Through our API 580 & 581 training course, you can gain a comprehensive understanding of risk assessment principles and risk management best practices, ensuring that you can effectively implement RBI strategies within your organization. Invest in the future of your assets and the safety of your operations with PetroSync’s industry-leading training.
Credit header image: Freepik
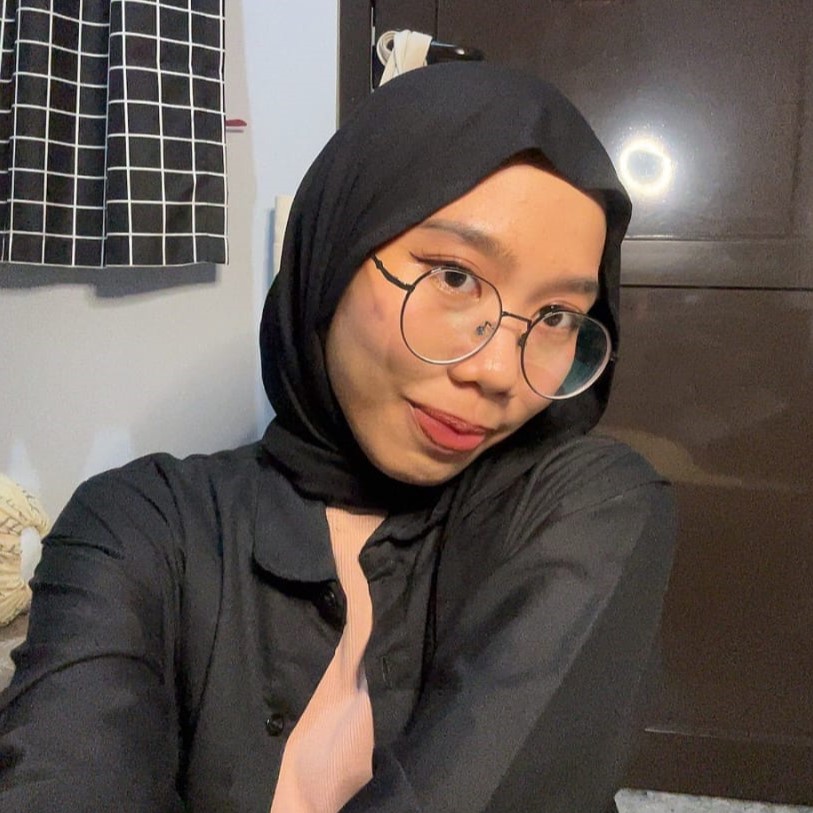
SEO specialist by day, fact-checker by night. An avid reader and content writer dedicated to delivering accurate and engaging articles through research and credible sources.