CTA:Embarking on the journey of implementing the six sigma methodology for reliability is a strategic initiative that holds the potential to significantly enhance the performance and dependability of products, services, and processes. In this article, we delve into the principles and practicalities of incorporating Six Sigma into reliability practices as a way to understand how to seamlessly integrate Six Sigma principles into reliability efforts.CTA:
What Is Six Sigma Methodology?
CTA:Six Sigma is a set of methodologies and tools used to improve business processes by reducing defects and errors, minimizing variation, and increasing quality and efficiency. The goal of Six Sigma is to enhance overall efficiency, reduce errors, and enhance customer satisfaction. It employs a data-driven approach, emphasizing the importance of precise measurement and analysis to identify and eliminate defects or variations in processes.CTA:
CTA:The term “six sigma” itself refers to the statistical goal of having processes that operate with minimal defects, allowing only about 3.4 defects per million opportunities. By following the Six Sigma methodology, organizations aim to achieve higher quality, streamline operations, and ultimately deliver better products or services to customers.CTA:
CTA:Achieving improved processes is carried out through a structured approach known as DMAIC, which stands for Define, Measure, Analyze, Improve, and Control. This method identifies and eliminates sources of variation, reducing defects.CTA:
CTA:Six Sigma is considered a methodical and data-focused strategy extensively applied in project management for process enhancement and defect reduction. It offers a systematic framework to pinpoint and remove variations that might affect project outcomes.CTA:
CTA:The term “Six Sigma” has its roots in the Greek symbol “sigma” (σ), a statistical measure indicating how much a process deviates from its mean or target. The name “Six Sigma” is derived from the statistical bell curve, where one Sigma represents a single standard deviation from the mean. If a process has six Sigmas, three above and three below the mean, it is considered to have an “extremely low” defect rate.CTA:
CTA:The visual representation of the normal distribution graph illustrates the statistical principles of the Six Sigma model. A higher standard deviation indicates a broader range of encountered values. Therefore, processes aiming for Six Sigma have a mean at least 6σ away from the closest specification limit.CTA:
What Is Lean and Six Sigma Methodology?
CTA:Lean and Six Sigma are methodologies aimed at improving business processes. Lean focuses on waste reduction, maximizing efficiency, and streamlining operations to deliver value to customers with fewer resources, whereas Six Sigma emphasizes variation, errors, and process reductionCTA:
CTA:When combined, Lean and Six Sigma create a powerful approach known as Lean Six Sigma. This integrated methodology leverages the strengths of both Lean and Six Sigma to optimize processes, minimize waste, and enhance overall quality and efficiency. It provides a comprehensive framework for organizations to achieve operational excellence and deliver higher-quality products or services.CTA:
What Are The 5 Phases of Six Sigma Methodology?
CTA:The Six Sigma Methodology consists of five key phases, known as DMAIC: Define, Measure, Analyze, Improve, and Control. These stages provide a structured and data-driven approach to process improvement, guiding organizations through a systematic journey to enhance efficiency, reduce defects, and achieve better quality outcomes.CTA:
1. Define
CTA:The “Define” phase in Six Sigma methodology is the initial step where the project team clarifies and outlines the project’s purpose, goals, and deliverables. This phase involves defining the problem or opportunity that requires improvement and establishing clear parameters for success. It sets the foundation for the entire project by identifying the scope, stakeholders, and the overall project plan.CTA:
