Understanding the common types of storage tanks is essential for making informed decisions regarding storage solutions. In this exploration, we delve into the characteristics and applications of prevalent storage tank types, each tailored to distinct industry needs and contributing to the safe and reliable storage of valuable materials.
What Is The Storage Tank?
A storage tank is a large container designed to hold and store liquids, compressed gases, or mediums for the short- or long-term storage of heat or cold. These tanks are utilized in various industries, such as agriculture, manufacturing, and energy. They come in different shapes and sizes, storing water, chemicals, oil, gas, or other substances.
Particularly crucial in industries like petrochemicals, a storage tank functions as a sizable vessel for storing oil, gas, and other petrochemical products. Overall, storage tanks are pivotal in providing a reliable means to store and manage substantial quantities of liquids or gases for later use or distribution.
What Are The Common Types of Storage Tanks?
Storage tanks play a crucial role in various industries by providing a secure and efficient means of storing liquids, gases, and other substances. The selection of an appropriate storage tank type is vital to meet the specific requirements of different applications.
1. Fixed-Roof Tanks
Fixed-roof tanks are a cost-effective and commonly used design for storing liquids. Typically, they consist of a cylindrical steel shell with a cone- or dome-shaped roof permanently attached. Modern versions are usually welded for liquid and vapor tightness. These tanks may have a Breather Valve for pressure-vacuum regulation, but older tanks might not be completely vapor-tight.
Application |
Advantages |
Liquid Storage | Cost-effective construction |
Petrochemicals | Simple design for basic storage needs |
General Industry | Low maintenance requirements |
Agriculture | Easy access for monitoring and maintenance |
2. External Floating Roof Tanks
External floating roof tanks feature a roof that floats on the liquid’s surface, rising and falling with the liquid level. The roof, composed of a deck, fittings, and a rim seal system, covers the liquid surface, minimizing evaporative losses. Floating roof decks come in configurations like pan, pontoon, or double deck, each emphasizing different characteristics.
Application |
Advantages |
Liquid Storage | Minimized evaporative losses |
Petrochemicals | Prevents exposure of liquid on tank walls |
Oil Industry | Versatile deck configurations for specific needs |
Environmental Compliance | Reduces standing storage loss |
3. Internal Floating Roof Tanks
Internal floating roof tanks have a roof that floats on the liquid surface or is supported by pontoons above the liquid. They can have a fixed roof with vertical columns or a self-supporting fixed roof without internal columns. Internal floating roofs rise and lower with the liquid level, providing a barrier between the stored liquid and the atmosphere.
Application |
Advantages |
Chemical Storage | Minimized vapor space and emissions |
Oil Refineries | Enhanced environmental and safety compliance |
Liquid Petrochemicals | Reduced withdrawal loss |
Storage of Volatile Substances | Vapor containment for safety |
4. Domed External Floating Roof Tanks
Domed external floating roof tanks combine a heavy-duty deck with a fixed roof on top of the shell. The fixed roof serves not only as a vapor barrier but also as a wind block. Self-supporting aluminum dome roofs are a popular type, fluidly ventilated similar to internal floating roof tanks.
Application |
Advantages |
Petrochemical Storage | Enhanced vapor containment |
Oil and Gas Industry | Wind resistance and stability |
Environmental Protection | Reduced vapor emissions |
Liquid Storage in Adverse Conditions | Self-supporting dome for added strength |
5. Horizontal Tanks
Horizontal tanks, often used in both above- and below-ground applications, have a horizontal orientation to ensure structural integrity. These steel tanks are equipped with pressure-vacuum vents, gauge hatches, and sampling wells. Cathodic protection may be applied to prevent corrosion in underground tanks.
Application |
Advantages |
Liquid Storage | Space-efficient design |
Agriculture | Easy integration into existing systems |
Petrochemical Industry | Cathodic protection for corrosion resistance |
General Industrial Storage | Structural integrity for diverse applications |
6. Variable Vapour Space Tanks
Variable vapour space tanks are equipped to handle temperature and barometric pressure variations. They may include lifter roof tanks or flexible diaphragm tanks, with wet or dry seal options. These tanks may be used separately or integrated with fixed-roof tank vapour spaces.
Application |
Advantages |
Chemical Processing | Efficient handling of temperature variations |
Petrochemical Storage | Prevents vapor losses due to temperature changes |
Industrial Applications | Flexibility in design for various needs |
Liquid Storage with Variable Conditions | Minimizes vapor loss during temperature fluctuations |
7. LNG (Liquefied Natural Gas) Tanks
LNG storage tanks are specialized containers designed to store liquefied natural gas at extremely low temperatures. These tanks have two cylinders—one for LNG and the other for insulating materials—to maintain the low temperature. Containment tanks are a common type, and LNG is preserved as a cryogen.
