Refractory failures pose intricate challenges that require a thorough understanding. In this article, we explore the essence of these failures, deciphering what causes them, understanding their symptoms, and discussing possible remedies. Whether you’re an experienced professional or a curious learner, this guide seeks to illuminate the realm of refractory materials and the challenges they face.
What Is Refractory Failure?
Refractory failures, the situation where materials lining high-temperature structures lose effectiveness, are significant issue. It stands as the number one cause of boiler inefficiency and a major contributor to boiler shutdowns. This failure can result from aging, exposure to extreme temperatures, mechanical stress, or improper installation.
When refractory materials fail, it not only compromises performance but also poses safety risks, necessitating repairs or replacements to ensure continued operational integrity. A well-chosen and properly installed refractory lasts longer, reduces shutdowns, and saves on annual fuel costs.
What Led to The Failure of The Refractory?
The refractory faced failure due to various factors, including aging, exposure to extreme temperatures, mechanical stress, and, notably, improper installation or maintenance. Issues related to installation techniques, curing time, insufficient support, or the use of subpar materials played a role in weakening the refractory, ultimately contributing to its failure.
1. Deterioration Due to Length of Service
Refractory materials, over time, change their physical properties due to continuous use. The high-temperature environment causes alterations in the binders within the materials, leading to a loss of surface or internal strength. This is particularly significant for materials under compressive loads, like bricks or castable linings, where local or widespread failure can occur. Additionally, prolonged exposure to flame impingement, every day in many radiant wall applications, can shorten the useful life of the refractory.
2. Incompatible Refractory Materials
Using various refractory materials in combination, as often seen in fired heaters, can present challenges. Openings like doors may utilize a mix of fiber and brick material, and peep sights could involve IFB, castable, or fiber modules.
Standardized design incorporating different materials becomes intricate as each material exhibits varying properties at high temperatures. This can result in damaged refractory linings, exposing the shell to hot flue gases and causing hot spots. To mitigate the risk of mismatched refractory materials, close collaboration with the refractory supplier to ensure compatibility around openings is advisable.
3. Loss of Support
All refractory linings rely on external steel shell support in fired heaters. Anchoring systems, typically welded to the shell, provide this support. However, corrosion often compromises the welded joint between the shell and the anchor.
The corrosion is the consequence of hot flue gases penetrating the refractory lining, condensing upon reaching the cooler shell, and creating an environment conducive to rapid oxidation or corrosion at the weld. Once support is lost, individual components like bricks or modules can detach, exposing the metal shell and triggering a cascading failure of adjacent refractory lining.
4. Mechanical Stress
Several factors contribute to mechanical stress leading to refractory failures. Vibrations from equipment or thermal expansion and spalling, occurring when refractory linings expand and contract at different rates due to thermal conditions, can result in cracking and spalling. Additionally, mechanical impact, such as from falling objects or components, can cause damage to the refractory. These mechanical stresses, if not addressed, can lead to failure over time.
5. Poor Installation and Maintenance
Inadequate installation or maintenance stands as a frequent cause of refractory failure. Elements like installation methods, curing duration, insufficient support, or substandard materials can undermine the refractory, contributing to its breakdown.
The installation of refractory begins during manufacturing, emphasizing the need for effective communication between the manufacturer and the plant. This collaboration is vital to ensure refractory suitability, making it resistant to thermal stresses and environmental processes. Critical parameters, including temperatures, start-ups and shutdowns, flue gas temperature, chemical components, and required heat loss, must be thoroughly evaluated.
Post-manufacturing, the refractory should be stored in a dry, well-ventilated space and installed within three months for environments with high temperatures or abrasion. When installed and maintained correctly, refractory linings can endure for 20 years or more. However, signs of issues during installation, such as fallen fiber modules or gaps, may indicate problems like insufficient stud welding or potential shell corrosion. While various installation issues can lead to refractory failure, routine and thorough inspections are crucial in early damage detection, facilitating timely remedial actions.
How To Repair Refractory?
1. Dry Gunning
The dry gunning technique for refractory repair involves a straightforward process using a configured system with a material tank, a high-pressure air gun, and a specialized nozzle.
The procedure includes selecting suitable refractory material, preparing a binder-mixed powder, and drawing materials for mixing with water at the nozzle before being propelled onto the repair area. This system is known for its simplicity, versatility for both cold and hot repairs, and the suitability of silicate and phosphate binders for high temperatures.
2. Wet Gunning
To repair refractory using the wet gunning technique, a wet gunning system is employed. This method addresses the mixing challenges associated with dry gunning. In the wet gunning system, a water-kneaded refractory mixture is pumped to a nozzle, which is augmented with a set accelerator before being applied to the repair area.
The set accelerator, an alkaline solution, facilitates the hardening process. The pump utilized can be a squeeze type, double-piston type, or screw type. Unlike dry gunning, the shotcrete mixture in wet gunning is kneaded beforehand, reducing water content and porosity, and resulting in improved durability.
