In the engineering world, keeping pipes strong and reliable is crucial, especially when following standards like ASME B31.3. Piping testing is a vital process that ensures these pipes meet strict rules for strength and dependability. This article explores different tests, from checking for pressure to finding leaks, and their important role in making sure engineering systems work well. Join us as we go through these essential tests that help keep pipes strong and operations smooth and safe.
What Is Piping Used for Industry?
Piping, essential for transporting fluids like liquids and gases, is integral to diverse industries. These industrial piping systems find application in water management, manufacturing, engineering, chemical processes, food production, and various other sectors. They play a crucial role in facilitating efficient and safe material conveyance within industrial environments, contributing significantly to the functioning of different industries.
So, what exactly is industrial piping? Industrial piping is crafted from various materials like aluminum, iron, and concrete. The choice of material depends on the specific industry’s requirements. The material selected must align with the operating conditions to ensure safety under potential factors like temperature, erosion, pressure, or corrosion.
What Is Piping Testing?
Piping testing refers to the evaluation process of assessing the ability of pipes to withstand consistent internal pressure under unchanging temperature conditions. In simpler terms, it involves examining how well pipes can endure the pressure from substances flowing inside them while maintaining a constant temperature. By subjecting pipes to various tests, engineers can identify and address potential problems, ensuring the safety and efficiency of the overall system.
What Are The Benefits of Following International Standards for Piping Testing?
Following international standards for piping testing offers several advantages:
1. Safety Assurance
Adhering to established international standards ensures that piping testing procedures prioritize safety. This reduces the risk of potential accidents or failures, safeguarding both personnel and the environment.
2. Consistency and Reliability
International standards provide a consistent framework for piping testing across different regions and industries. This consistency enhances the reliability of testing results, making it easier to compare and share valuable insights globally.
3. Compliance and Industry Recognition
Conforming to international standards demonstrates a commitment to industry best practices. It enhances the credibility of piping testing processes, ensuring compliance with recognized benchmarks and gaining trust and recognition within the global industrial community.
How to Conduct Piping Testing per ASME B31.3?
By doing the following steps under ASME B31.3, you ensure a comprehensive and standardized approach to piping testing, promoting the integrity and safety of your piping systems.
1. Required Leak Test
Before initiating piping testing according to ASME B31.3, there are considerations and options outlined to ensure the integrity of the piping system. The primary testing method recommended is a hydrostatic leak test, as per para. 345.4. However, the owner has flexibility in certain situations. In Category D fluid service, an initial service leak test may be opted for instead of the hydrostatic test. Considerations for Piping Testing Methods:
Condition |
Consideration |
Category D Fluid Service | Initial service leak test may be considered as an option for hydrostatic leak test. |
Impracticality of Hydrostatic Test | Pneumatic test or combined hydrostatic-pneumatic test may be alternatives, recognizing hazards. |
Impracticality of Both Tests | Alternative specified in para. 345.9 may be used if specific conditions apply. |
These considerations provide a comprehensive framework for owners to choose the most suitable testing method.
2. General Requirement for Leak Test
When conducting a leak test as per ASME B31.3, several requirements outlined in para. 345.2 must be considered to ensure the effectiveness and safety of the testing process. These requirements cover various aspects, including pressure limitations, examination for leaks, heat treatment, and special provisions for testing specific components.
Considerations for Leak Testing (ASME B31.3, para. 345.2):
Requirement |
Consideration |
Pressure Limitations (para. 345.2.1) | Control test pressure to avoid exceeding yield strength or component ratings; consider reduced pressure if needed. |
Examination for Leaks (para. 345.2.2) | Maintain test pressure, examine joints for leaks, and conduct inspections for at least 10 minutes. |
Special Provisions (para. 345.2.3) | Specific provisions for testing components, flanged joints, closure welds, instrument connections, and more. |
Externally Pressured Piping (para. 345.2.4) | Pressure requirements for piping systems under external pressure; considerations for vacuum service. |
Jacketed Piping (para. 345.2.5) | Leak testing procedures for the internal line and jacket; considerations for repairs or additions. |
Repairs or Additions After Leak Testing (para. 345.2.6) | Retesting requirements after repairs or additions; potential waiver for minor repairs with precautionary measures. |
Test Records (para. 345.2.7) | Document key information during testing, including date, system identification, test fluid, pressure, and results. |
Adhering to these considerations ensures a comprehensive and compliant leak testing process in line with ASME B31.3 standards.
3. Preparation for Leak Test
When conducting leak tests according to ASME B31.3, specific considerations must be taken into account during the examination of joints and other components. Considerations for Leak Testing Joints and Components (ASME B31.3, para. 345.3):
Requirement |
Consideration |
Joints Exposed (para. 345.3.1) | Considerations for insulating joints, with specific options for different fluid services and leak test types. |
Temporary Supports (para. 345.3.2) | Additional supports for vapor or gas piping to bear the weight of the test liquid. |
Piping With Expansion Joints (para. 345.3.3) | Specific leak test procedures for unrestrained and self-restrained expansion joints. |
Limits of Tested Piping (para. 345.3.4) | Protocols for equipment not undergoing testing, including disconnection or isolation by blinds or valves. |
Adhering to these considerations ensures a comprehensive and compliant leak testing process in line with ASME B31.3 standards.