CTA:In petrochemical, petroleum, and energy industries, examples of the “Define” phase may include:CTA:
- Improving Refinery Efficiency
CTA:Defining a project to enhance the efficiency of refinery processes, specifying the scope, and setting measurable goals for increased output or reduced energy consumption.CTA:
- Reducing Equipment Downtime
CTA:Identifying and defining a project aimed at minimizing downtime for critical equipment, establishing parameters for acceptable performance, and setting targets for improved reliability.CTA:
- Optimizing Supply Chain Processes
CTA:Defining a project to streamline supply chain operations, specifying the key areas for improvement, and setting goals for reducing lead times or improving inventory management.CTA:
- Enhancing Safety Protocols
CTA:Defining a project focused on improving safety measures, specifying the safety concerns to be addressed, and setting measurable goals for reducing incidents and ensuring compliance with industry standards.CTA:
2. Measure
CTA:The “Measure” phase in Six Sigma methodology is the second stage where the project team collects and analyzes relevant data to quantify the current state of the process or problem identified in the “Define” phase. It involves developing a measurement plan, defining key performance indicators (KPIs), and gathering accurate and reliable data to assess the baseline performance.CTA:
CTA:In petrochemical, petroleum, and energy industries, examples of the “Measure” phase may include:CTA:
- Process Efficiency Measurement
CTA:Conducting measurements to quantify the efficiency of a specific refining process, capturing data on throughput, energy consumption, and other relevant metrics.CTA:
- Equipment Performance Metrics
CTA:Measuring the performance of critical equipment, such as turbines or pumps, by collecting data on factors like reliability, downtime, and maintenance needs.CTA:
- Environmental Impact Assessment
CTA:Gathering data to measure the environmental impact of certain operations, including emissions, waste generation, and adherence to environmental regulations.CTA:
- Supply Chain Performance Metrics
CTA:Evaluating the performance of the supply chain by measuring key indicators such as lead times, inventory levels, and on-time delivery rates.CTA:
3. Analyze
CTA:The “Analyze” phase in Six Sigma methodology is the third stage where the project team scrutinizes and interprets the collected data to identify patterns, root causes, and potential sources of variation within the process. It involves applying statistical tools and methods to gain a deeper understanding of the factors influencing the problem or process.CTA:
CTA:In petrochemical, petroleum, and energy industries, examples of the “Analyze” phase may include:CTA:
- Root Cause Analysis for Equipment Failures
CTA:Using statistical analysis to identify the root causes of equipment failures, such as examining historical maintenance data, operational parameters, and failure modes.CTA:
- Variation Analysis in Production Processes
CTA:Investigating variations in the production processes to determine factors affecting product quality, efficiency, or safety by analyzing data on process parameters.CTA:
- Energy Consumption Patterns Analysis
CTA:Analyzing energy consumption data to identify inefficiencies and areas for improvement in energy-intensive operations, such as refining or manufacturing.CTA:
- Emission Reduction Strategies
CTA:Applying statistical methods to analyze emissions data and identify strategies for reducing environmental impact, meeting regulatory requirements, and enhancing sustainability practices.CTA:
4. Improve
CTA:The “Improve” phase in Six Sigma methodology is the fourth stage where the project team devises and implements solutions to address the identified issues and improve the process. It involves developing and testing potential solutions, selecting the most effective ones, and implementing changes to achieve the desired improvements.CTA:
