Welcome to the world of Shell and Tube Testing Inspection, a crucial process for maintaining efficiency and safety in industrial operations. This detailed guide will explore various aspects, providing valuable insights and expert knowledge to help you navigate this critical field.
What Is Shell and Tube Inspection?
Shell and tube heat exchanger inspection is a vital process to identify potential issues like corrosion, fouling, erosion, and variations in tube wall thickness. Experts use techniques such as visual inspection, eddy current testing, and ultrasonic testing to carefully examine the equipment.
During the inspection, specialists scrutinize the outer shell and the tubes within the system. They look for signs of wear and tear, corrosion, and other issues that could impact the efficiency or safety of the heat exchanger. The methods employed, including non-destructive techniques like ultrasonic testing, ensure a thorough evaluation without causing any harm to the equipment.
Regular inspections play a crucial role in catching problems early on, preventing unexpected breakdowns, and maintaining the system’s smooth operation. Additionally, these inspections, incorporating the detection of corrosion, fouling, erosion, and tube wall thickness variations, contribute to a comprehensive assessment, enhancing the overall reliability and safety of shell and tube heat exchangers
What is the Inspection Checklist of Shell and Tube Inspection?
No. |
Inspection Point |
Check & Explanation |
1. | Pressure Design Code and Applicable Local Regulations | Verify compliance with specified Pressure Design Code and local regulations. Ensure proper documentation of adherence. |
2. | Completeness and Correctness of Datasheet Information | Confirm all data, dimensions, impingement plate, and gasket recommendations are accurate and complete. Ensure no missing or inaccurate details. |
3. | Maximum Design Temperature and Minimum Design Metal Temperature | Check if these temperatures fall within specified limits to ensure equipment can operate safely under expected conditions. |
4. | Latest Issue of Process Data Sheet Followed | Verify that the most recent process data sheet version is being used to avoid outdated or incorrect information. |
5. | Specific Notes and Special Service Requirements | Check for any unique instructions or service requirements like NACE/Sour service, ensuring these are properly accounted for in the design. |
6. | Shell Internal Diameter Adequacy | Ensure the shell’s internal diameter can comfortably accommodate all tubes, considering pitch, orientation, and recommended dimensions. |
7. | Design Codes, Wind, Seismic Load, and References | Confirm utilization of correct design codes, accounting for wind and seismic loads. Verify reference books and standards with accurate edition and publication details. |
8. | Nozzle Schedule and Details | Verify nozzle details including size, rating, thickness, and surface finish. Confirm proper location and orientation of nozzles. |
9. | Test Pressure and Temperature Correction | Confirm the specified test pressure and ensure any necessary temperature correction is accurately applied. |
10. | Drawing Information | Check that drawing details align with project procedures, reference numbers, and standards. Be cautious of discrepancies. |
11. | Standard Drawing References | Ensure reference numbers for standard drawings are indicated or specified when not detailed on the drawing itself. |
12. | Datasheet Reference | Verify that the reference datasheet number with the latest revision is clearly indicated on the drawing. |
13. | Basics of Pipe Stress Analysis | Confirm that the fundamentals of pipe stress analysis are considered in the design to ensure structural integrity. |
14. | Instrument and Vent/Drain Connections | Verify the provision of instrument connections as per TEMA and check for the availability of vent or drain connections for testing. |
15. | Support Details and Foundation Bolts | Confirm support details, including lugs and saddles. Verify the size, numbers, and PCD of foundation bolts for proper anchoring. |
16. | Weld Details for Plates, Nozzles, and Attachments | Check applicable weld details for plates, nozzles, and other attachments based on material construction and thickness. |
17. | Standard Attachments and Tube Expansion Requirements | Verify provision for standard attachments like nameplates, earthing boss. Ensure compliance with tube expansion requirements. |
What Are The Stages of Inspection for Shell and Tube Inspection?
1. Manufacturing Phase Inspection
During the manufacturing phase, inspections are crucial to ensuring the quality and compliance of shell and tube heat exchangers. The process begins with adherence to the ASME Code Section VIII, covering design, materials, fabrication, and testing.
