In industrial settings, the prevention and mitigation of leaks play a crucial role in ensuring safety, environmental compliance, and operational efficiency. Leak Detection and Repair (LDAR) programs are fundamental components of this effort, providing systematic approaches to identify and address potential leaks in equipment and facilities. As industries strive to uphold stringent regulatory standards and minimize their environmental footprint, the significance of LDAR in safeguarding against leaks cannot be diminished.
What Is Leak Detection?
Leak detection refers to a method used to detect the leak of materials from a pipeline and alert operators to these leak incidents by identifying and locating unwanted or unintended leaks in systems or structures. It involves using various techniques and tools to detect the presence of leaks, such as visual inspections, pressure testing, and specialized sensors. By detecting leaks early, it helps prevent potential damage, conserve resources, and maintain the safety and integrity of the system or structure.
Leak detection is crucial for ensuring the safe operation of pipelines and other systems. As per EPA estimates, the implementation of a facility Leak Detection and Repair (LDAR) program could lead to a significant reduction in emissions from equipment leaks. Specifically, petroleum refineries may achieve a 63% reduction in emissions, while chemical facilities could see a reduction of up to 56% in volatile organic compound (VOC) emissions through the adoption of such a program. (cited from EPA)
By promptly identifying and locating leaks, operators can take swift action to mitigate potential hazards and prevent environmental damage. Various methods, including visual inspections and advanced sensor technologies, are employed to detect leaks accurately. Timely detection enables operators to maintain the integrity of the infrastructure, protect valuable resources, and uphold safety standards.
What Are Some Examples of Leaks?
In the industrial process, there are several types of leaks worth noticing and resolved, such as:
1. Water Leaks
These occur when pipes, valves, or fittings carrying water develop cracks or corrode over time. Water leaks can lead to equipment damage, structural issues, and water wastage, impacting the efficiency and safety of industrial operations.
2. Gas Leaks
Gas leaks can arise from pipelines, storage tanks, or equipment such as valves and fittings. They pose a significant safety hazard as certain gases, such as methane or hydrogen sulfide, can be flammable, toxic, or asphyxiating. Prompt detection and repair are essential to prevent accidents and protect workers’ health.
3. Air Leaks
Air leaks commonly occur in compressed air systems due to faulty seals, fittings, or connections. These leaks waste energy and reduce the efficiency of pneumatic equipment. Regular inspections and maintenance are necessary to identify and address air leaks, ensuring optimal performance and cost savings.
4. Electricity Leaks
Electricity leaks, often referred to as electrical faults or shorts, occur when current flows through unintended paths due to damaged insulation or faulty wiring. These leaks can result in equipment malfunction, electrical fires, or even electrocution hazards. Proper electrical maintenance and insulation testing are crucial to prevent such incidents.
5. Oil and gas Leaks
Oil and gas leaks can occur in pipelines, valves, or storage tanks, posing environmental risks and potential safety hazards. These leaks may lead to soil or water contamination, fires, or explosions if not promptly addressed. Stringent monitoring and maintenance protocols are essential to prevent oil and gas leaks and mitigate their consequences.
6. Chemical Leaks
Chemical leaks can occur in industrial settings where various chemicals are stored, processed, or transported. These leaks can result from equipment failure, human error, or chemical reactions. Depending on the type of chemical involved, leaks can pose serious health risks, environmental damage, and regulatory non-compliance. Proper handling, storage, and monitoring are essential to prevent chemical leaks and ensure workplace safety.
7. Radioactive/Nuclear Waste Leaks
In facilities dealing with radioactive materials or nuclear waste, leaks can have severe consequences for human health and the environment. These leaks may occur in storage containers, processing equipment, or disposal sites due to corrosion, structural degradation, or accidents. Rigorous safety protocols, monitoring systems, and containment measures are necessary to prevent radioactive leaks and minimize their impact.
Overall, addressing and mitigating various types of leaks require proactive maintenance, robust monitoring systems, and adherence to strict safety and environmental regulations in industrial settings.
What Equipment Types Commonly Become The Source of Leaks?
