Let’s explore how maintenance and reliability management are connected and the important areas they cover. Discussion in this article includes how maintenance practices and reliability principles work together to make sure equipment works well and problems are minimized.
What Is Maintenance?
Maintenance refers to a set of processes and practices that aim to ensure the continuous and efficient operation of machinery, equipment, and other types of assets typically used in business. It involves regular inspections, repairs, and upkeep to prevent breakdowns and ensure that equipment, machinery, or systems function effectively and safely.
Maintenance can include tasks such as cleaning, lubricating, replacing worn parts, and conducting inspections to identify potential issues before they escalate into larger problems. Overall, maintenance is essential for prolonging the lifespan and optimizing the performance of assets, whether they are household appliances, vehicles, industrial machinery, or infrastructure.
What Are Some Types of Maintenance?
1. Preventive Maintenance
Preventive maintenance involves performing regular and periodic tasks according to predefined schedules. These tasks aim to prevent equipment failure and prolong the lifespan of assets by addressing potential issues before they escalate. Examples include routine inspections, lubrication, filter changes, and calibration.
2. Corrective Maintenance
Corrective maintenance occurs in response to an identified issue or failure. When a problem is noticed, corrective action is taken to repair or restore the equipment to its normal operating condition. This type of maintenance is reactive and aims to minimize downtime and restore functionality quickly.
3. Predetermined Maintenance
Predetermined maintenance follows a predefined schedule provided by the manufacturer or based on historical data and industry standards. It typically involves routine servicing or replacement of components at specified intervals, regardless of the equipment’s condition. This approach helps ensure consistent and proactive maintenance of assets.
4. Condition-Based Maintenance
Condition-based maintenance involves monitoring the condition of equipment and performing maintenance tasks when a specific condition or threshold is reached. This approach relies on sensors, monitoring systems, and diagnostic tools to assess the health and performance of assets in real-time. Maintenance activities are triggered based on indicators such as temperature, vibration, fluid levels, or other relevant parameters.
5. Predictive Maintenance
Predictive maintenance utilizes data-driven techniques and analytics to forecast equipment failures and schedule maintenance proactively. By analyzing historical data, trends, and patterns, predictive maintenance algorithms identify potential issues and recommend maintenance actions before they occur. This approach aims to minimize unplanned downtime, optimize maintenance resources, and maximize asset availability and reliability.
6. Reactive Maintenance
Reactive maintenance, also known as breakdown maintenance, occurs in response to a total breakdown or failure of equipment. When an unexpected failure happens, immediate action is taken to repair the equipment and restore functionality. While reactive maintenance can be costly and disruptive due to unplanned downtime, it is necessary for addressing emergencies and critical situations.
What Is Reliability?
Reliability refers to the engineering discipline for applying scientific know-how to a component, product, plant, or process in order to ensure that it performs its intended function consistently and predictably over time without experiencing failures or breakdowns. It is a measure of how dependable and trustworthy a system, process, or product is in meeting its intended purpose or function.
In essence, reliability ensures that something operates smoothly and efficiently without unexpected interruptions or malfunctions. It is an important factor in determining the overall quality and performance of equipment, machinery, and systems, as well as in maintaining the trust and satisfaction of users or customers.
What Are Reliability Metrics?
Reliability metrics are quantitative measures used to assess the performance and reliability of a component, product, or system. They help in evaluating the likelihood of failures and the ability of the item to meet its intended function consistently. Here are four common reliability metrics:
1. Failure Rate
The failure rate refers to the frequency at which a component or system fails over a specific period. It is typically expressed as the number of failures per unit of time, such as failures per hour or failures per million hours of operation. A lower failure rate indicates higher reliability.
2. Mean Time Between Failures (MTBF)
MTBF is the average time interval between consecutive failures of a component or system. It is calculated by dividing the total operating time by the number of failures observed during that period. MTBF provides an estimate of the expected time between failures and is commonly used to assess the reliability of repairable systems.
3. Mean Time to Failure (MTTF)
MTTF is similar to MTBF but is used for non-repairable systems or components. It represents the average time that a component or system operates before experiencing a failure. MTTF is calculated by dividing the total operating time by the number of failures observed. It is particularly useful for assessing the reliability of items that cannot be repaired and must be replaced after failure.
4. Mean Time to Repair (MTTR)
MTTR measures the average time required to repair a failed component or system and restore it to normal operation. It includes the time spent diagnosing the problem, obtaining replacement parts, and performing the necessary repairs. MTTR is crucial for assessing the maintainability and downtime associated with failures. A lower MTTR indicates faster repair times and better overall reliability.
Depending on the type and purpose of the product or system being evaluated, one or more of these metrics may be used to set reliability goals and assess test results. By monitoring these reliability metrics, engineers and stakeholders can identify areas for improvement, implement corrective actions, and ensure that products meet performance expectations and customer requirements.
What Are The 5 Pillars of Maintenance and Reliability?
The five pillars of maintenance and reliability are essential aspects that contribute to the effective management and optimization of assets and systems:
1. Business Processes
Business processes encompass the strategies, procedures, and workflows established to manage maintenance and reliability activities within an organization. These processes ensure alignment with overall business objectives, facilitate efficient resource allocation, and promote continuous improvement in maintenance practices.