Design considerations, especially after the 2003 addenda, involve compliance with Subsection C in UHX part or acceptable alternatives like TEMA. Tube inspections are meticulous, covering dimensions such as outside and inside diameter, thickness, and ovality, following ASME Section II standards.
Tube bundle and tube sheet inspections focus on dimensions, baffle control, and cleanliness, ensuring welds meet drawing requirements. Tube rolling checks include customer-specified criteria, and if seal welding is employed, a mandatory leak test is performed. The entire structure undergoes hydrostatic testing, with inspections to verify welds, tube sheets, and the absence of leakage.
2. In-Service Inspection
In-service inspection, governed by API 510, emphasizes maintaining the integrity of shell and tube heat exchangers during operation. API-recommended practices and additional codes complement this inspection.
Qualified API 510 Pressure Vessel Inspectors play a pivotal role in ensuring ongoing reliability. The inspection involves a holistic assessment of the heat exchanger’s condition during its operational life, adhering to API standards and other relevant construction codes like ASME Section VIII and ASME Section IX.
Repair requirements are outlined by API STD 510 or ASME PCC-2, with special considerations for “U” stamped heat exchangers, necessitating the involvement of Repair Organizations holding an “R” Stamp from the National Board Inspection Code.
3. Overhaul Inspection
Overhaul inspections are essential for rejuvenating shell and tube heat exchangers, ensuring continued efficiency and safety. The stages encompass shell and structure inspection, involving neutralization, thickness measurement, and examination of weld joints and support structures.
Bonnet inspection covers thickness measurement, girth flange examination, and scrutiny of internal surfaces and welding joints. Tube bundle inspection requires careful extraction, sampling, and meticulous measurements. Channel inspection includes thickness measurements, internal surface examinations, and weld joint inspections.
Channel cover assessments involve thickness measurements, gasket seating area inspections, and internal surface evaluations. Floating head inspections encompass a range of measurements and examinations, ensuring the overall health of the heat exchanger.
Expansion joint inspections, specific to exchangers with such components, include thorough assessments of flanges, internal surfaces, and air testing, completing the comprehensive overhaul inspection process.
What Are The Advantages of Shell and Tube Inspection?
Shell and tube heat exchangers testing and inspection are advantageous in several ways below.
1. Detecting Issues Early for Prevention
Regular inspections help identify potential problems like corrosion, fouling, erosion, and variations in tube wall thickness early on. This early detection allows us to take preventive measures, reducing the risk of equipment failure and avoiding disruptions.
2. Improved Safety and Compliance
Inspections significantly contribute to a safer work environment by identifying and addressing potential hazards before they become serious. Additionally, they ensure compliance with design codes, industry standards, and regulations, strengthening safety measures in the workplace
3. Better Performance and Longevity
Regular inspections play a crucial role in avoiding costly repairs or replacements by promoting the long-term performance and health of shell and tube systems. Timely maintenance activities enhance the equipment’s overall reliability, preventing unexpected breakdowns and maintaining consistent functionality.
4. Cost Savings through Efficient Resource Management
Shell and Tube Inspection supports efficient resource management by preventing unnecessary downtime. Planned inspections and maintenance activities minimize disruptions to production schedules and help optimize the allocation of resources, resulting in significant cost savings over time.
5. Informed Decision-Making with Comprehensive Data
Inspection data provides valuable insights for making informed decisions. This data-driven approach assists organizations in making thoughtful choices about maintenance schedules, upgrades, or system modifications. The detailed information gathered during inspections contributes to strategic planning, ensuring ongoing efficiency and reliability in industrial operations.
What Are The FAQs of Shell and Tube Heat Exchanger Inspection?
1. How often should Shell and Tube Testing Inspections be conducted?
Regular inspections are recommended, varying frequency based on system age, operating conditions, and industry standards.
2. Are there portable testing methods for on-site inspections?
Portable ultrasonic testing equipment allows on-site inspections, providing flexibility and efficiency.
