The upstream process is the first step in finding and extracting oil and gas. It involves searching for reservoirs and drilling and completing wells. In this article, we will explore two of the upstream activities: well completion, including its procedures, and well workover.
What Is Well Completion?
Well completion, which incorporates the steps taken to transform a drilled well into a producing one, is a crucial step in the production of oil and gas after drilling activity is performed. The process involves the installation of equipment both underground and aboveground to create a safe and efficient environment for production.
Well-completion requires careful attention to detail in terms of installation, maintenance, and ongoing monitoring to ensure maximum safety and productivity.
In the process, coiled tubing may be needed as it plays a crucial role in the completion of wells. This flexible tubing is utilized for well-intervention tasks such as cleaning, pumping, and logging.
What Are The Steps of Well Completion?
Well-completion involves several steps that need to be taken to make sure the well can produce oil or gas effectively and efficiently. Below are the common steps involved in performing well-completion to ensure a safe and efficient production environment for oil and gas.
1. Casing Process
The first step is to install the steel casing and cement it in place to prevent the well from closing in upon itself while avoiding groundwater contamination. This casing acts as a barrier between the wellbore and the surrounding rock formations. Some types of casing (placed based on different levels of the well) are production casing, intermediate casing, surface casing, conductor casing, liner, and liner tieback casing.
2. Hole Completions
After the casing is installed and cemented, the next step is to create holes in the casing using a perforating gun. This allows the oil or gas to flow into the wellbore for extraction. There are two types of hole completions, namely open hole and cased hole.
3. Perforation
It requires perforation for the cased hole. This procedure entails inserting a perforation gun and a device for locating reservoirs into the wellbore. Once the casing has been perforated, a completion string consisting of production tubing, packers, and other equipment is lowered into the wellbore.
4. Gravel Packing
Certain wells necessitate the use of filtration systems to prevent sand from entering the well stream. Along with installing a casing and a liner, gravel packing is employed as a measure to keep the well stream clear of sand.
5. Production Tubing Placement
The production tubing runs down the center of the casing and allows the oil or gas to flow to the surface, while the packers create a seal between the tubing and casing to prevent fluids from entering the space between them. Valves, gauges, and chokes may also be installed to regulate the flow of oil or gas and control well pressure.
6. Production Tree Installation
For the final part, the wellhead is installed on top of the casing and connected to the surface equipment. The wellhead is a collection of valves, pipes, and fittings that allow the materials to be transported to storage tanks or processing facilities. It also provides a means for monitoring and controlling the well pressure and flow rate.
Safety is of utmost importance during the entire well-completion process. It is crucial to design and construct a well-completion that prevents any accidents or leaks that may cause harm to people or the environment. Moreover, it is necessary to regularly maintain and monitor the well to ensure its continued safety and productivity throughout its lifespan.
What Are Some Types Well Completion?
There are some types of well completion and each method has its advantages and considerations. The selection depends on the specific requirements of the well and the desired production outcomes.