Application |
Advantages |
LNG Storage Facilities | Maintains LNG at ultra-low temperatures |
Energy Industry | Efficient preservation of liquefied natural gas |
Transportation (LNG Ships) | Ensures safe storage during transit |
Cryogenic Storage | Prevents LNG from vaporizing due to temperature changes |
What Are The Types of Storage Tanks based on Its Position?
Storage Tank Types |
Oil Type | Shape | Structure |
Capacity |
Aboveground Storage Tank | Crude oil, diesel, fuel oil, lubricating oil, edible oil, fire water, etc. | Vertical, horizontal | Fixed roof, floating roof | Large (>100m³) or small |
Underground Storage Tank | Crude oil, diesel, fuel oil, lubricating oil, edible oil, fire water, etc. | Vertical, horizontal | Fixed roof | Large (>100m³) or small |
The table above presents an overview of storage tank types based on their position. Aboveground storage tanks are situated above ground and can accommodate various oils, offering flexibility in applications, shapes, structures, and capacities. On the other hand, underground storage tanks are located below ground, designed to store different oils, with variations in application, shape, structure, and capacity.
In summary, the various storage tank types demonstrate their adaptability across industries. Each type is designed to meet specific requirements, accommodating materials like crude oil, diesel, and fuel oil for diverse applications in both industrial and commercial settings.
The selection of tank design considers factors such as position, shape, structure, and capacity, addressing the unique needs of different storage situations. Notably, the aboveground storage tank stands out as a crucial solution, offering accessibility, flexible placement, and various structures to handle a wide range of liquids and gases.
Moreover, to ensure the optimal performance and longevity of aboveground storage tanks, adhering to industry standards is imperative. One such standard is API 653, a comprehensive set of guidelines that outlines inspection, repair, alteration, and reconstruction practices for these tanks.
Enrolling in API 653 training programs provides industry professionals with the knowledge and skills needed to effectively maintain and assess the condition of aboveground storage tanks. These training sessions are enriched with practical case studies and interactive discussions, offering participants valuable insights into real-world scenarios.
By investing in API 653 training, individuals can enhance their expertise, ensuring that aboveground storage tanks are not only constructed and installed according to standards but also maintained and inspected with precision, contributing to the overall safety and efficiency of storage facilities.
Credit header image: iStock
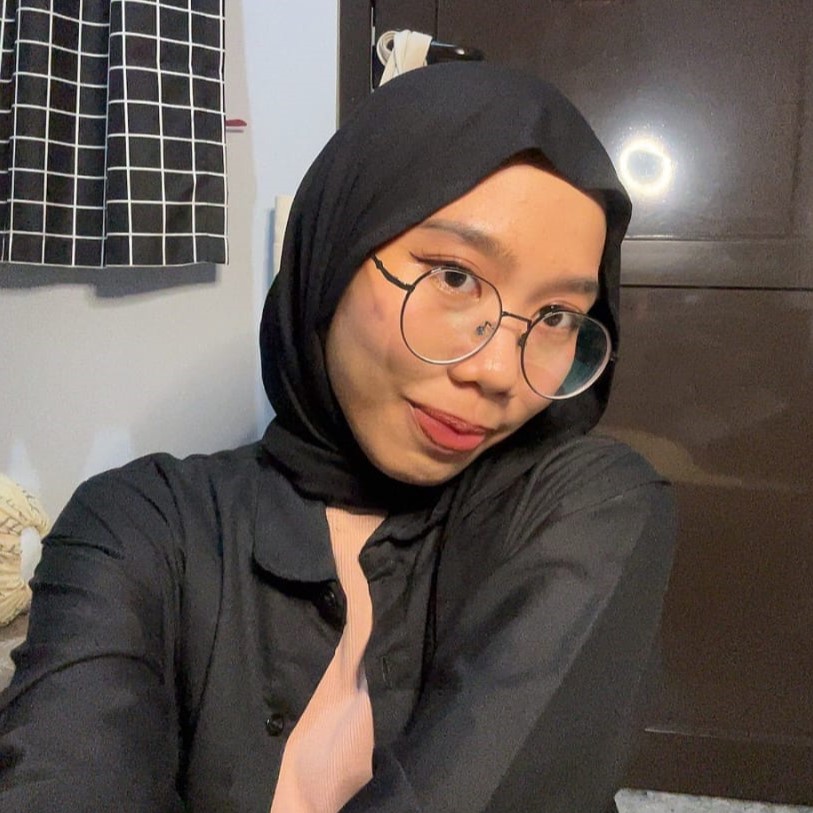
SEO specialist by day, fact-checker by night. An avid reader and content writer dedicated to delivering accurate and engaging articles through research and credible sources.