Welding plays a crucial role in engineering, forming joints that endure over time and under stress. In this article, we’ll explore the details of achieving excellence in welded joints, examining the different factors that contribute to their success.
What Is Welded Joints?
A welded joint is a connection created by fusing two or more pieces of metal together through the application of heat, forming a point or edge where two or more pieces of metal or plastic are joined together. This process involves melting the edges of the metal components and allowing them to cool, resulting in a strong and durable bond.
Welded joints are commonly used in various industries, including construction and manufacturing, to create sturdy structures and components. The goal is to seamlessly unite the materials, ensuring they function as a single, cohesive unit. This welding method is crucial for producing everything from bridges and buildings to intricate machinery.
What Are The Common Types of Welded Joints?
A key aspect in understanding welded joints is by knowing the different types of welded joints. Each of the existing welded joints serves a specific purpose in seamlessly connecting metals. From the straightforward butt joint to the versatile T-joint, these welding techniques are the building blocks of numerous projects.
1. Butt Joint Welding
Butt joint welding is a technique where the ends of two pieces of metal are aligned and joined together by applying heat, forming a joint where two pieces of metal are placed together in the same plane, and the side of each metal is joined by welding. This process involves melting the edges of the metal components and allowing them to cool, creating a strong and cohesive connection.
Butt joint welding is commonly used in various industries, including oil and gas, for joining plates, sheets, and pipes. It is known for its simplicity and effectiveness, making it a fundamental method in welding processes. The resulting weld is typically flush and smooth. Below are a few common instances of butt weld joints.
Type of Butt Weld Joint |
Description |
Square | This butt weld joint involves the straightforward alignment of two square-edged metal pieces. |
Single Bevel | In a single bevel joint, one of the metal pieces has an angled edge, facilitating easier welding penetration. |
Double Bevel | Similar to the single bevel, both metal pieces in this joint have angled edges, enhancing the welding process. |
Single J | The single J joint features one metal piece with a J-shaped edge, allowing for effective welding and a strong connection. |
Double J | Both metal pieces in the double J joint possess J-shaped edges, providing increased welding surface and strength. |
Single V | With one metal piece having a V-shaped edge, the single V joint ensures efficient welding and a durable bond. |
Double V | In the double V joint, both metal pieces boast V-shaped edges, optimizing welding effectiveness and joint strength. |
Single U | The single U joint involves one metal piece with a U-shaped edge, facilitating a robust weld and secure connection. |
Double U | Featuring U-shaped edges on both metal pieces, the double U joint enhances welding efficiency and joint integrity. |
The part of the metal’s surface that melts during welding is called the faying surface. Before welding, the faying surface can be shaped to enhance the weld’s strength, known as edge preparation. The preparation may be the same on both sides of the butt joint or different on each side. There are several reasons to prepare faying surfaces:
- Meeting codes and standards.
- Adapting to different metals.
- Achieving deeper weld penetration.
- Creating a smooth appearance.
- Increasing overall strength.
In some cases, the size, shape, and angle of a groove may be specified. If not, the groove can be adjusted to the required dimensions. However, it’s essential to note that wider grooves necessitate more welding.
As the metal thickness increases, the joint design must change for a reliable weld. While a square butt joint may suffice for thin sections, thicker plates or pipes often require a groove to ensure proper penetration.
Common defects in butt joints include burn-through, porosity, cracking, or incomplete penetration. These issues can be prevented by adjusting welding variables.
2. T-Joint Welding
T-joint welding is a method where two pieces of metal are joined together to form a “T” shape, occurring when two pieces meet at a 90-degree angle. In this welding process, one piece of metal is placed perpendicularly to the other, and the joint is created at the intersection.
This type of welding is commonly used in structural applications, providing strength and stability in projects like building frames and other load-bearing structures. The T-joint configuration allows for effective fusion of the metals, ensuring a solid and durable connection.