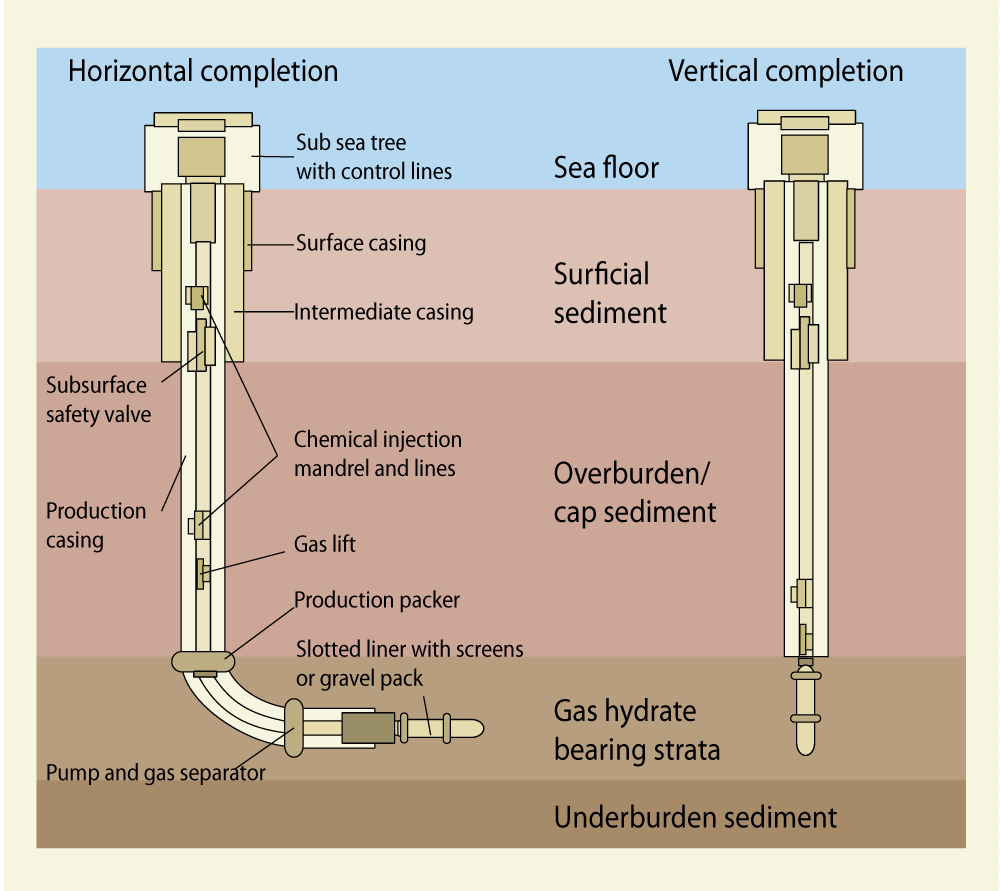
1. Barefoot Completion
In a barefoot completion, no casing or tubing is used to line the wellbore. Instead, the well is drilled directly into the reservoir rock. This type of completion is used in certain situations where the rock formation is strong and stable enough to support the wellbore without the need for additional support from casing or tubing. Barefoot completions can be cost-effective but may require careful monitoring to prevent sand or other materials from entering the wellbore.
2. Open Hole
An open hole completion refers to a wellbore that has been drilled without any casing or tubing being set in the drilled section. This means that the well is left “open” to the surrounding rock formation. Open hole completions are common during the drilling phase and are often followed by other completion methods, such as cased hole or liner completions, to provide support and control for production.
3. Open Hole Completion
An open hole completion involves completing the well without setting casing or liners in the open hole section. This method is used when the formation is stable enough to support itself without the need for additional support. It allows for direct contact between the reservoir and the wellbore, which can be beneficial in certain production scenarios. However, it requires careful planning and evaluation to ensure well integrity and prevent issues like sand production.
4. Liner Completions
A liner completion involves running a casing liner into the wellbore without extending it to the surface. The liner is typically set above the production zone to provide support and prevent the wellbore from collapsing. Liner completions are often used in deviated or horizontal wells where full casing strings may not be necessary. They help reduce costs while still providing structural integrity to the well.
5. Perforated Liner
In a perforated liner completion, holes or perforations are made in the casing liner to allow oil or gas to flow from the reservoir into the wellbore. These perforations are typically made using specialized tools and techniques to ensure proper placement and prevent damage to the casing. Perforated liners are common in wells where selective production from specific zones within the reservoir is desired.
6. Perforated Casing
Similar to a perforated liner, perforated casing involves creating holes or perforations in the casing itself to allow for fluid flow from the reservoir into the wellbore. Perforated casing is used in cased hole completions where the casing extends throughout the wellbore. This method allows for controlled production from different zones within the reservoir by perforating specific sections of the casing.
7. Cased Hole Completion
A cased hole completion involves running casing (metal pipe) into the wellbore and cementing it in place. This creates a sealed environment between the wellbore and the surrounding rock formation.