When coming to leaks detection, these equipment must be checked first as they become the main source of leaks:
1. Pump
Pumps, which are crucial for moving fluids within industrial processes, often encounter leaks at their seals.
2. Valves
Valves, utilized to control the flow of fluids, commonly develop leaks around the stem or gland area, typically due to issues with valve packing or O-rings.
3. Connectors
Connectors such as flanges and fittings, used to join pipes and equipment, may experience leaks caused by gasket failure or improperly tightened bolts on flanges.
4. Sampling Connections
Sampling connections, essential for obtaining process samples, may develop leaks at the outlet of the sampling valve during purging.
5. Compressors
Compressors, responsible for increasing fluid pressure, are prone to leaks, primarily at their seals.
6. Pressure Relief Devices
Pressure relief valves and rupture disks, vital for maintaining safe pressure levels, may experience leaks if not seated properly, operating too close to their set points, or if seals are worn or damaged.
7. Open-Ended Lines
Open-ended lines, which are pipes or hoses exposed to the atmosphere, can develop leaks at points where the line is open, typically managed using caps, plugs, or flanges. Leakage can also occur due to incorrect implementation of block and bleed procedures.
What Is a Leak Detection and Repair (LDAR) Program?
A Leak Detection and Repair (LDAR) program is a systematic approach implemented by industries to identify and address leaks in their equipment and facilities. The program involves regular inspections using specialized tools and techniques to detect emissions of gasses or vapors that may indicate leaks.
How Are The Procedures of Doing LDAR Program?
1. Identifying Components
Identifying components involves determining which equipment and parts are subject to the Leak Detection and Repair (LDAR) program.
Common Problems |
Best Practices |
– Not properly identifying all regulated equipment components. | – Physically tag each regulated equipment component with a unique ID number. |
– Not properly documenting exempt components (e.g., <300 hour exemption and <5 (or <10) weight % HAP). | – Write the component ID number on piping and instrumentation diagrams. |
– Institute an electronic data management system for LDAR data and records, possibly including the use of bar coding equipment. | |
– Periodically perform a field audit to ensure lists and diagrams accurately represent equipment installed in the plant. |
Ensuring accurate identification of components is essential for effective LDAR implementation, preventing oversight of regulated equipment and exempt components.
By physically tagging each regulated component with a unique ID number and maintaining comprehensive documentation, such as piping and instrumentation diagrams, companies can enhance their LDAR program’s efficiency and compliance. Implementing electronic data management systems and conducting periodic field audits further contribute to the accuracy and reliability of LDAR records.
2. Leak Definition
Leak Definition entails understanding what constitutes a leak within the context of a LDAR program. It involves defining thresholds for emissions that indicate a leak and establishing criteria for identifying and addressing them. Below is a breakdown of common problems encountered in defining leaks and best practices to mitigate them:
Common Problems |
Best Practices |
Using the wrong leak definition for a particular component due to confusion at facilities where multiple LDAR regulations apply. | Utilize a leak definition lower than what the regulation requires. |
Simplify the program by using the lowest leak definition when multiple leak definitions exist. | |
Make the lowest leak definition conservative to provide a margin of safety when monitoring components. | |
Keep the lowest leak definition consistent among all similar component types. For example, all valves in a facility might have a leak definition of 500 ppm. |
Adhering to these best practices ensures clarity and consistency in identifying and addressing leaks within the LDAR program, ultimately enhancing its effectiveness in emissions reduction and regulatory compliance.
3. Monitoring Components
Monitoring components involves systematically inspecting equipment and facilities to detect and address leaks. Here are common problems and best practices associated with this procedure:
Common Problems |
Best Practices |
– Not following Method 21 properly. | – Utilize an automatic (electronic) data logger, though not required, to save time and enhance accuracy. |
– Failing to monitor at the maximum leak location. | – Audit the LDAR program to ensure correct equipment monitoring and proper Method 21 procedures and record-keeping. |
– Not monitoring long enough to identify a leak. | – Monitor components more frequently than mandated. |
– Holding the detection probe too far from the component interface. | – Implement QA/QC of LDAR data for accuracy and consistency. |
– Not monitoring all potential leak interfaces. | – Remove obstructions hindering monitoring at the interface, such as grease. |
– Using incorrect or expired calibration gas. | – Periodically use Method 21 even if alternatives are permitted. |
– Not monitoring all regulated components. | |
– Not completing monitoring if the first attempt fails due to temporary equipment unavailability. |
These best practices aim to enhance the effectiveness and reliability of LDAR programs, ensuring compliance with regulations and minimizing emissions.