Welding Style |
Explanation |
Plug Weld | Ensuring effective penetration into the roof of the weld, a plug weld is a method commonly used for creating T-joints. |
Slot Weld | In tee joint welding, a slot weld is employed to guarantee proper penetration and a strong connection between two metal pieces. |
Bevel-Groove Weld | In creating a sloped groove, a bevel-groove weld is utilized in tee joint welding to enhance penetration and strengthen the joint. |
Fillet Weld | Known for its simplicity, a fillet weld is a commonly used style in tee joint welding, providing a sturdy connection between metal pieces. |
J-Groove Weld | The J-groove weld style is employed in tee joint welding to create a J-shaped groove, promoting effective penetration and ensuring a durable joint. |
Melt-Through Weld | T-joints benefit from the melt-through welding style, ensuring the molten metal penetrates thoroughly and creating a robust connection between the metal pieces. |
Flare-Bevel-Groove Weld | In tee joint welding, the flare-bevel-groove weld creates a flared and sloped groove, contributing to effective penetration and strengthening the overall joint. |
T-joints typically don’t need a groove unless the base metal is thick, and welding on both sides can’t handle the load the joint must support. A common issue with T-joints is lamellar tearing caused by joint restriction. To avoid this, welders often use a stopper to prevent deformities in the joint.
3. Corner Joint Welding
Corner joint welding is a method where two pieces of metal meet at a right angle, forming a corner, instances in which two materials meet in the “corner” to form an L-shape. In this welding process, the joint is created at the intersection of the two pieces.
Corner joint welding is commonly used in various applications, especially when constructing structures with square or rectangular sections. This welding technique ensures a solid and secure connection at the corners, providing strength and stability to the overall structure.
Welding Style |
Explanation |
V-Groove | A V-shaped groove is created for effective welding in corner joints. |
J-Groove | Utilized in corner joint welding, a J-shaped groove enhances penetration and joint strength. |
U-Groove | The U-groove style involves shaping a U for better penetration and a robust connection in corner joints. |
Spot | Corner joints benefit from spot welding, where small, concentrated welds secure metal pieces together. |
Edge | In corner joint welding, an edge weld involves joining the edges of two metal pieces for a strong connection. |
Fillet | The simplicity of fillet welding is employed in corner joints for creating a robust connection between materials. |
Corner-Flange | Corner-flange welding involves joining the flanges of two metal pieces at a right angle, ensuring stability in corner joints. |
Bevel-Groove | By creating a sloped groove, bevel-groove welding enhances penetration and strength in corner joints. |
Flare-V-Groove | The flare-V-groove style involves shaping a flared V-groove for effective penetration in corner joint welding. |
Square-Groove or Butt | Square-groove or butt welding creates a square joint for a secure and stable connection between metal pieces in corners. |
4. Lap Joint Welding
Lap joint welding is a method where two pieces of metal overlap and are joined together, essentially a modified version of the butt joint. In this welding process, the joint is created by welding along the overlapping section of the two pieces.
Lap joint welding is commonly used when a strong connection is needed between surfaces that can be overlapped, providing stability and strength to the joined materials. Lap joints are not often applied to thicker materials; instead, they are commonly used for sheet metal. Possible issues with this type of welding joint include lamellar tearing or corrosion arising from overlapping materials. However, with proper technique and adjusting variables as needed, these challenges can be avoided.
5. Edge Joint Welding
Edge joint welding is a method where the edges of two pieces of metal are joined together, often applied to sheet metal parts that have flanging edges or are placed at a location where a weld must be made to attach to adjacent pieces.
In this welding process, the connection is formed by welding along the adjoining edges of the two metal pieces. Edge joint welding is commonly used when a strong and secure bond is needed along the edges of materials, providing stability and cohesion to the joined pieces.
The ability of a welded joint to endure forces depends on the joint design and weld integrity, with certain joint styles better suited for specific forces. The welding process significantly influences joint design selection, as each process has unique characteristics impacting its performance. Factors such as travel rate, penetration, deposition rate, and heat input also affect welds in various joint designs.