Cased hole completions provide structural support to the well, prevent formation fluids from entering the wellbore, and allow for controlled production through perforations or other completion methods. They are common in most oil and gas wells to ensure safe and efficient production operations.
These types of well completions vary in complexity and are chosen based on factors such as reservoir characteristics, well design, and production objectives.
8. Multiple Completions
Multiple completions refer to a method used in certain cases to best control reservoir operations. It involves setting up the well with multiple tubing strings or tubing-casing duals. This approach allows for the simultaneous production from two or more reservoirs through a single wellbore.
However, such setups can be quite complex, leading to challenges during both completion and subsequent workover operations. Therefore, multiple completions are typically considered only in special situations, such as areas with high drilling costs or limited space for drilling wells, like offshore locations or densely populated areas. While the economic benefits of multiple completions can be attractive if everything goes smoothly, it’s essential to carefully weigh the operational costs involved in such setups.
What Happens After Well Completion?
After the well completion process, especially in cased hole completions which are common in many wells, the next step involves creating a connection between the wellbore and the surrounding formation. This connection is crucial for the flow of fluids such as oil or gas. To achieve this, perforation guns are used to create openings or holes in the casing or liner. These perforations allow the reservoir fluids to flow into the wellbore, initiating the production phase of the well.
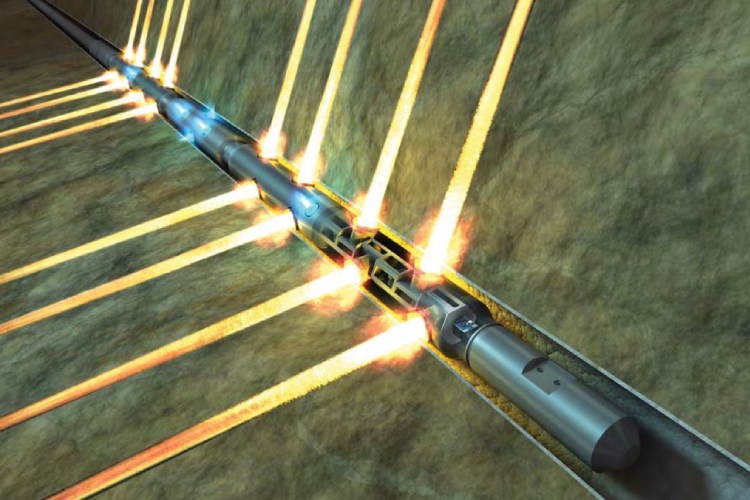
Once the perforations are made, the well undergoes a series of tests to evaluate its productivity and ensure that it is functioning as expected. These tests may include flow rate measurements, pressure testing, and fluid sampling. Engineers and technicians closely monitor these tests to gather important data about the reservoir and the well’s performance.
What Is The Importance of Well Completion?
The importance of well completion lies in its direct impact on the successful production and depletion of a reservoir. When a well is completed effectively, it allows for the efficient extraction of oil, gas, or other fluids from the underground reservoir. Well completion ensures that the connection between the wellbore and the reservoir is properly established, allowing for the flow of fluids to the surface.
Additionally, well completion plays a crucial role in ensuring the safety and integrity of the well. A well that is properly completed is less likely to encounter issues such as leaks or mechanical failures, which can disrupt production and pose environmental risks. Furthermore, well completion sets the stage for future workover operations, which may be needed to maintain or enhance well performance over time.
What Is Well Workover?
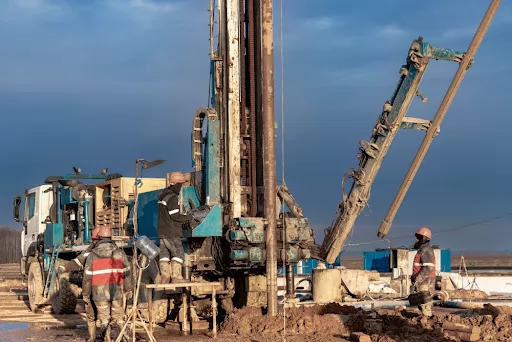
Well workover is the process of repairing and maintaining an existing well to enhance its lifespan and performance even beyond its original state. The activities include removing debris, repairing or replacing components, and performing chemical treatments.
