In the realm of manufacturing and material engineering, heat treatment is critical for increasing the strength and durability of many materials. Whether you’re working with metals, alloys, or other materials, heat treatment is used to change the physical and mechanical qualities to fulfill specific performance needs.
This makes heat-treating critical in industries like automotive, aerospace, and construction, where material performance directly affects product quality and safety. But what exactly is heat-treating, and how does it alter material properties?
In this article, we’ll go over the notion of heat-treating, including its process, methods, and types, so you can grasp how this strategy is used to improve material strength and durability.
What Is Heat Treatment?
Heat treatment is a regulated procedure for changing the characteristics of materials, particularly metals and alloys. Manufacturers can change the hardness, strength, flexibility, and other mechanical qualities of materials by heating and cooling them under certain conditions. Heat treatment aims to improve the material’s resistance to wear, corrosion, and fatigue.
Making it more suited for specific applications. The phrase heat treatment refers to any technique that involves heating and cooling materials to obtain a certain set of qualities. This can be accomplished via a variety of processes, including quenching, tempering, annealing, and normalizing, each with a specific purpose in increasing material performance.
Heat-treating is quite important in industrial settings. In the automotive sector, post-weld heat-treating is often employed to reduce internal stresses and prevent cracking. This ensures that the building will be durable and functional. heat-treating is also required for parts that are exposed to extreme conditions, such as gears and shafts, where toughness and resistance to deformation are crucial.
What Is The Heat Treatment Process?
Heat treatment is a sequence of precisely controlled processes in which metals are heated to specified temperatures and then cooled in a specific manner to adjust their physical and mechanical properties while retaining their original shape. This process is critical for improving the strength, hardness, and longevity of metal parts, hence increasing their resistance to wear and deterioration.
Heat-treated materials are commonly used in the oil and gas industry to withstand extremely high temperatures and pressures, ensuring the longevity and safety of equipment in severe environments. Heating, soaking (maintaining a high temperature), and cooling are all stages of the process that are meticulously managed to get the appropriate material properties.
Metal can be softened or hardened through heat treatment, depending on the method used.
What Are The 4 Methods Of Heat Treatment?
There are four primary methods of heat treatment, each serving different purposes depending on the desired material properties:
1. Annealing
Annealing is the process of heating a metal to a specific temperature and then slowly cooling it, typically in a furnace. This technique softens the metal, enhancing ductility and making it easier to work with. Annealing also helps relieve internal stresses and improve the material’s machinability and conductivity.
2. Quenching
Quenching involves heating the metal and then rapidly cooling it, usually in water, oil, or air. This process increases the hardness and strength of the metal but can make it more brittle. Quenching is frequently used for components that require high wear resistance, such as tools or heavy machinery parts in the energy sector.
3. Tempering
Tempering is done after quenching to reduce the metal’s brittleness while keeping some of the hardness obtained during the quenching process. This entails warming the quenched metal to a lower temperature and allowing it to cool gradually. The end product is a material with an excellent blend of strength, hardness, and toughness, making it ideal for critical applications such as pipelines and pressure vessels.
4. Normalizing
Normalizing entails heating the metal to temperatures over its critical range and allowing it to cool in the air. This process refines the metal’s grain structure, increasing mechanical properties such as strength and hardness. Normalizing is commonly used for steel components in the oil and gas industry to maintain homogeneity and eradicate the impacts of earlier heat treatments.
What Is The Basic Principle Of Heat Treatment?
The basic goal of heat treatment is to control a material’s temperature and cooling rate in order to affect its microstructure and, therefore, mechanical properties. Heat treatment alters the crystalline structure of a metal, increasing its hardness, strength, and ductility.
The process typically involves three key steps:
1. Heating:
The metal is heated to a precise temperature where its microstructure begins to change.
2. Soaking:
The metal is held at this temperature for a set period to allow the heat to penetrate throughout the material.
3. Cooling:
The metal is cooled at a controlled rate, either slowly or rapidly, depending on the desired outcome.
This approach is very important in the oil and gas industry because it allows components to operate consistently in harsh environments, reducing the risk of failure and extending the lifespan of vital equipment. Heat treatment is a crucial part of various industrial processes, ensuring that metals meet strict requirements related to safety and durability.
How Does Heat Treatment Work?
Heat treatment alters the atomic structure of a substance, typically a metal. When a metal is heated, its atomic bonds become more flexible, allowing atoms to shift positions. The way the metal is cooled after formation determines its final structure and qualities. For example, rapid cooling (quenching) holds the atoms in a hard but brittle form.
Whereas slow cooling allows the atoms to migrate into a more stable and less brittle configuration. Post weld heat treatment reduces welding residual stress, enhancing durability and performance of the welded product.
Heat treatment customizes material properties by adjusting temperature, duration, and cooling rate for specific applications. This process is crucial for developing components that must perform reliably in stressful or hostile environments.
