In the complex world of oil and gas exploration, where details matter, casing design plays a crucial role in optimizing well operations. This article delves into the various aspects of casing design, explaining why it is vital for ensuring efficient well performance.
What Is Casing Design?
Casing design in the context of oil and gas involves the careful planning and construction of a protective structure, known as casing, around a wellbore. This process includes the selection of setting depths, casing sizes, and grades of steel that will enable the safe drilling and well completion of a well to the desired producing configuration.
The casing serves as a robust outer layer, shielding the well and preventing unwanted substances from entering or leaking out. The primary goal of casing design is to ensure the integrity and stability of the well, addressing factors such as depth, pressure, and geological conditions. Proper casing design is essential for preventing accidents, maintaining well control, and safeguarding the environment.
What Are Casing Design Objectives?
The objectives of casing design in the context of oil and gas are
1. Ensure Mechanical Integrity
The primary goal is to safeguard the well’s mechanical integrity. This involves creating a design foundation that considers all expected loads the well may face throughout its lifespan. By doing so, we aim to prevent any structural issues that could compromise the well’s stability.
2. Minimize Well Costs
Designing the casing strings with cost efficiency in mind is essential. The objective is to minimize overall well costs throughout its operational life. This includes selecting materials and configurations that balance durability and cost-effectiveness.
3. Provide Clear Documentation
It’s crucial to offer comprehensive documentation of the design basis to the personnel working at the well site. This documentation serves as a guide, helping operational staff understand the design parameters. By providing clear information, we aim to prevent the application of loads that were not initially considered in the original design, avoiding any risks associated with exceeding the design limits
Although the goal is to construct wells reliably at a low cost, failures can still happen. Most recorded failures occur when the pipe is subjected to loads it wasn’t designed for, known as “off-design” failures.
Failures that occur under the intended design conditions, referred to as “on-design” failures, are infrequent. This suggests that casing design practices are cautious. A significant number of failures happen at the connections. This suggests that either the on-site assembly practices need to be revised or the design basis for the connections needs to align with the design basis for the pipe body.
What Are Casing Design Methods?
Casing design involves careful planning to create a protective structure around a wellbore, ensuring stability and safety. The methods used in casing design are systematic approaches to determine the right materials, dimensions, and configurations for the casing strings.
1. Preliminary Design Method
The preliminary design phase in casing design is a crucial step where significant cost-saving opportunities can be identified. This phase involves several key tasks
Data Gathering and Interpretation
Collecting essential information about the well site and understanding geological data. This helps in making informed decisions throughout the casing design process.
Determination of Casing Shoe Depths and Number of Strings
Figuring out how deep the casing shoe should be set and deciding on the number of casing strings needed. This is vital for providing stability and support to the well.
Selection of Hole and Casing Sizes
Choosing the appropriate sizes for the wellbore and casing. This decision is based on factors like well conditions and the type of materials that will be encountered during drilling.
Mud-Weight Design
Designing the mud weight, or the density of the drilling fluid. This is crucial for controlling pressure, stabilizing the well, and preventing issues like wellbore collapse.
Directional Design
Planning for directional drilling if needed. This involves determining the path the well will take to reach its target. Directional design is essential for accessing specific reservoirs or avoiding obstacles underground.
During the Preliminary Design phase, careful consideration of these factors ensures that the casing design sets a solid foundation for the overall well construction. By making informed decisions in this early stage, engineers can optimize costs and contribute to the success and safety of the entire drilling process.
2. Detailed Design Method
The Preliminary Design phase in casing design is where significant cost-saving opportunities can be found. This phase involves crucial tasks, and here are the key steps
Data Gathering and Interpretation
Collecting important information about the well site and understanding geological data. This helps in making well-informed decisions during the casing design process.
Determining Casing Shoe Depths and Number of Strings
Figuring out how deep the casing shoe should be set and deciding on the number of casing strings needed. This is vital for providing stability and support to the well.
Selecting Hole and Casing Sizes
Choosing the right sizes for the wellbore and casing based on factors like well conditions and the materials encountered during drilling.
