Heat exchanger are critical components in many industries, increasing efficiency and thermal performance. By transporting heat between fluids, they aid in the optimization of heating, cooling, and even energy recovery operations. This makes them essential in industries including oil and gas, petrochemicals, HVAC, and power generation.
In today’s world, where energy conservation and efficiency are critical, the role of heat exchangers cannot be overstated. They not only reduce energy consumption but also increase operational efficiency by maintaining the desired temperature levels in systems. Whether you are an engineer or an industry professional, understanding the heat exchanger meaning and principles is essential for improving your thermal systems.
What Is A Heat Exchanger?
A heat exchanger is a device that transfers heat between two or more fluids with different temperatures. The major function is to transfer heat energy from one medium to another without mixing them, allowing for precise thermal control in a variety of systems. A heat exchanger’s definition varies slightly depending on its type and use.
But they all serve the same basic purpose to improve heat flow and system efficiency. Heat exchangers in industrial applications come in a variety of shapes and sizes to meet the system’s specific requirements. Common types include shell and tube heat exchangers, plate heat exchanger, and air-cooled heat exchanger.
These devices are required for tasks such as cooling engines, heating fluids, and recovering waste heat from exhaust.
What Is The Function of Heat Exchangers?
The primary function of heat exchanger is to efficiently transfer heat between two substances, such as liquids or gases, without allowing them to mix directly. They play a crucial role in various applications to achieve heating or cooling effects. In heating processes, a heat exchanger helps raise the temperature of a substance by transferring heat from a warmer fluid or gas to it.
Conversely, in cooling processes, the heat exchanger facilitates the removal of excess heat from a substance by transferring it to a cooler fluid or gas. The key components involved in this process are the two mediums (fluids or gases) with different temperatures and the surface area provided.
The hotter medium releases heat as it passes through the heat exchanger, which is then absorbed by the colder medium, resulting in temperature changes for both substances. This efficient heat transfer mechanism is fundamental in applications ranging from household heating systems and air conditioners to industrial processes like power generation, chemical manufacturing, and refrigeration.
What Is the Principle of a Heat Exchanger?
Any heat exchanger’s operation is based on a fundamental thermodynamic concept: heat travels reliably from higher to lower temperatures. When a conductive barrier separates a hot fluid from a cooler one, heat naturally moves from the warmer fluid to the cooler one.
This controlled heat transfer enables heat exchangers to manage temperature in industrial operations without bringing the two fluids into direct contact. Heat exchangers increase system energy efficiency by leveraging the natural transfer of heat, ensuring that operations run smoothly while minimizing energy loss.
This idea is employed in a variety of heat exchanger designs, including shell-and-tube, plate, and air-cooled types, all of which are tuned to fit specific purposes. Whether heating a cold fluid or cooling a hot one, the goal is the same: achieve thermal balance in the most energy-efficient method feasible.
What Are The Components of Heat Exchangers?
Heat exchangers are sophisticated machines comprised of numerous critical components that all contribute to their efficiency. These components work together to provide efficient heat transfer while assuring the system’s lifetime and safety. The primary components of heat exchangers are as follows:
1. Tubes/Channels
The tubes or channels are the conduits via which fluids move. They are the central components of most heat exchangers, with one fluid passing through the tubes and the other flowing around them. The tubes’ material and design have a considerable impact on heat transmission efficiency.
2. Shell/Casing
The shell or casing houses the tubes or channels. This component gives structural integrity to the heat exchanger and guarantees that the fluids remain separate. The shell frequently includes apertures for fluids to enter and exit the system.
3. Tube Sheets/Header
The tube sheets, also known as headers, link the individual tubes to the rest of the heat exchanger. These components also help to direct the flow of fluids into the tubes, resulting in efficient heat transfer.
4. Fluid Inlets and Outlets/Nozzles
The inlets and outlets are critical for regulating the flow of fluids into and out of the heat exchanger. They are meant to reduce resistance and increase system efficiency.
5. Baffles/Fins
Baffles or fins are used to direct fluid flow through a heat exchanger. They improve the contact surface area between the fluids and the heat exchanger, hence enhancing heat transfer efficiency.