3. Can non-destructive testing methods identify internal corrosion?
Techniques like radiographic examination and ultrasonic testing are adept at identifying internal corrosion without causing damage.
4. What are the consequences of neglecting Shell and Tube Testing Inspection?
Neglecting inspections can decrease system efficiency, increase operational risks, and costly repairs or replacements.
5. How does Shell and Tube Testing Inspection contribute to safety?
By identifying potential issues early on, inspections contribute to a safer working environment, preventing accidents and ensuring compliance with safety standards.
6. Is Shell and Tube Testing Inspection applicable across all industries?
Yes, the principles of testing and inspection are applicable across various industries, including oil and gas, chemical, and manufacturing.
In conclusion, Shell and Tube Testing Inspection is crucial for ensuring the reliability and safety of industrial processes. Regular inspections, proactive maintenance, and the adoption of advanced testing methods collectively contribute to optimal system performance.
In summary, recognizing the significance of Shell and Tube Heat Exchanger Inspection is crucial for ensuring the dependability, safety, and effectiveness of industrial processes. The thorough checks conducted during manufacturing guarantee adherence to strict codes, preventing potential issues like corrosion and fouling.
If you want to deepen your expertise in Shell and Tube Heat Exchanger Inspection, PetroSync offers specialized Shell and Tube Heat Exchanger training. This course provides comprehensive insights into inspection techniques, industry best practices, and the latest standards.
With a focus on practical applications and real-world scenarios, PetroSync’s training programs empower professionals to enhance the performance and reliability of shell and tube heat exchangers in their respective industries. Invest in knowledge, empower your team, and elevate the efficiency of your operations through PetroSync’s dedicated training initiatives.
Credit header image: iStock
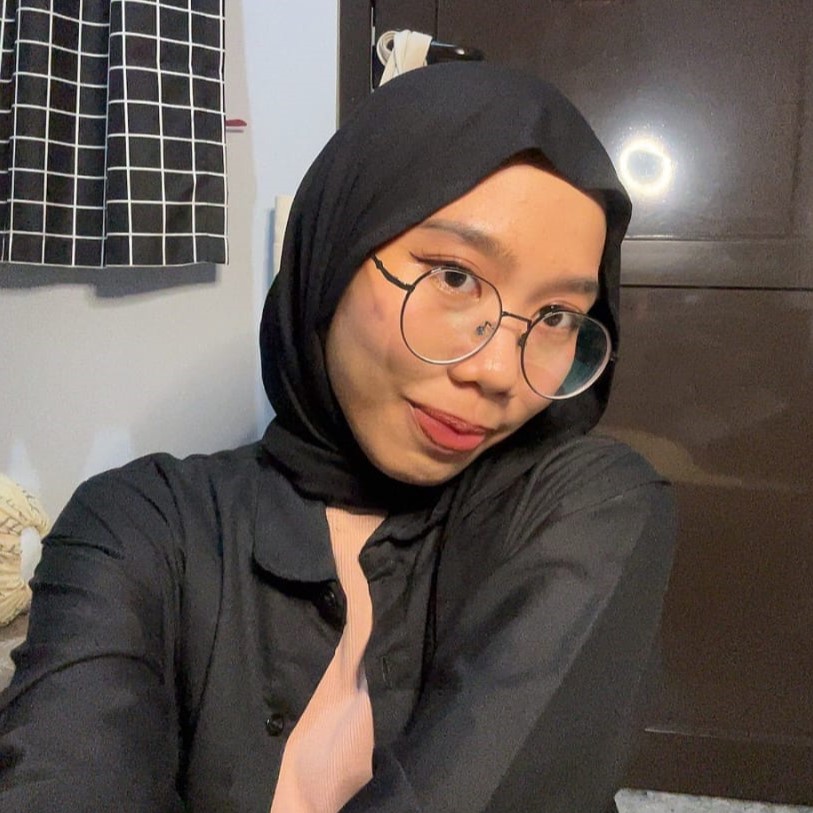
SEO specialist by day, fact-checker by night. An avid reader and content writer dedicated to delivering accurate and engaging articles through research and credible sources.