In high risk industries where safety is crucial, leak testing is an essential task to ensure that systems and equipment function without any leaks that can lead to further damage. This article will cover the basics of leak testing, why it is important for safety, and the different methods used to perform leak tests.
What Is Leak Testing?
Leak testing is a procedure that inspectors use to determine whether an object or system is functioning within a specific leak limit, checking for any leaks or holes in a system or component that could allow fluids or gasses to escape. It involves pressurizing the system or component with a gas or liquid and then monitoring for any decrease in pressure, which could indicate a leak.
There are various methods of leak testing, including pressure decay, bubble testing, and helium leak detection, each with its own advantages depending on the specific application. During leak testing procedures, inspectors will examine for various types of defects such as cracks, holes, inadequate seals, and other flaws or imperfections that could result in the escape of gas or liquid from an object or system.
What Are Some Leak Testing Methods?
There are several leak testing methods commonly used across industries:
1. Pressure Decay Testing
This method involves pressurizing the test object with gas and then measuring any decrease in pressure over a specific time period. A significant drop in pressure indicates the presence of a leak.
2. Hard Vacuum Leak Test
In this method, the test object is placed in a vacuum chamber, and any leaks are detected by observing changes in the vacuum level. This test is suitable for detecting small leaks in sealed components.
3. Bubble Test
The bubble test involves applying a liquid solution or mixture, usually soapy water, to the surface of the test object and then observing for the formation of bubbles. Bubbles indicate the presence of a leak, making this method effective for identifying leaks in pressurized systems.
4. Vacuum Decay
Similar to pressure decay testing, vacuum decay involves subjecting the test object to a vacuum and then monitoring any increase in pressure over time, which can indicate the presence of a leak.
5. Vacuum Testing
This method involves creating a vacuum inside or around the test object and then observing for any changes in pressure or vacuum level, which can indicate the presence of a leak.
6. Absolute Pressure Method
In this method, the test object is pressurized to a known absolute pressure, and any decrease in pressure over time is measured to detect leaks.
7. Biological Leak Detection
This method utilizes bacteria or other microorganisms that react to the presence of specific gasses emitted from leaks, providing a sensitive and accurate means of leak detection.
8. Dye Penetrant Method
This method involves applying a colored dye to the surface of the test object, which penetrates into any surface defects or cracks. After a specified time, excess dye is removed, and any leaks are revealed by the presence of colored dye.
9. Helium Leak Detection
Helium is used as a tracer gas in this method, where the test object is pressurized with helium, and a specialized detector is used to identify helium escaping from any leaks. This method is highly sensitive and suitable for detecting very small leaks in a wide range of materials and components.
What Are Some Leak Testing Considerations?
When conducting leak test, there are several important considerations to keep in mind:
1. Acceptable Leak Rate
Understand the acceptable level of leakage for the object or system being tested. Different industries have guidelines specifying acceptable leak rates for various products and substances, guiding maintenance decisions.
2. Manufacturing Considerations
Consider the original purpose and design of the object or system. Manufacturers may have designed it to either retain or allow substances to pass through, impacting the approach to leak testing.
3. Material Considerations
The material of the object affects how it responds to pressure and potential leaks. Factors like brittleness or malleability influence how the object changes shape under pressure, affecting the accuracy of leak tests.
4. Medium Considerations
Consider the substance the object holds, as different molecules have varying sizes. Understand the size of defects that could allow substances to escape and the pressure ranges that could affect the object’s integrity without damaging it. These factors help ensure accurate and safe leak testing procedures.
What Are The International Standards for Leak Tests?
1. ASTM E1003
ASTM E1003 outlines the standard test method for hydrostatic leak testing. This method involves pressurizing a system or component with a liquid, typically water, to a specified pressure level and then monitoring for any decrease in pressure over a set period. The test evaluates the integrity of the system by assessing whether it can maintain pressure without any significant leaks.
2. ISO 20485
ISO 20485 provides guidelines for leak testing of components used in gas cylinders. This standard specifies various testing methods, such as pressure decay testing, immersion testing, and bubble testing, to ensure the safety and reliability of gas cylinders. It also includes requirements for test equipment, procedures, and acceptance criteria for detecting and quantifying leaks in gas cylinder components.