4. Repairing Components
Repairing components in the context of LDAR involves addressing leaks detected in equipment and ensuring compliance with regulatory requirements.
Common Problems |
Best Practices |
– Not repairing leaking equipment within specified timeframes | – Develop a repair plan with clear timelines |
– Improperly placing components on Delay of Repair list | – Initiate repair promptly after leak detection |
– Lack of justifiable reasons for delayed repairs | – Monitor components consistently for successful repairs |
– Failure to explore repair alternatives before delaying repairs | – Consider replacement with “leakless” or alternative technologies |
These practices aim to efficiently address leaks, prevent regulatory violations, and promote environmental responsibility within LDAR programs.
5. Recordkeeping
Recordkeeping involves the systematic documentation and storage of information related to Leak Detection and Repair (LDAR) activities. It includes maintaining detailed and accurate records as required by applicable regulations, updating records to reflect changes in regulations or process modifications, and ensuring compliance with regulatory requirements.
Common Problems |
Best Practices |
– Not keeping detailed and accurate records | – Perform internal and third-party audits of LDAR records on a regular basis |
required by regulations. | – Electronically monitor and store LDAR data including regular QA/QC audits |
– Not updating records to designate new components | – Perform regular records maintenance |
subject to LDAR due to revised regulations | – Continually search for and update regulatory requirements |
or process modifications. | – Properly record and report first attempts at repair |
– Keep the proper records for components on Delay of Repair lists |
These practices help ensure that LDAR records are up-to-date, accurate, and in compliance with regulatory standards. Regular audits, electronic monitoring, and proactive maintenance are essential components of effective recordkeeping in LDAR programs.
What Are The Benefits of Doing Leak Detection & Repair (LDAR)?
Implementing Leak Detection and Repair (LDAR) programs offers several benefits for industrial facilities. Firstly, LDAR helps to prevent environmental pollution by identifying and repairing leaks promptly, thereby reducing emissions of harmful substances into the atmosphere. This not only ensures compliance with environmental regulations but also demonstrates a commitment to sustainable practices and corporate responsibility. Additionally, LDAR programs contribute to cost savings by minimizing product loss, conserving resources, and improving operational efficiency.
However, if LDAR is not conducted properly or neglected altogether, several negative consequences may arise. Without effective leak detection and repair measures in place, leaks can escalate over time, leading to increased emissions, environmental contamination, and health hazards for workers and surrounding communities.
Failure to comply with regulatory requirements may result in penalties, legal consequences, and damage to the company’s reputation. Moreover, untreated leaks can compromise the integrity and reliability of industrial equipment, leading to operational disruptions, costly repairs, and decreased productivity. Overall, neglecting LDAR can undermine both environmental stewardship and financial sustainability, highlighting the importance of implementing robust leak detection and repair practices in industrial operations.
Inspector engineers, as key personnel in these industries, play a pivotal role in implementing and overseeing LDAR programs. Their job description often includes conducting regular inspections, monitoring equipment integrity, and ensuring compliance with safety and environmental regulations. By diligently performing their duties, inspector engineers contribute to the effectiveness of LDAR programs, thereby safeguarding the environment, protecting public health, and minimizing operational risks.
In essence, the adoption of LDAR programs in high-risk industries not only enhances environmental stewardship and regulatory compliance but also supports the overarching goal of ensuring safe and sustainable industrial operations. Inspector engineers, through their expertise and diligence, play a crucial part in achieving these objectives and upholding the highest standards of safety and environmental responsibility.