6. Pass Partitions/Dividers
Pass partitions or dividers are used to separate fluid flow into many passes within the heat exchanger. This increases the heat transfer surface area and enhances the system’s overall performance.
7. Heat Transfer Surface
The heat transfer surface is the substance used to transmit heat from one fluid to another. The greater the surface area, the better the heat transfer efficiency.
8. Turbulators
Turbulators are devices that induce turbulence in fluid flow. This helps mix the fluid, increasing the rate of heat transfer.
9. Insulation and Cladding
Insulation is applied to the heat exchanger to minimize heat loss to the environment. Cladding provides additional protection to the heat exchanger’s components, particularly in harsh environments.
10. Gaskets/Seals
Gaskets and seals ensure that fluids do not leak from the heat exchanger, maintaining efficiency and preventing contamination.
11. Flanges
Flanges are used to connect different sections of the heat exchanger. They create a secure, leak-proof connection.
12. By-pass valves
By directing fluid away from certain parts of the heat exchanger, bypass valves help to regulate fluid flow and prevent overheating.
13. Distributors and Collectors
Distributors and collectors are used to distribute the fluid evenly into the heat exchanger and collect the outgoing fluid.
14. Sight Glasses
Sight glasses allow operators to observe the fluid flow inside the heat exchanger, providing valuable insight into the system’s performance.
15. Drain Valves
Drain valves are essential for maintaining and cleaning heat exchangers. They allow the removal of fluids when maintenance is required.
16. Pressure and Temperature Sensors
These sensors help monitor the operating conditions of the heat exchanger, ensuring it is functioning within the correct parameters.
17. Bypass Dampers
Bypass dampers help control airflow and prevent unnecessary heat loss, ensuring optimal thermal performance.
Where Heat Exchangers Are Used For?
A range of sectors use heat exchangers, which play a critical role in improving efficiency and performance. Various applications utilize heat exchangers, including power generation in power plants, heating and air conditioning systems, refrigeration, manufacturing, food processing, chemical processing, and automotive radiators.
In fact, thousands of different places, from everyday appliances to large-scale industrial systems, use heat exchangers. Some common applications include:
1. Power Generation:
Heat exchangers are used in power plants to recover waste heat, hence increasing efficiency and lowering energy costs.
2. HVAC Systems:
Heat exchangers are essential components of air conditioning and heating systems, as they help regulate temperature and humidity.
3. Oil and Gas:
Heat exchangers are used in refineries to cool and heat fluids, hence enhancing system safety and performance.
4. Chemical Processing:
Heat exchangers are used in chemical plants to maintain stable reaction temperatures, resulting in optimal yields.
How Does a Heat Exchanger Work?
A heat exchanger has a basic working concept. Conduction is the transfer of heat from a hot to a cool fluid. The fluids are separated by a surface that allows heat to pass but inhibits mixing. As one fluid loses heat, the other absorbs it, either heating up or chilling down.
Heat is transferred by conduction through the exchanger materials that separate the media used.
A Shell and Tube Heat Exchanger distributes fluids through and over tubes, whereas an Air Cooled cools a liquid by circulating cool air through a fin-filled core.
A heat exchanger’s efficacy is determined by several parameters, including the surface area of the heat transfer material, the fluid flow rate.
And the temperature difference between the two fluids. The heat exchanger’s design, such as whether it is a Shell and Tube Heat Exchanger or a Plate Heat Exchanger, has a significant impact on its efficiency.
Which Heat Exchanger is Better?
Choosing the appropriate heat exchanger is dependent on the application’s individual requirements. A Shell and Tube Heat Exchanger performs best in high-pressure, high-temperature applications, whereas a Plate it works better in scenarios requiring space and efficiency. Plate heat exchangers are up to five times more efficient than shell-and-tube designs.
In many cases, you can recover more heat by replacing existing shell-and-tube models with compact heat exchangers. This makes Plate Heat Exchangers an excellent choice for industries or facilities that need to maximize heat recovery while minimizing space and energy consumption. Understanding the many types of heat exchangers, such as Shell and Tube Heat Exchangers.
Their characteristics is critical for picking the best one for your requirements. Shell and Tube Heat Exchanger Training may provide detailed knowledge of these systems, allowing professionals to make informed judgments.