3. ASME Section V
ASME Section V outlines the non-destructive examination (NDE) methods, including leak testing, used to assess the integrity of materials and components. This section of the ASME Boiler and Pressure Vessel Code specifies procedures for leak testing using various techniques, such as pressure testing, vacuum testing, and tracer gas testing. It provides requirements for equipment calibration, test procedures, and acceptance criteria to ensure the accuracy and reliability of leak testing results.
4. EN 13185
EN 13185 is the European standard for leak testing of refrigerating systems and heat pumps. This standard specifies the methods and procedures for leak testing refrigerating systems and heat pumps using various techniques, such as pressure testing, vacuum testing, and halide torch testing. It includes requirements for test equipment, test procedures, and acceptance criteria to ensure the safety and efficiency of refrigerating systems and heat pumps.
5. API 570
API 570 standard is the American Petroleum Institute (API) standard for inspection, repair, alteration, and rerating of in-service piping systems. While not specifically focused on leak testing, API 570 includes guidelines for evaluating the integrity of piping systems, which may involve leak testing as part of the inspection process. It provides requirements for assessing the condition of piping systems and determining the need for repairs or maintenance to prevent leaks and ensure safe operation.
In conclusion, leak testing plays a crucial role in ensuring the safety, reliability, and performance of various systems and components across industries. By detecting and addressing leaks promptly, you can prevent potential hazards, minimize downtime, and prolong the lifespan of equipment.
Adhering to international standards and employing appropriate testing methods is essential for accurate and effective leak detection. Remember to consider factors such as acceptable leak rates, manufacturing materials, and testing procedures to conduct thorough and reliable leak tests. By prioritizing leak testing and implementing best practices, you can maintain the integrity of systems and promote a safe working environment for all.
Credit Header Image: Vecteezy
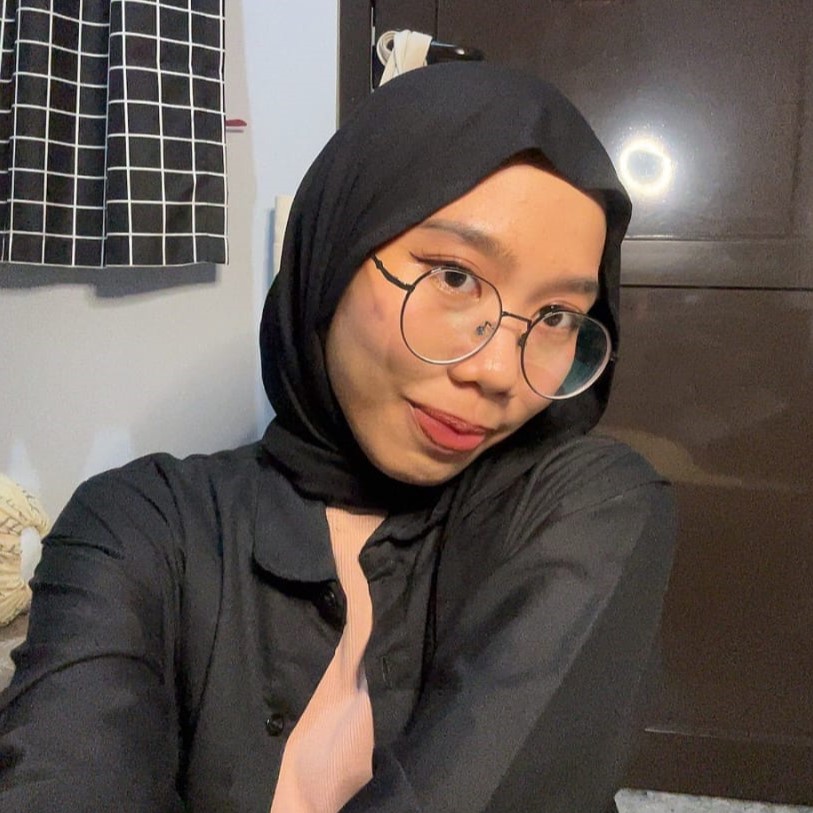
SEO specialist by day, fact-checker by night. An avid reader and content writer dedicated to delivering accurate and engaging articles through research and credible sources.