PetroSync offers comprehensive API training programs tailored to the specific needs and focus areas of engineers working with different types of equipment in the oil and gas industry. Depending on your specialization and the equipment you handle, PetroSync provides the following API training courses:
- API 510 Training: This course is designed for engineers involved in pressure vessel inspection, maintenance, and repair. It covers the requirements of the API 510 Pressure Vessel Inspection Code.
- API 560 Training: Engineers working with fired heaters and boilers can benefit from this training, which focuses on the specifications outlined in API Standard 560 for the design and operation of such equipment.
- API 570 Training: For engineers responsible for piping systems in refineries, chemical plants, and other facilities, this training covers the API 570 Piping Inspection Code requirements for inspection, repair, alteration, and rerating of in-service piping systems.
- API 571 Training: This course is ideal for engineers seeking to enhance their understanding of damage mechanisms in refining and chemical processing equipment, as outlined in API 571 Damage Mechanisms Affecting Fixed Equipment in the Refining Industry.
- API 580 & 581 Training: Engineers involved in risk-based inspection (RBI) processes will benefit from this training, which covers the principles and practices outlined in API 580 Risk-Based Inspection and API 581 Base Resource Document.
- API 653 Training: Engineers responsible for aboveground storage tanks (ASTs) will find this training valuable, as it covers the requirements of the API 653 Tank Inspection, Repair, Alteration, and Reconstruction standard.
By attending PetroSync‘s API training courses, engineers can deepen their knowledge, enhance their skills, and stay updated with the latest industry standards and best practices relevant to their equipment focus areas. These courses are delivered by industry experts and provide practical insights to help engineers excel in their roles and contribute effectively to their organizations’ success.
Credit header image: Freepik
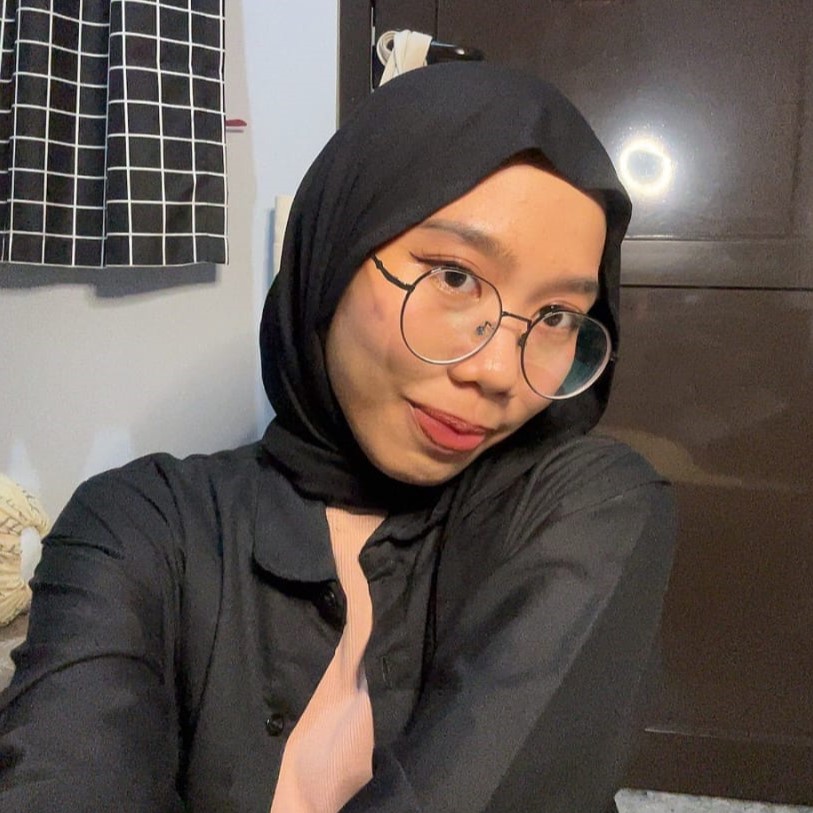
SEO specialist by day, fact-checker by night. An avid reader and content writer dedicated to delivering accurate and engaging articles through research and credible sources.