Join PetroSync Training: Elevate Your Skills Today!
To deepen your understanding of heat exchangers, especially the widely used shell and tube heat exchangers design, consider enrolling in a specialized training program. PetroSync offers comprehensive ASME/TEMA-certified courses on shell and tube heat exchangers, covering aspects of design, maintenance, and operational best practices.
By enhancing your knowledge in this field, you can contribute to improved efficiency, safety, and reliability in heat exchange systems. Invest in your professional development and explore the world of heat exchangers through practical, industry-focused shell and tube heat exchangers training with PetroSync!
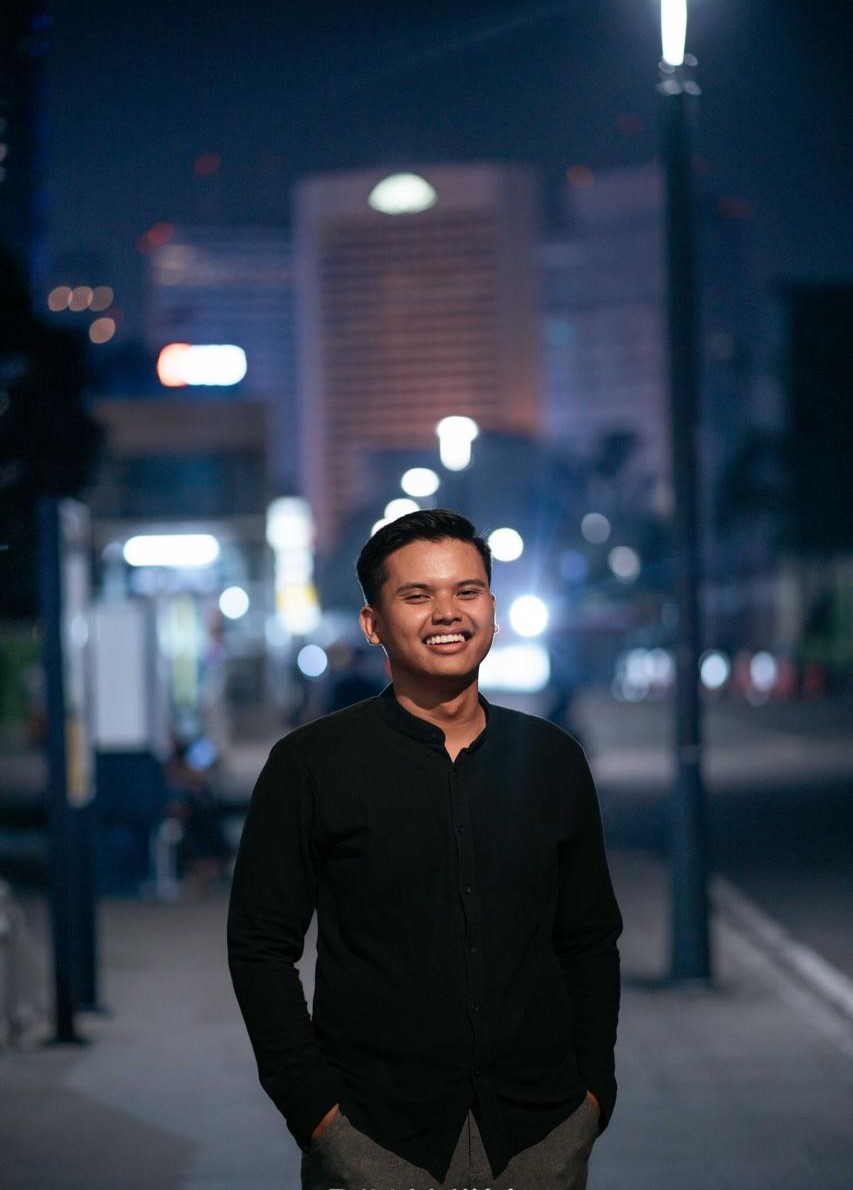
Results-oriented and thorough SEO specialist with extensive experience in conducting keyword research, developing and implementing digital website promotion strategies and plans, managing campaigns to develop company websites in the digital world, excellent knowledge of marketing techniques and principles, and attentive strong attention to detail.