In the dynamic world of industries, maintaining efficient operations is an ongoing challenge. To improve productivity and minimize disruptions, having a well-thought-out maintenance strategy is crucial. This article delves into the details of creating a maintenance plan that ensures equipment and systems run smoothly, contributing to overall operational efficiency.
What Is a Maintenance Strategy?
A maintenance strategy is a systematic approach to ensuring equipment reliability and optimal performance in an industrial setting, outlining how an organization will manage the upkeep and care of its assets or equipment. It involves making decisions about when and how maintenance activities will be performed to ensure that assets operate efficiently and reliably.
The strategy considers factors such as preventive maintenance, predictive maintenance, corrective maintenance, and the allocation of resources. In essence, it’s a structured plan that guides the maintenance activities to maximize the lifespan and performance of assets while minimizing downtime and costs.
What Are The 4 Types of Maintenance Strategies?
In general, there are four types of maintenance strategies:
1. Corrective Maintenance
Corrective maintenance, which falls under the category of maintenance tasks, refers to the repair and restoration activities performed on equipment or systems after a failure or malfunction has occurred.
In this approach, maintenance is carried out to fix the specific issue that caused the equipment to stop functioning correctly. It aims to return the equipment to its normal operational state, addressing the root cause of the problem. While it helps in resolving immediate issues, it is reactive in nature, responding to failures rather than preventing them.
2. Preventive Maintenance
Preventive maintenance, the act of performing regularly scheduled maintenance activities to help prevent unexpected failures in the future, is a planned and proactive approach to maintaining equipment or systems before any issues or failures occur.
It involves scheduled inspections, repairs, and replacements of components to prevent potential problems and ensure that the equipment continues to function smoothly. The goal is to anticipate and address issues before they lead to breakdowns, minimizing downtime and extending the lifespan of the equipment.
3. Risk-based Maintenance
Risk-based maintenance, the act of performing regularly scheduled maintenance activities to help prevent unexpected failures in the future, is a methodology for optimizing maintenance tasks and resource allocation.
Instead of treating all assets equally, this method focuses resources on areas with higher risks of failure or significant consequences if a failure occurs. It involves assessing the likelihood and impact of potential failures and then allocating maintenance efforts accordingly. By addressing high-risk areas first, organizations can enhance the reliability of critical systems, reduce unexpected breakdowns, and optimize the use of resources.
4. Condition-based Maintenance
Condition-based maintenance, a maintenance strategy that monitors the condition of an asset to determine what maintenance is needed, is an approach where maintenance activities are performed based on the actual condition of equipment or systems rather than a predetermined schedule. It involves using sensors and monitoring tools to continuously assess the health and performance of assets.
When specific conditions or indicators suggest potential issues or degradation, maintenance is then scheduled. This method aims to optimize maintenance efforts, reduce unnecessary interventions, and address problems when they are most likely to occur, promoting efficiency and minimizing downtime.
You can check the table below for a concise overview of the benefits and drawbacks associated with each of the four maintenance strategies
Maintenance Strategy |
Benefits |
Drawbacks |
Corrective Maintenance | Minimal upfront planning and costs. | Unplanned downtime and production losses. |
Resources are only used when issues arise. | Potential for higher repair costs due to emergency responses. | |
Suitable for non-critical equipment or systems. | Increased risk of safety incidents. | |
Shortened equipment lifespan due to reactive rather than proactive approach. | ||
Preventive Maintenance | Proactive approach reduces the likelihood of unexpected failures. | Can lead to unnecessary maintenance if schedules are too frequent. |
Extended equipment lifespan through regular care and monitoring. | Downtime for scheduled maintenance may disrupt operations. | |
Helps in identifying and addressing potential issues before they escalate. | Fixed schedules may not align with actual equipment condition. | |
Upfront costs for regular maintenance activities. | ||
Risk-based Maintenance | Targets high-risk areas, optimizing resource allocation. | Initial setup for risk assessment can be time-consuming. |
Reduces the likelihood of critical failures with focused attention. | Requires expertise in risk assessment and analysis. | |
Cost-effective by prioritizing maintenance efforts based on risk levels. | Continuous monitoring and updates to risk assessments are necessary. | |
May not address low-probability, high-consequence events effectively. | ||
Condition-based Maintenance | Optimizes maintenance efforts by addressing issues when they arise. | Initial investment in monitoring equipment and sensors. |
Minimizes unnecessary maintenance by responding to actual equipment conditions. | Ongoing monitoring may require skilled personnel. | |
Reduces downtime by addressing issues at their early stages. | Possibility of false alarms leading to unnecessary interventions. | |
May not be suitable for non-critical or easily replaceable equipment. |
How Do I Develop A Maintenance Strategy?
To develop a maintenance strategy, you need a systematic approach that considers the critical assets in your operations and aligns with your business goals. Here are the steps to guide you through the process:
1. Identify Critical Assets and Assess Current Maintenance Capabilities
To begin developing an effective maintenance strategy, first, identify critical assets vital for safety and production. Evaluate your current maintenance capabilities, considering how well-established your processes and systems are. Beyond fixing issues, emphasize planning, organization, and technical capabilities crucial for adopting a more proactive strategy.