4. Hydrostatic Leak Test
When conducting a hydrostatic leak test per ASME B31.3, careful considerations must be made regarding the test fluid, test pressure, and specific conditions involving piping connected to vessels. The test fluid is typically water unless freezing or adverse effects are possible, in which case a suitable non-toxic liquid may be used, provided it meets safety criteria, including a flash point above 49°C (120°F) for flammable liquids.
Considerations for Hydrostatic Leak Test (ASME B31.3, para. 345.4):
Requirement |
Consideration |
Test Fluid (para. 345.4.1) | Selection of test fluid, typically water, unless freezing or adverse effects warrant another suitable non-toxic liquid. |
Test Pressure (para. 345.4.2) | Determination of hydrostatic test pressure based on design pressure, temperature, and ST/S ratio considerations. |
Hydrostatic Test of Piping With Vessels (para. 345.4.3) | Specific conditions for testing piping connected to vessels, considering test pressure relationships and isolation feasibility. |
Adhering to these considerations ensures a comprehensive and compliant hydrostatic leak test in line with ASME B31.3 standards.
5. Pneumatic Leak Test
When performing a pneumatic leak test according to ASME B31.3, several crucial considerations must be taken into account to ensure safety and effectiveness. Pneumatic testing involves the risk of released energy stored in compressed gas, posing a potential hazard for brittle failure.
Considerations for Pneumatic Leak Test (ASME B31.3, para. 345.5):
Requirement |
Consideration |
Precautions (para. 345.5.1) | Minimization of the chance of brittle failure during pneumatic testing; consideration of test temperature and material choice. |
Pressure Relief Device (para. 345.5.2) | Mandatory provision of a pressure relief device with set pressure limits to prevent over-pressurization during testing. |
Test Fluid (para. 345.5.3) | Selection of a nonflammable and nontoxic gas as a test fluid if air is not used, ensuring safety during the testing process. |
Test Pressure (para. 345.5.4) | Determination of the appropriate test pressure within specified limits to ensure a safe and effective testing environment. |
Procedure (para. 345.5.5) | Gradual pressure increase, preliminary checks, and examination steps to equalize piping strains, followed by pressure reduction for leakage examination. |
Careful attention to test temperature and material choice during the design phase is essential to mitigate this risk. The standards highlight the importance of these considerations in maintaining safety during the pneumatic leak test, as outlined in para. 345.2.2(c) and Appendix F, paras. F323.4 and F345.5.1.
6. Hydrostatic-Pneumatic Leak Test
If you choose to conduct a combined hydrostatic-pneumatic leak test, it’s essential to follow the guidelines outlined in para. 345.5. Additionally, ensure that the pressure within the liquid-filled portion of the piping does not surpass the limits specified in para. 345.4.2.
7. Initial-Service Leak Test
When conducting an Initial Service Leak Test as per ASME B31.3, specific considerations and procedures must be followed, particularly for piping in Category D Fluid Service as chosen by the owner (see para. 345.1(a)). The test fluid used is the service fluid itself.
Considerations for Initial Service Leak Test (ASME B31.3, para. 345.7):
Requirement |
Consideration |
Piping Category (para. 345.7.1) | Applicability limited to Category D Fluid Service piping, at the owner’s discretion (see para. 345.1(a)). |
Test Fluid (para. 345.7.1) | Use of the service fluid itself as the test fluid. |
Procedure (para. 345.7.2) | Gradual pressure increase in steps until operating pressure is reached, with adequate time for strain equalization. |
Preliminary Check (para. 345.7.2) | If the service fluid is a gas or vapor, conducting a preliminary check in line with para. 345.5.5. |
Examination for Leaks (para. 345.7.3) | Examination for leaks at operating pressure, with the option to omit examination for previously tested joints and connections. |
Following these considerations ensures a comprehensive and compliant Initial Service Leak Test as per ASME B31.3 standards.
8. Sensitive Leak Test
When performing the Sensitive Leak Test as per ASME B31.3, specific considerations and procedures must be adhered to ensure accurate detection of leaks in the piping system. This test, utilizing the Bubble Test — Direct Pressure Technique outlined in the BPV Code, Section V, Article 10, Appendix I, or an alternative method with demonstrated sensitivity not less than 10^(-3) std ml/s under test conditions, is designed to identify even the smallest leaks.
In the case of the Bubble Test — Direct Pressure Technique, the following steps must be followed:
- Test Pressure (para. 345.8): The test pressure should be at least the lesser of 105 kPa (15 psi) gage or 25% of the design pressure.
- Gradual Pressure Increase (para. 345.8): The pressure should be gradually increased until a gage pressure equal to the lesser of one-half the test pressure or 170 kPa (25 psi) is attained. At this point, a preliminary check is conducted.