Mud-Weight Design
Designing the mud weight, or the density of the drilling fluid. This is crucial for controlling pressure, stabilizing the well, and preventing issues like wellbore collapse.
Directional Design
Planning for directional drilling if needed. This involves determining the path the well will take to reach its target. Directional design is essential for accessing specific reservoirs or avoiding obstacles underground.
Additionally, in the detailed design phase, engineers choose the right weights and grades for each casing string. The process involves comparing pipe ratings with design loads and applying minimum safety standards (design factors). A cost-effective design meets all criteria with the least expensive available pipe, contributing to overall cost efficiency.
What Is the Required Information in Creating Casing Design?
Information Category | Required Information |
Formation Properties |
|
Directional Data |
|
Minimum Diameter Requirements |
|
Production Data |
|
Other |
|
This checklist provides you with essential information during both the preliminary and detailed design phases, ensuring a comprehensive and well-informed approach to casing design.
In the oil and gas industry, casing design is a critical aspect of well construction, ensuring the stability, safety, and efficiency of drilling operations. By carefully planning and implementing protective casing structures, you can mitigate risks associated with formation pressures, temperature variations, and other geological challenges.
If you’re interested in delving deeper into casing design and enhancing your knowledge in applied drilling and well engineering, enroll in specialized training by PetroSync. The Applied Drilling and Well Engineering training provides comprehensive insights into various aspects of well construction, including casing design.
You can gain practical knowledge and skills that are crucial for professionals in the oil and gas industry. To learn more about this applied drilling and well engineering training and related subjects, visit PetroSync’s website or contact them directly. Invest in your professional development and stay abreast of industry best practices in drilling and well engineering.
Credit header image: Freepik.com
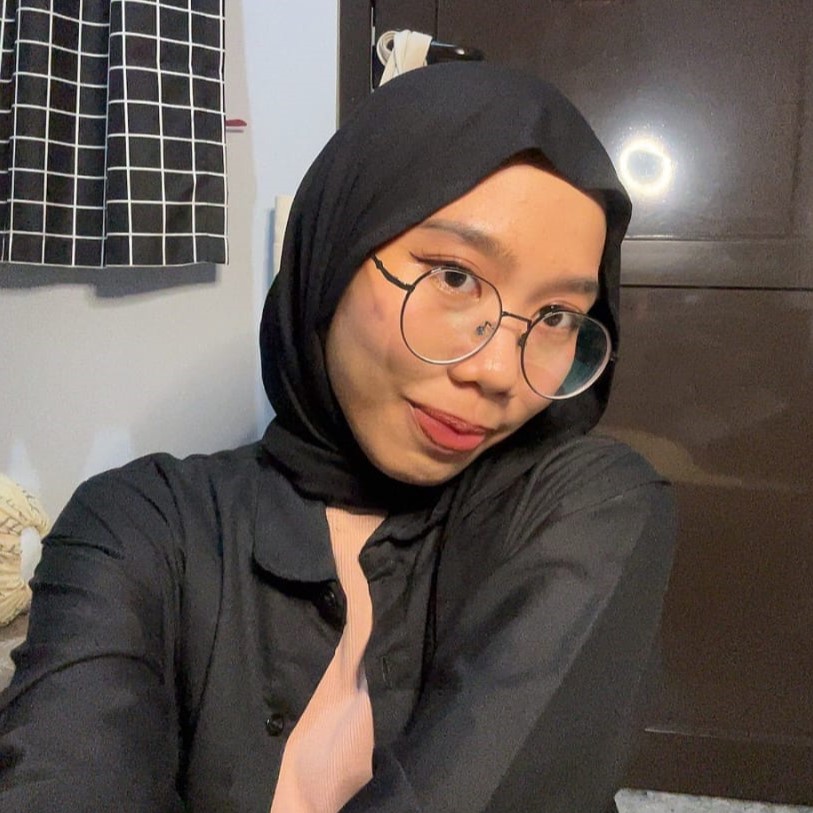
SEO specialist by day, fact-checker by night. An avid reader and content writer dedicated to delivering accurate and engaging articles through research and credible sources.