There are two types of equipment in the oil and gas industry: static equipment and rotating equipment. Static equipment refers to machinery or devices that stay in one place and do not have moving parts during normal operation. Let’s explore the importance, functions, and applications of static equipment in different sectors of the oil and gas industry.
What Is Static Equipment?
Static equipment refers to machinery or devices that stay in one place, do not have moving parts like pumps or compressors, and do not move during normal operation. These are usually used in industries like manufacturing, oil and gas, and power generation.
Examples of static equipment include tanks, pressure vessels, heat exchangers, and pipes. They are designed to handle specific tasks like storing liquids, containing high-pressure gasses, or transferring heat between fluids. Static equipment plays a crucial role in various industrial processes by providing necessary infrastructure for production and operations.
How Many Types of Static Equipment Are There?
There are several types of static equipment used in various industries. Some common types include tanks, pressure vessels, heat exchangers, columns, and piping systems. These static equipment types serve different purposes such as storing liquids, handling high-pressure gasses, and transferring heat between fluids.
1. Heat Exchangers
A heat exchanger is a system used to transfer heat between a source and a working fluid, without them mixing together. This means that heat can move between the two fluids without any physical contact between them.
It is considered part of static equipment because heat exchangers are typically designed to stay in one place and do not have moving parts during normal operation. They are stationary and are used in various industries such as power plants, chemical processing, and HVAC systems to control temperatures and transfer heat efficiently between fluids like water, air, or gasses. Their stationary nature and specialized design make them an essential component of static equipment used in industrial processes.
2. Pressure Vessels
A pressure vessel is a container designed to hold gasses or liquids at a pressure substantially different from the ambient pressure and is made to withstand high pressures safely without leaking or rupturing.
Pressure vessels are considered part of static equipment because they do not have moving parts during normal operation. Unlike dynamic equipment like pumps or compressors, pressure vessels remain stationary while performing their function of containing pressurized substances. They are vital in various industries for storing and transporting gasses or liquids under pressure, such as in chemical processing plants, oil refineries, and power generation facilities.
3. Distillation Column
A column is a tall, vertical structure typically used in industrial processes, produced for the chemical and petrochemical industry, for refineries, and for the gas and food industry. It works by allowing different components of a mixture to rise or fall based on their properties like density or volatility.
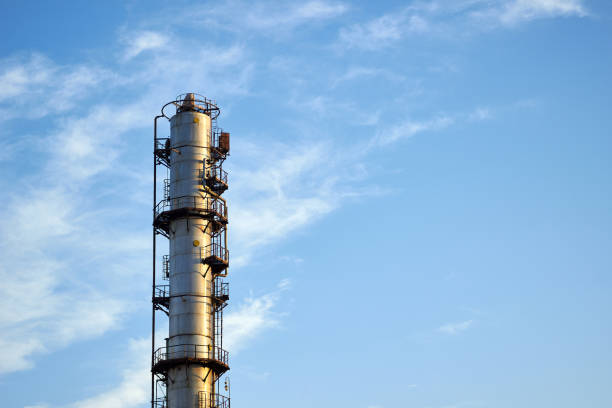
Columns are considered part of static equipment because they do not have moving parts during regular operation. Unlike pumps or compressors that actively move fluids, columns rely on natural forces like gravity and phase separation to perform their function. They are stationary components that play a vital role in various industries such as oil refining, chemical processing, and wastewater treatment, aiding in the separation and purification of substances for production purposes.
4. Atmospheric Storage Tank
An atmospheric storage tank is a type of container that stores products at the same pressure as the atmosphere at the location of the tank, and it is used to store liquids or gasses at atmospheric pressure, which means it is not pressurized. These tanks are commonly used in industries like oil and gas, chemical processing, and water treatment.
Atmospheric storage tanks are considered part of static equipment because they remain stationary and do not have moving parts during their normal operation. They are designed to store materials like crude oil, water, chemicals, or natural gas without needing additional pressure to keep the contents inside. This distinguishes them from pressurized vessels like boilers or high-pressure cylinders, which require pressure to contain their contents safely.
Because atmospheric storage tanks do not rely on pressurization, they are simpler in design and typically easier to maintain compared to pressurized equipment. They are an essential part of static equipment used in various industries for storing and handling liquids or gasses under normal atmospheric conditions.
5. Aboveground Storage Tank
An aboveground storage tank is a large container used to store liquids such as oil, chemicals, or water above the ground level. These tanks are usually made of steel and have a fixed position in a facility or an outdoor area. They are different from underground tanks, which are buried beneath the ground.
Aboveground storage tanks are considered part of static equipment because they are designed to remain stationary and hold substances without the need for constant movement or agitation. This static nature distinguishes them from dynamic equipment like pumps or compressors, which are used to move fluids or gasses.
6. Air cooled exchangers
An air-cooled exchanger, also known as heat rejection equipment where the excess process heat is rejected to the atmosphere, is a type of equipment used to cool fluids, such as water or oil, by using ambient air. It consists of a series of tubes or fins through which the hot fluid flows, while cool air is blown over the tubes or fins to remove heat and lower the temperature of the fluid.