After the issues are identified, in-field personnel must select the appropriate equipment and methods for repair. Sometimes, special treatments and chemicals may also be applied to protect the well against corrosion and other possible damage.
Why Is Well Workover Important?
Workover needs to be done when a well completion does not meet its expected condition. In order for a workover to occur, it is necessary to stop the flow of oil or gas from the well, which is also known as “killing” the well. Since this is a complex process, workovers are planned well in advance. Several reasons become the factors of doing workover as follows.
- Well deterioration
- Competitive drainage
- Changing reservoir conditions
- Insufficient injection or production rates
- The need for supplementary recovery projects
- Compliance with regulations
- Gathering reservoir data
Whether it’s repairing, enhancing, or finishing well, this workover process plays a significant role in maximizing the efficiency and profitability of oil and gas operations.
PetroSync offers Well Completion and Workover training where you can learn the fundamentals of well completion and workover, including technical knowledge of completion techniques, equipment, perforating methodologies and techniques, wellhead and downhole equipment, hydraulic fracturing, acidizing, squeeze cementing, and scale removal techniques.
Throughout our 5-days Well Completion and Workover course, our instructor will offer assistance and feedback to help you navigate the well-completion and workover process. Upon completion of the course, you will possess a thorough comprehension of the process and be equipped to utilize your newly acquired expertise in the field.
Enroll today and master the well completion and workover skills with PetroSync!
Credit header image: Freepik.com
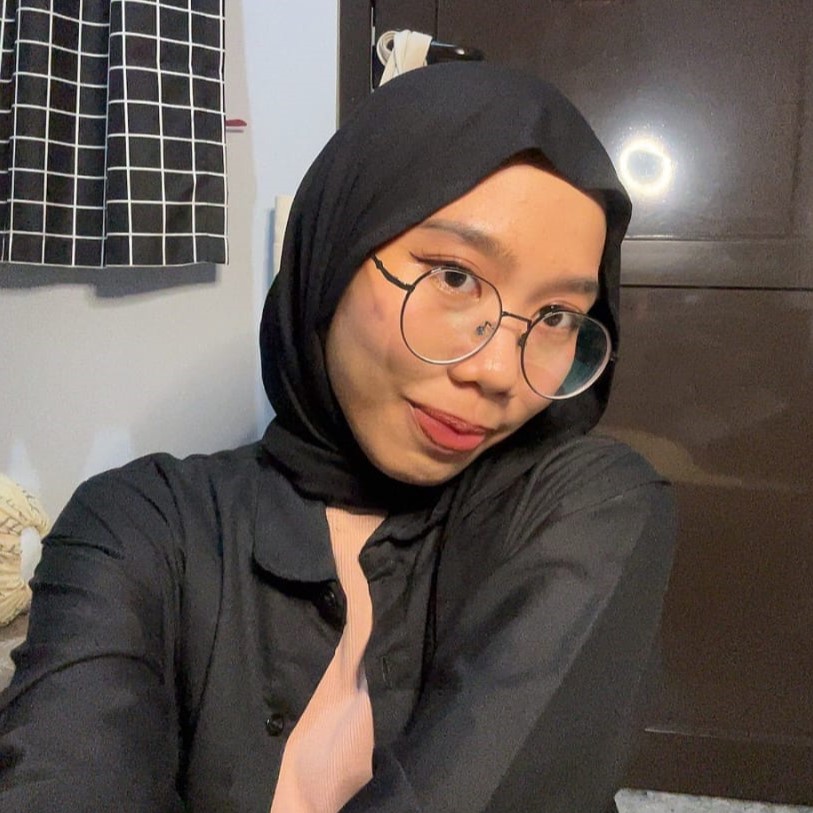
SEO specialist by day, fact-checker by night. An avid reader and content writer dedicated to delivering accurate and engaging articles through research and credible sources.