CTA:In petrochemical, petroleum, and energy industries, examples of the “Improve” phase may include:CTA:
- Process Optimization for Energy Efficiency
CTA:Implementing changes to optimize production processes, reduce energy consumption, and enhance overall efficiency in refinery or manufacturing operations.CTA:
- Enhancement of Safety Protocols
CTA:Introducing and implementing improved safety protocols and procedures based on the analysis of incident data to minimize risks and enhance workplace safety.CTA:
- Upgrading Equipment for Reliability
CTA:Implementing improvements in equipment design or maintenance practices to enhance reliability and reduce the frequency of unplanned downtime.CTA:
- Reducing Environmental Impact
CTA:Introducing changes in processes or technologies to minimize environmental impact, such as reducing emissions, waste generation, or water usage in compliance with sustainability goals and regulationsCTA:
5. Control
CTA:The “Control” phase in Six Sigma methodology is the fifth and final stage where the team implements measures to ensure the sustained success of the improvements made during the project. It involves establishing controls and monitoring systems to track the performance of the optimized process over time. The goal is to prevent a return to the previous state of inefficiency or defects.CTA:
CTA:In petrochemical, petroleum, and energy industries, examples of the “Control” phase may include:CTA:
- Continuous Monitoring of Key Metrics
CTA:Implementing a system to continuously monitor critical metrics, such as production output, energy consumption, or emissions, to ensure they remain within acceptable limits.CTA:
- Documented Standard Operating Procedures (SOPs)
CTA:Developing and enforcing standardized operating procedures for various processes to maintain consistency and prevent deviations that could lead to defects or safety issues.CTA:
- Training Programs for Sustainability
CTA:Conducting ongoing training programs for employees to ensure they are familiar with and adhere to the optimized processes, safety protocols, and environmental practices.CTA:
- Regular Audits and Inspections
CTA:Establishing a schedule for regular audits and inspections to assess compliance with established controls, identify any deviations, and take corrective actions as needed to sustain improvements.CTA:
CTA:In summary, the six sigma methodology serves as a robust approach for enhancing processes and minimizing defects. The structured method, DMAIC, includes steps like Define, Measure, Analyze, Improve, and Control, offering organizations a systematic and data-driven framework.CTA:
CTA:By adhering to statistical principles and targeting an “extremely low” defect rate, Six Sigma ensures a disciplined strategy to identify and eliminate variations, ultimately improving overall project performance. Its success lies in a commitment to ongoing improvement, making it a valuable tool for organizations striving for operational excellence and superior quality.CTA:
CTA:Embarking on Six Sigma methodology not only elevates your understanding of process improvement but also opens doors to numerous opportunities for professional growth. To further enhance your skills and ensure a comprehensive grasp of Six Sigma and related principles, consider enrolling in PetroSync‘s Certified Reliability Engineer (CRE) training.CTA:
CTA:Our CRE training program incorporates Six Sigma methodology as part of its learning approach, providing you with a well-rounded and practical understanding of reliability engineering. By taking this step, you position yourself to not only meet the challenges of today’s competitive landscape but also lead your organization towards excellence in reliability and performance.CTA:
CTA:Credit: FreepikCTA:
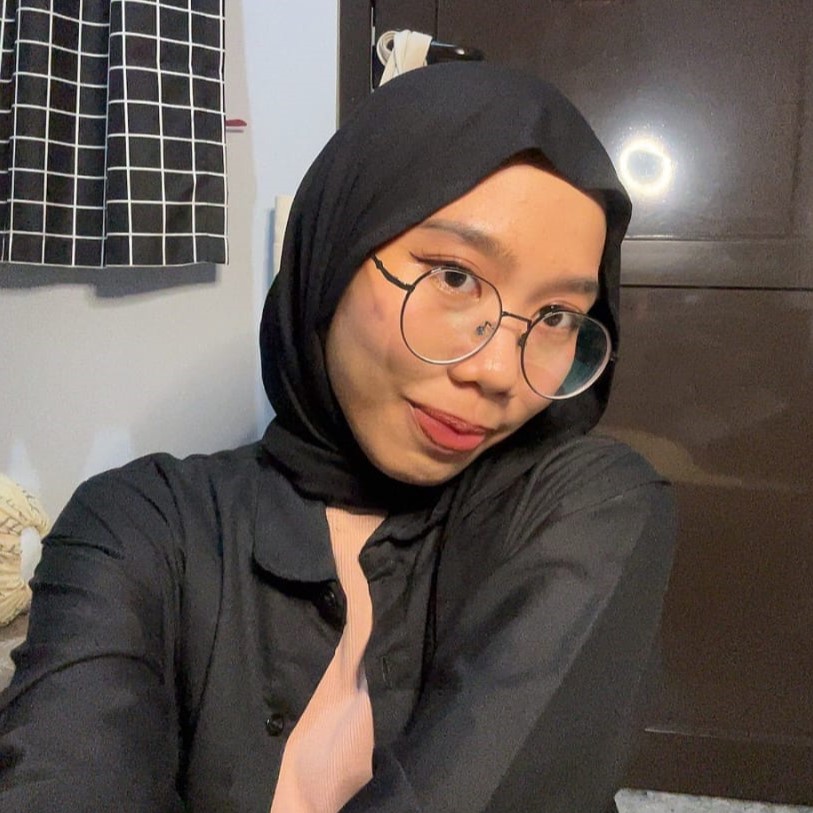
SEO specialist by day, fact-checker by night. An avid reader and content writer dedicated to delivering accurate and engaging articles through research and credible sources.