- Incremental Pressure Increase (para. 345.8): The pressure is then gradually increased in steps until the test pressure is reached. At each step, the pressure is held long enough to allow for the equalization of piping strains.
Considerations for Sensitive Leak Test (ASME B31.3, para. 345.8):
Requirement |
Consideration |
Leak Test Method (para. 345.8) | Utilization of the Bubble Test — Direct Pressure Technique or an alternative method with demonstrated sensitivity. |
Test Pressure (para. 345.8(a)) | The test pressure should be at least the lesser of 105 kPa (15 psi) gage or 25% of the design pressure. |
Gradual Pressure Increase (para. 345.8(b)) | Incremental pressure increase until a gage pressure equal to one-half the test pressure or 170 kPa (25 psi) is attained. |
Preliminary Check (para. 345.8(b)) | Conducting a preliminary check at the specified gage pressure before further incremental increases. |
Adhering to these considerations ensures a thorough and sensitive leak test, meeting the standards set by ASME B31.3.
8. Alternative Leak Test
In the context of ASME B31.3’s Alternative Leak Test, specific considerations and actions must be taken under the conditions outlined in para. 345.1(c). This alternative approach involves a multi-step process to ensure the integrity of the piping system.
Considerations for Alternative Leak Test (ASME B31.3, para. 345.9):
Requirement |
Consideration |
Examination of Welds (para. 345.9.1) | Thorough examination of welds, including 100% radiographic or ultrasonic examination for specific weld types. Liquid penetrant or magnetic particle methods for other welds. |
Flexibility Analysis (para. 345.9.2) | Conducting a flexibility analysis of the piping system to ensure it can effectively handle stresses and strains. |
Test Method (para. 345.9.3) | Subjecting the piping system to a sensitive leak test, following the specifications outlined in para. 345.8, for accurate leak detection and system integrity. |
Following these considerations guarantees a comprehensive approach to the Alternative Leak Test, aligning with the guidelines set by ASME B31.3.
In conclusion, the process of piping testing, as meticulously outlined by ASME B31.3, ensures the robustness and safety of piping systems. The comprehensive steps, ranging from the initial considerations before testing to the specific leak test methods, contribute to the reliability and functionality of the piping infrastructure. The standards not only emphasize the importance of traditional hydrostatic testing but also provide alternatives, such as pneumatic and sensitive leak tests, demonstrating the adaptability of the guidelines to various operational conditions.
For you aiming to deepen your understanding of ASME B31.3 and become experts in piping, PetroSync offers specialized training programs. This ASME B31.3 training is meticulously designed to equip you with the knowledge and skills necessary to navigate the intricacies of ASME B31.3, ensuring strict compliance with industry standards.
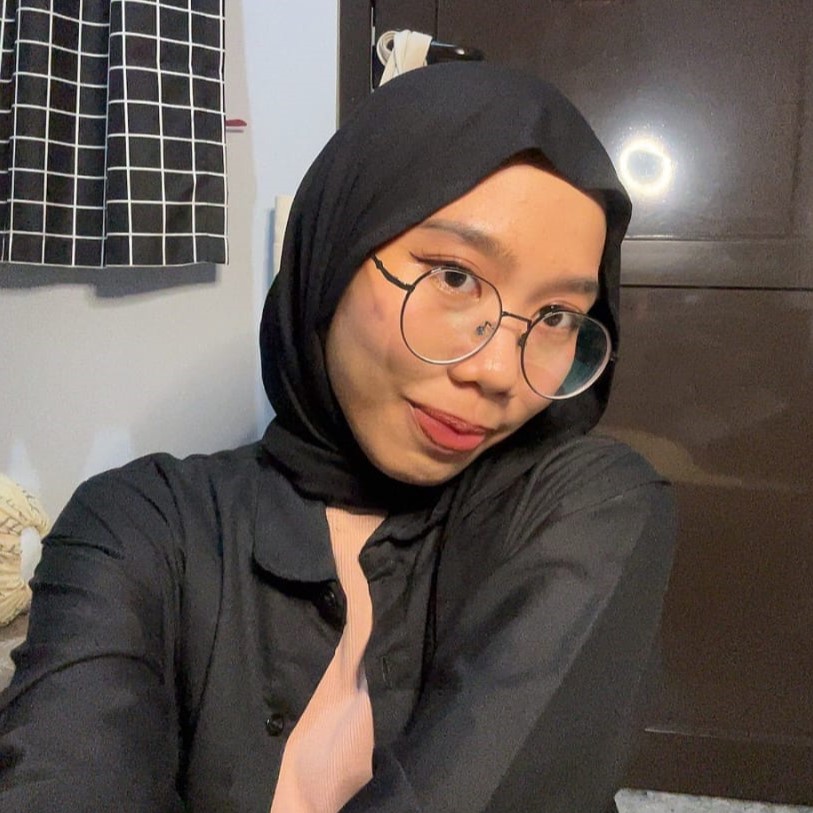
SEO specialist by day, fact-checker by night. An avid reader and content writer dedicated to delivering accurate and engaging articles through research and credible sources.