Welding Style |
Explanation |
U-Groove | The U-groove style is used for edge joints, forming a U shape to enhance penetration and connection. |
V-Groove | Employed in edge joints, the V-groove style creates a V shape for effective welding and joint strength. |
J-Groove | Utilized for edge joints, the J-groove style forms a J shape, promoting efficient penetration and a durable connection. |
Corner-Flange | In edge joint welding, the corner-flange style involves joining the flanges of two metal pieces at a right angle for stability. |
Bevel-Groove | Enhancing penetration and strength in edge joints, the bevel-groove style creates a sloped groove. |
Square-Groove | Square-groove welding for edge joints forms a square joint, ensuring a secure and stable connection between metal pieces. |
Edge-Flange | Used in edge joint welding, the edge-flange style involves joining the edges of two metal pieces with flanges for added stability. |
Understanding the types of welded joints is vital for you as it enables you to choose the most appropriate joint design for a given project. This knowledge ensures that the welding work aligns with industry standards and project specifications, contributing to the overall structural integrity of the components. It enhances the durability and reliability of welded structures, crucial factors in applications where performance and safety are paramount.
In the context of using piping codes like ASME B31.3 or API 570, familiarity with various welded joint types is indispensable. These codes often prescribe specific welding procedures and joint designs to ensure the safety and functionality of piping systems.
Understanding the importance of following the industry codes, PetroSync equips you with ASME B31.3 training and API 570 training. Our courses are created to ensure you gain thorough knowledge aligned with international standards for piping.
By focusing on the details of proper welding procedures, joint designs, and compliance requirements, PetroSync‘s training goes beyond the usual. You not only become proficient in meeting these standards but also develop a profound understanding of how to apply them effectively in practical welding situations.
Credit header image: iStock
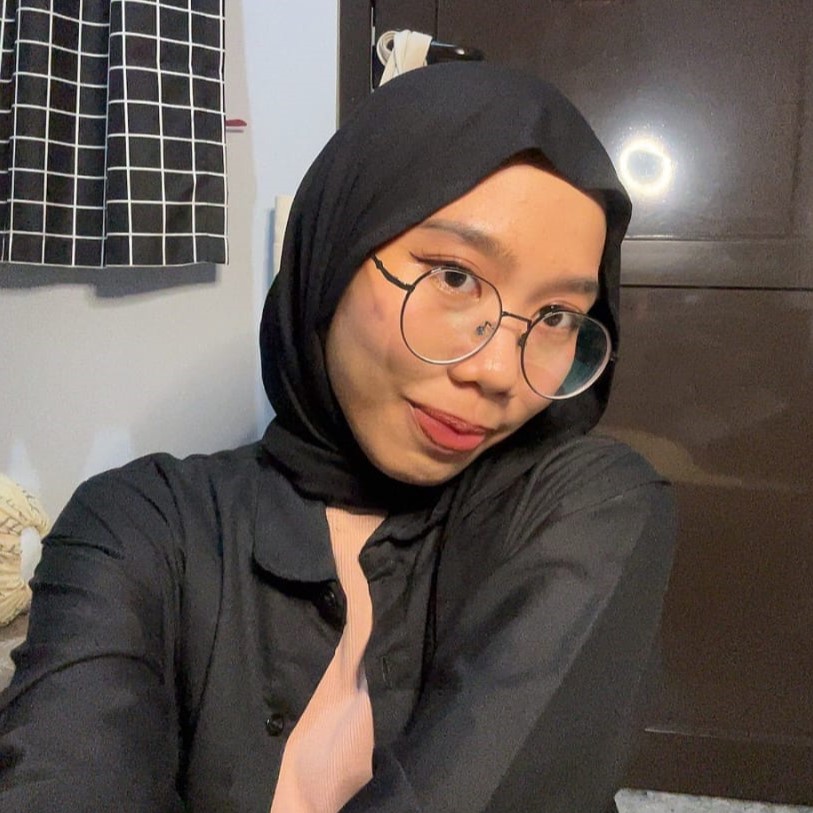
SEO specialist by day, fact-checker by night. An avid reader and content writer dedicated to delivering accurate and engaging articles through research and credible sources.