Air heat exchangers are fixed in place within industrial facilities and serve the specific purpose of heat exchange without requiring mechanical movement. This static nature makes them suitable for applications where continuous cooling or heat exchange is needed without the complexity of dynamic components.
7. Boilers
Power boilers are large vessels designed to generate steam or hot water for various industrial processes or heating purposes by taking the chemical energy stored in fuel, converting it to heat energy in the combustion process, and transferring that heat energy to water to produce steam. They are typically used in power plants, manufacturing facilities, and other industries that require a significant amount of steam or hot water.
Unlike pumps or compressors that are part of dynamic equipment and involve mechanical motion, power boilers rely on the static containment of pressurized fluids (such as water or steam) to generate energy. They are stationary devices that are integral to the production of steam or hot water, playing a key role in providing thermal energy for industrial processes and heating systems.
8. Filters
Filters in static equipment are devices used to remove impurities or contaminants from fluids flowing through the equipment. These impurities can include solid particles, debris, or other substances that may affect the performance or integrity of the equipment. Filters help to ensure that the fluid remains clean and free from harmful substances, thus maintaining the efficiency and reliability of the static equipment.
9. Fired heaters
Fired heaters, serving as a primary source of thermal energy for process heating operations in petroleum refining and chemical plants, are devices used in industries like oil and gas to generate heat by burning fuels like natural gas or oil. They are used to heat up fluids or gasses in processes such as refining, petrochemical production, and power generation. Fired heaters are considered part of static equipment because, unlike rotating machinery like pumps or compressors, fired heaters remain stationary during operation.
10. Furnace
A furnace is an appliance used to generate heat for all or part of a building, commonly found in homes and industries to provide warmth and heat for various applications. Furnaces work by burning fuel such as gas, oil, or coal to produce heat, which is then distributed throughout a building or used for specific processes like melting metals or drying materials.
A furnace is considered part of static equipment because it typically remains in one place and doesn’t have moving parts during its normal operation. Unlike machinery like pumps or compressors that involve mechanical motion, furnaces are stationary and designed to provide consistent heat output without the need for continuous movement. This static nature makes furnaces fall into the category of static equipment used in industrial and residential heating systems.
11. Pig receiver
A pig receiver is a type of equipment used in pipelines to receive and collect cleaning devices called pigs, which are a device that “catches” the cleaning device (“pig”) after it has passed through the pipeline. These pigs are used for maintenance and cleaning purposes inside the pipeline. The pig receiver is designed to safely and efficiently capture the pig as it travels through the pipeline during maintenance activities.
12. Piping
A piping system, which is a network of pipes, fittings, and valves intended to perform a specific job i.e. to transport fluids or gasses within a facility or industrial plant. These pipes are interconnected to form a system that can carry materials like water, chemicals, oil, steam, or air from one place to another.
Piping systems play a crucial role in various industrial activities such as refineries, petrochemical plants, and power plants. In refineries, piping systems are used to transport crude oil, refined products, and various chemicals throughout the facility, enabling different refining processes such as distillation, cracking, and blending. In petrochemical plants, these systems facilitate the movement of raw materials, intermediates, and final products like plastics, solvents, and fuels.
Moreover, in power plants, piping systems are essential for circulating water, steam, and other fluids required for electricity generation, cooling systems, and steam turbines. These systems also include safety features such as valves, pressure gauges, and control systems to ensure efficient and safe operation.
13. Valves
A valve is a device or natural object that regulates, directs, or controls the flow of a fluid (gasses, liquids, fluidized solids, or slurries) by opening, closing, or partially obstructing passages within a system. It is like a door that can be opened or closed to regulate the flow of liquids or gasses through pipes or channels.
Valves play a crucial role in the oil and gas industry by regulating the flow of fluids and gasses throughout the production, refining, and distribution processes. They are used in various applications such as controlling the flow of crude oil, natural gas, and refined products like gasoline and diesel.
What Is The Difference between Static and Rotating Equipment?
The main difference between static and rotating equipment lies in their functionality and movement during operation. Static equipment, which is without moving parts, is comparatively more reliable, such as tanks, pressure vessels, heat exchangers, and pipes.
On the other hand, rotating equipment includes machinery that has moving parts and rotates during operation, such as pumps, compressors, turbines, and motors. Rotating equipment is designed to convert energy and move fluids or gasses, while static equipment provides infrastructure for storage, containment, or transfer of substances without moving parts. Both types of equipment serve distinct purposes in industrial processes and are essential for various applications in different industries.
What Are Some FAQs About Static Equipment?
1. Is Valve A Static Equipment?
Yes, a valve is considered a static equipment because it typically remains stationary and does not have moving parts like pumps or compressors. Valves are fixed in place within a system and are used to regulate, control, or stop the flow of fluids or gases by opening, closing, or partially obstructing passages. They are an essential component of pipelines, industrial processes, and systems where fluid or gas flow needs to be managed.