2. Workforce Management
Workforce management involves the recruitment, training, scheduling, and supervision of personnel responsible for maintenance and reliability tasks. It focuses on developing skilled and motivated teams capable of effectively executing maintenance activities, troubleshooting issues, and implementing preventive measures to minimize downtime and maximize asset performance.
3. Materials Management
Materials management involves the procurement, inventory control, and distribution of spare parts, tools, and consumables necessary for maintenance and repair activities. Effective materials management ensures that the right materials are available at the right time and place, minimizing delays and optimizing maintenance efficiency.
4. Asset Management
Asset management encompasses the strategic planning, monitoring, and optimization of physical assets throughout their lifecycle. It involves identifying critical assets, assessing their condition, prioritizing maintenance interventions, and making data-driven decisions to maximize asset reliability, availability, and performance while minimizing the total cost of ownership.
5. Performance Management
Performance management involves the measurement, analysis, and improvement of maintenance and reliability performance indicators. It includes establishing key performance indicators (KPIs), collecting and analyzing relevant data, identifying areas for improvement, and implementing corrective actions to enhance overall maintenance effectiveness and achieve organizational goals.
What Is The Objective and Relationship of Maintenance and Reliability?
The objective of maintenance and reliability is to ensure that equipment, machinery, and systems operate efficiently and reliably to support business operations while keeping the system/machines updated. Maintenance focuses on preserving assets through preventive and corrective measures, while reliability aims to optimize asset performance and minimize failures.
The relationship between maintenance and reliability is symbiotic: effective maintenance practices contribute to improved reliability by preventing breakdowns and extending asset lifespan, while reliability principles guide maintenance strategies to enhance asset performance and minimize downtime. Together, maintenance and reliability work towards achieving operational excellence, cost reduction, and increased productivity for organizations across various industries.
In conclusion, mastering the field of maintenance and reliability is crucial for ensuring the efficient operation and longevity of equipment, machinery, and systems in various industries. By implementing effective maintenance strategies and reliability principles, organizations can minimize downtime, reduce costs, and maximize productivity.
PetroSync offers comprehensive maintenance and reliability training programs designed to equip you with the knowledge and skills needed to excel in this critical field. Topics covered include:
- ISO 55000 Asset Management Training
- Root Cause Analysis Training
- Applied Reliability Centered Maintenance Training
- Certified Maintenance and Reliability Professional – CMRP Training
- Certified Reliability Engineer – CRE Training
- Maintenance Planning and Scheduling Training
Most of the topics covered discuss preventive maintenance strategies, asset management techniques, reliability engineering principles, and advanced maintenance technologies. By attending PetroSync‘s training sessions, you can gain valuable insights, learn best practices, and network with industry experts to enhance your expertise in maintenance and reliability.
As you strive for excellence in maintenance and reliability, I encourage you to explore PetroSync’s training programs to discover the wealth of knowledge and opportunities available. Visit our website to learn more about upcoming training sessions and take your skills to the next level in maintenance and reliability management.
Credit: Vecteezy
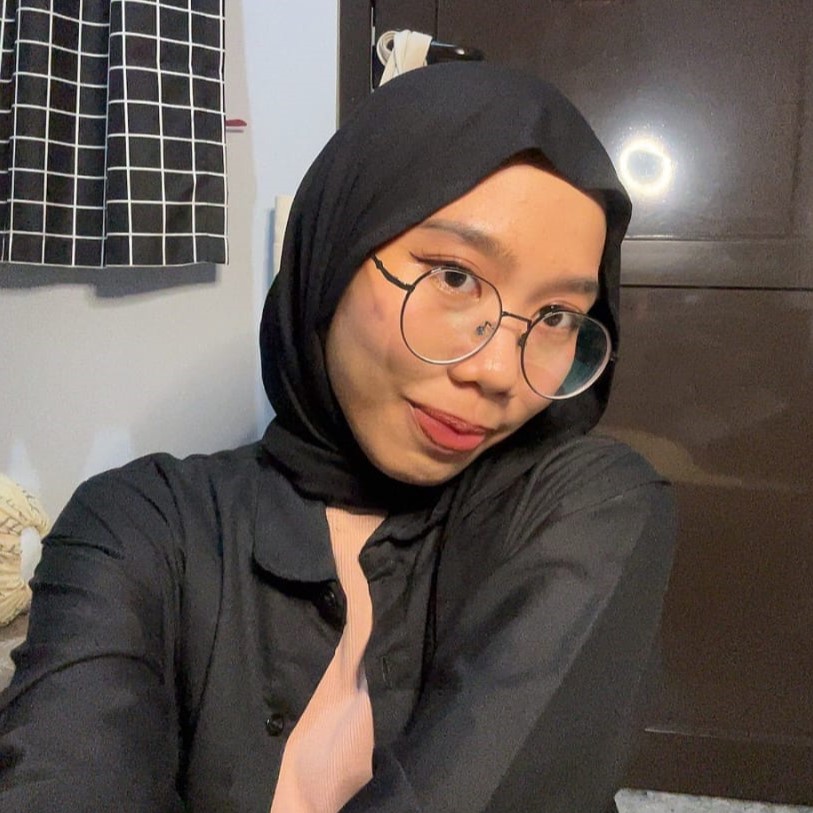
SEO specialist by day, fact-checker by night. An avid reader and content writer dedicated to delivering accurate and engaging articles through research and credible sources.