3. Injection
In the injection technique for refractory repair, the process involves pumping a kneaded mixture to the desired installation position and injecting the material into the repair area. This technique finds utility in injecting refractory material between the steel shell and the brick lining of hot blast stoves and blast furnaces. These examples highlight the versatility of the injection method in addressing various refractory repair scenarios across industrial applications.
4. Thermal Spraying
When employing the thermal spraying technique for refractory repair, the process involves spraying a molten or semi-molten refractory material onto the repair area. There are two primary methods for thermal spraying in refractory repair. The first is the lava flame method, where finely crushed refractory material is mixed with oxygen and propane, melted by the flame’s heat, and sprayed onto the repair area.
The second method is the thermite gunning method, where refractory material is mixed with silicon metal and carried by oxygen. The thermite reaction between the metal and oxygen bonds the refractory material to the repair surface. The thermite gunning method, known for its simplicity, is primarily used to repair coke oven opening walls. These thermal spraying techniques offer versatile solutions for maintaining and restoring refractory linings in various industrial applications.
5. Hot Casting
Repairing refractory through the hot casting technique involves a straightforward process. This method combines the refractory material with a binder, such as phenol resin or pitch, forming a mixture that is then bagged and introduced into the furnace. The binder serves to soften and harden, facilitating the installation of the refractory lining.
It is important to note that the casting material is fluid in its hot state. However, the evaporation of volatile matter in the binder extends the hardening time. Due to this characteristic, the hot casting method is unsuitable for vertical walls and similar areas. Its primary application is in repairing the linings of converters, where its fluidity and hardening properties prove effective in the restoration process.
Refractory failures, arising from aging, extreme temperatures, and improper installation, pose significant challenges, leading to reduced efficiency, boiler shutdowns, and safety hazards. Addressing these issues requires careful material selection and adherence to proper installation procedures, considering factors such as temperature, start-ups, shutdowns, and chemical components.
To gain expertise in refractory inspection and repair while avoiding refractory failures, consider enrolling in API 936 training. This API 936 certification offers specialized knowledge in material selection, installation, and inspection procedures, crucial for managing refractory systems effectively. Obtaining API 936 certification demonstrates a commitment to industry best practices and equips individuals to address refractory maintenance challenges, contributing to industrial systems’ longevity and reliability.
Credit header image: iStock
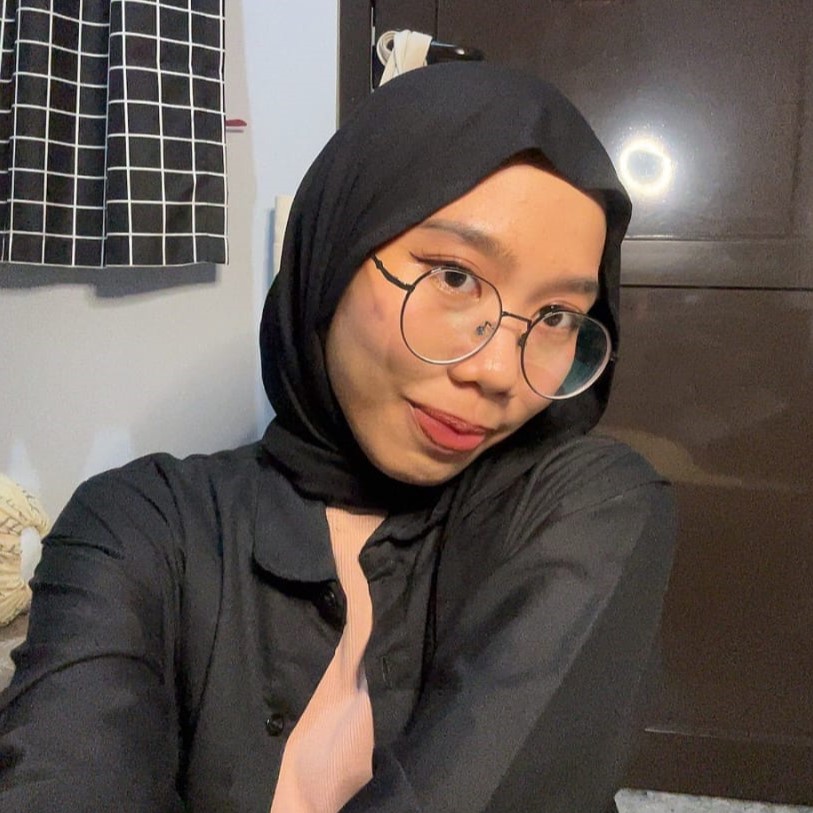
SEO specialist by day, fact-checker by night. An avid reader and content writer dedicated to delivering accurate and engaging articles through research and credible sources.