2. Is A Separator Static Equipment?
Yes, a separator is considered static equipment because it remains in one place and does not have moving parts during normal operation. Separators are used in various industries, such as oil and gas, to separate different components of a mixture, such as oil, gas, and water.
They work by utilizing gravity, centrifugal force, or other separation mechanisms to achieve the desired separation of substances. Separators play a crucial role in processing and refining operations by separating and recovering valuable components efficiently.
3. Is A Compressor Static or Rotary?
A compressor is a rotary equipment because it has moving parts that rotate during operation. Compressors are used to increase the pressure of gasses or air by compressing and reducing their volume.
They work by drawing in gas or air and then mechanically compressing it to a higher pressure before releasing it. Rotary compressors are designed with rotating components such as rotors or blades that create the compression action, distinguishing them from static equipment that remains stationary during operation.
4. What Is Static Equipment Engineering?
Static equipment engineering refers to the specialized field of engineering focused on the design, analysis, construction, and maintenance of static equipment used in various industries, including the stationary components used in various processes of oil and gas exploration, production, refining, and transportation.
This discipline involves applying engineering principles to develop equipment such as tanks, pressure vessels, heat exchangers, and pipes that do not have moving parts during normal operation.
Static equipment engineers ensure that these devices are designed to withstand specific pressures, temperatures, and environmental conditions while meeting safety, regulatory, and performance standards. They also oversee the installation, testing, and ongoing maintenance of static equipment to ensure reliable and efficient operation throughout its service life.
5. What Are The Static Equipment Used in Refinery?
The static equipment used in a refinery includes tanks, pressure vessels, heat exchangers, columns and towers, piping systems, and valves.
In conclusion, static equipment plays a vital role in the oil and gas industry by providing essential infrastructure for storage, containment, and transfer of substances without moving parts. The design, creation, and inspection of static equipment are governed by strict standards to ensure safety, reliability, and compliance with industry requirements. Two prominent standards in this regard are the American Petroleum Institute (API) standards and the American Society of Mechanical Engineers (ASME) codes.
In addition to the standards set by API and ASME, it is essential for engineers and professionals in the oil and gas industry to have thorough knowledge and expertise in handling static equipment.
PetroSync offers API training and ASME training programs specifically designed to equip you with the necessary skills and understanding to work effectively with static equipment. These training courses cover topics such as design principles, inspection techniques, maintenance practices, and compliance with industry regulations. You can invest in your own professional development through API and ASME training with PetroSync.
Credit header image: Vecteezy
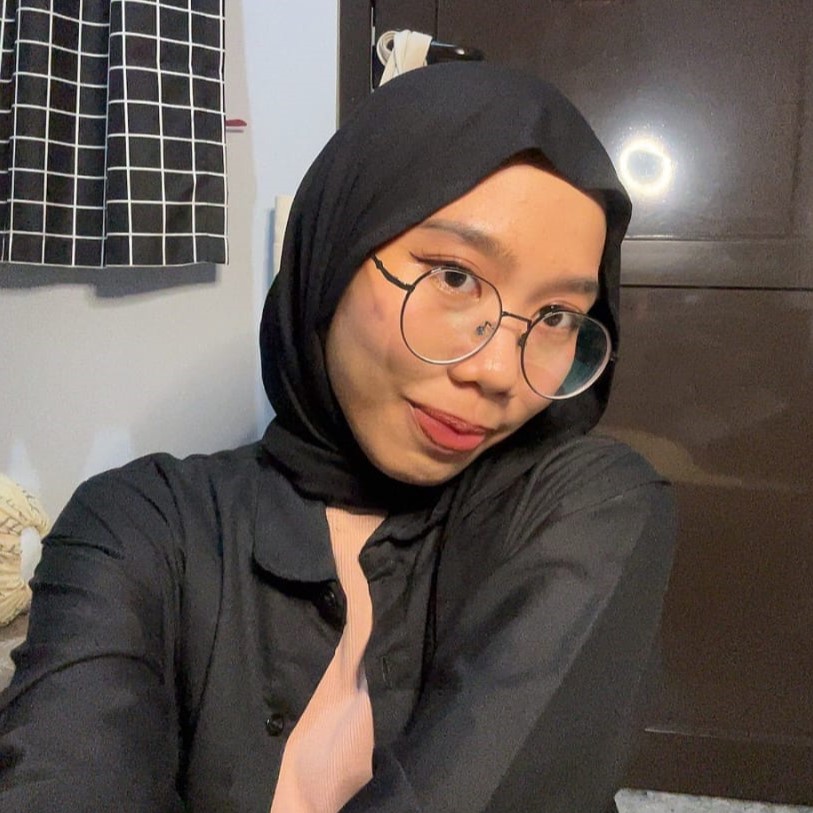
SEO specialist by day, fact-checker by night. An avid reader and content writer dedicated to delivering accurate and engaging articles through research and credible sources.