2. Evaluate Existing Operations Performance and Establish Maintenance Objectives
Assess the performance of your current operations to understand your standing and success in maintenance. Collect and analyze data on equipment availability, downtime, causes of failures, and expenditure. Align these insights with your operational facilities and overall business goals. This analysis will guide you in setting clear and relevant maintenance objectives.
3. Select an Appropriate Maintenance Approach for Your Assets
Choosing the appropriate maintenance approach is essential for safety and cost-effectiveness. Whether preventive, predictive, or run-to-failure, select the approach based on asset criticality and condition. For key assets, deliberately choose the right maintenance approach for each equipment failure type, minimizing the overall cost to the organization.
4. Formulate a Comprehensive Maintenance Plan
Once the appropriate approach is identified, create a well-structured maintenance plan aligned with set objectives. Clearly outline all necessary maintenance activities, their schedule, frequency, and required resources or spare parts. This comprehensive guide helps maintenance teams understand what needs to be done and why, optimizing their work effectiveness.
5. Execute the Maintenance Plan
With the developed plan in hand, it’s time to put it into action. Plan and schedule maintenance activities, allocate resources, assign tasks, and ensure correct execution. Implement a structured project management approach to minimize resistance and ensure successful execution. Training can further solidify lasting change and commitment from every team member.
6. Monitor Outcomes and Refine the Strategy
Continuously monitor asset performance and collect data to analyze results. Utilize maintenance analytics and benchmarking tools to understand performance gaps. Evaluate whether the strategy is effective, identify areas for improvement, and maximize production while enhancing safety. Regularly update and refine the strategy to align with changing business needs and goals.
7. Establish a Continuous Feedback Loop
Identifying areas for improvement in your maintenance plan is one thing, but it’s crucial to implement continuous improvements. Establish a feedback loop to integrate insights gained from analyzing maintenance activities back into the strategy. Maintenance strategies should be dynamic, constantly updated, and refined to reflect evolving business needs and goals.
In summary, creating a thorough maintenance strategy is crucial for the reliability, safety, and efficiency of your operational assets. By carefully identifying critical assets, aligning maintenance objectives with business goals, and executing a clear maintenance plan, you set the stage for optimized operations.
Importantly, this approach seamlessly aligns with the principles of Reliability Centered Maintenance (RCM). RCM emphasizes a systematic analysis of potential failures, prioritizing maintenance tasks based on risk and criticality. Integrating RCM principles into your maintenance strategy enhances its effectiveness, fostering proactive maintenance practices and overall improved asset performance.
As you aim to enhance your maintenance skills and embrace the principles of Reliability Centered Maintenance, we strongly suggest considering RCM training provided by PetroSync. PetroSync offers thorough and specialized training programs that dive into the details of RCM methodology.
This training will equip you with the skills and knowledge necessary to seamlessly incorporate RCM principles into your maintenance strategy. By enrolling in PetroSync’s RCM training, you invest in your professional growth and position yourself as a valuable asset to your organization. Seize the opportunity to deepen your understanding of RCM and its practical applications, ultimately contributing to the reliability and success of your operational assets.
Credit: Freepik
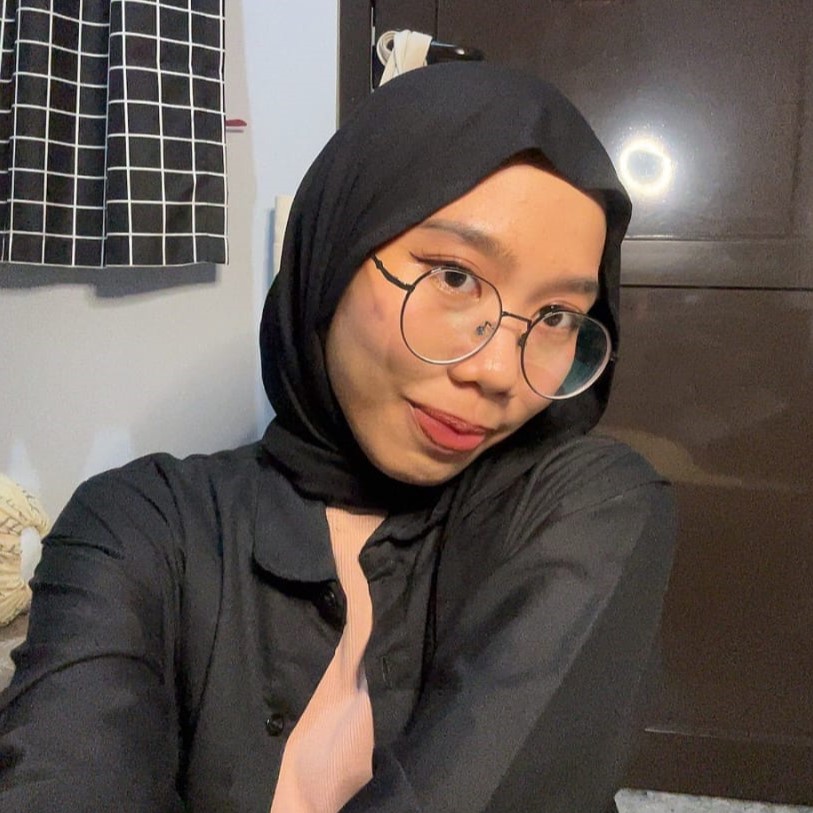
SEO specialist by day, fact-checker by night. An avid reader and content writer dedicated to delivering accurate and engaging articles through research and credible sources.