What Are The Types of Heat Treatment?
Heat treatment processes differ according to the material and purpose. Some of the more frequent varieties include:
1. Carburizing:
A process of adding carbon to the surface of low-carbon steels to increase hardness while maintaining a strong interior.
2. Case Hardening:
Heats the material and inserts carbon or nitrogen into its surface, forming a hard outer layer and a tough inner core.
3. Quenching and Tempering:
To change the hardness and strength of steel, heat it, then quickly cool and reheat it.
4. Solution Heat Treatment:
This technique, which is commonly used for aluminum and other nonferrous metals, includes heating the material to dissolve alloying components before rapidly cooling it.
Each method of heat treatment is chosen based on the required material qualities and the end usage of the product. Understanding these types and how they function is critical for improving material strength and durability in manufacturing.
Join PetroSync and Enhance Your Heat Treatment Skills
If you want to learn more about heat treatment and how it may improve material qualities in a variety of industries, join PetroSync. PetroSync offers professional training and consulting for industries that require advanced knowledge in materials engineering and heat-treating techniques. By joining PetroSync, you can gain practical insights into post weld.
Learn about the different methods and types of heat-treating, and understand how to apply these techniques in real-world scenarios. PetroSync offers courses to help engineers, technicians, and QC professionals advance careers and understand heat treatment better.
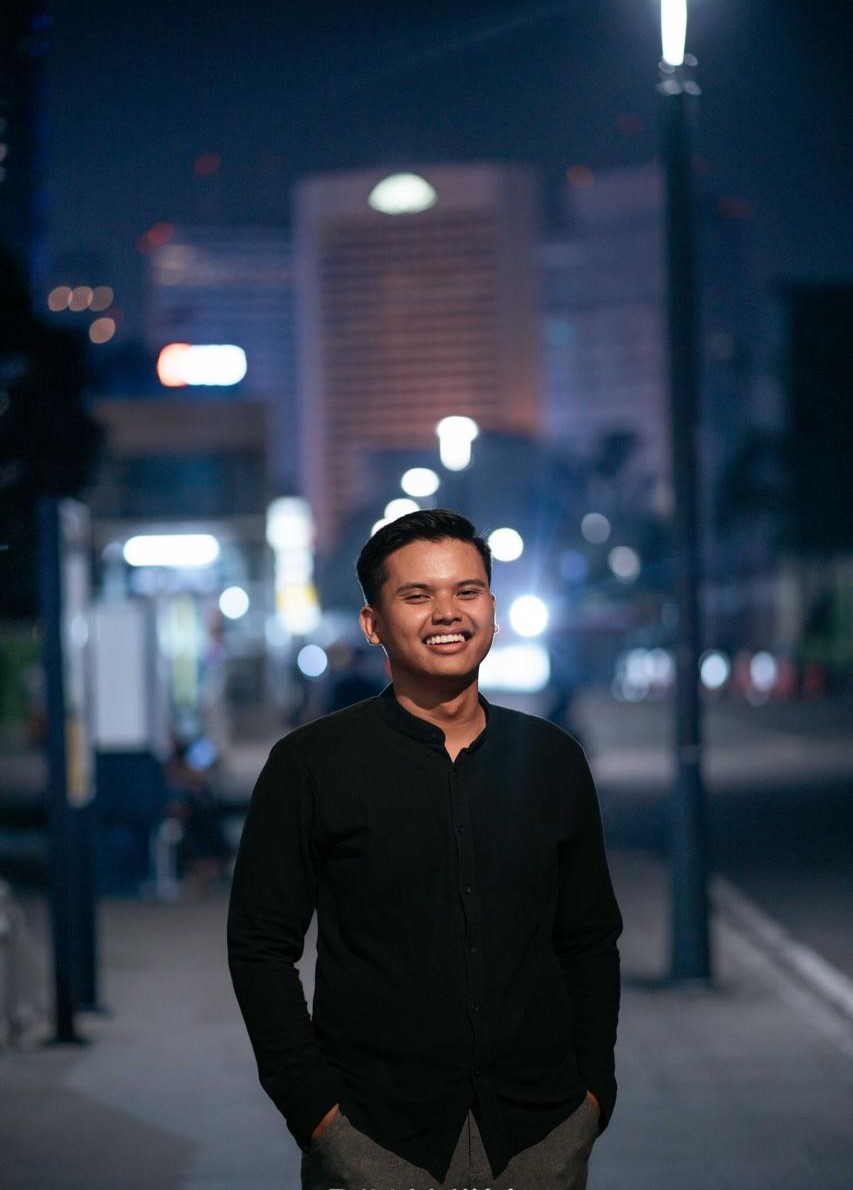
Results-oriented and thorough SEO specialist with extensive experience in conducting keyword research, developing and implementing digital website promotion strategies and plans, managing campaigns to develop company websites in the digital world, excellent knowledge of marketing techniques and principles, and attentive strong attention to detail.