Ensuring safe and reliable operation of critical equipment is vital in today’s industries. Fitness-for-Service (FFS) assessments mitigate risks by evaluating equipment integrity and fitness throughout its lifespan. With industry standards and best practices, FFS assessments inform decisions on maintenance, repairs, and equipment life extension. This article explores FFS significance, applications, and benefits for equipment reliability, safety, and operational efficiency.
What Is Fitness For Service?
Fitness-for-Service (FFS) is a thorough evaluation conducted according to industry standards to assess the structural integrity of an asset/component. Its purpose is to determine if the asset/component is suitable for continued use, given its current state and any detected flaws, damage, or degradation.
The FFS assessment is typically carried out on components like pipelines, pressure vessels, storage tanks, and other crucial industrial equipment that are already in use. Its purpose is to ensure that these components can continue to function safely and reliably, without compromising the overall integrity of the system.
During the FFS evaluation, several factors are considered, including material properties, structural design, operational conditions, and any identified defects or damage. This assessment involves visual inspections, non-destructive testing, analysis of structural and mechanical properties, and adherence to relevant codes and standards.
What Is The API Standard for FFS?
The API 579-1/ASME FFS-1-2021 standard offers a comprehensive range of assessment methods for fitness-for-service evaluations, catering to various equipment conditions and requirements.
By following API 579, engineers and inspectors can conduct thorough FFS assessments. The standard provides assessment procedures, inspection techniques, data analysis methods, and calculations to determine the remaining strength and life of the equipment.
What Are The Types of Flaws and Damage in Fitness For Service?
API 579-1/ASME FFS-1 is divided into several parts describing how to assess various flaws or damage. These are:
- Brittle fracture
- General metal loss
- Local metal loss
- Pitting corrosion
- Hydrogen blisters and hydrogen damage
- Weld misalignment and shell distortions
- Crack-like flaws
- Operation in creep range
- Fire damage
- Dents, gouges, and dent-gouge combinations
- Laminations
How To Do Fitness For Service Assessment?
API 579-1/FFS-1 provides comprehensive guidance on conducting Level 1, Level 2, and Level 3 Assessments. While discussing each part and its specific requirements is beyond the scope here, the procedures for assessing various types of flaws and damage are generally similar. Let’s outline the general procedure below:
Identification of flaw and damage mechanism
1. Determination of Applicability and Limitations of FFS Assessment Procedures
The first step in API 579 involves assessing if the assessment procedures are suitable for the equipment/component being evaluated. This step considers factors like design, damage identification, procedure alignment, and limitations, ensuring accurate and reliable fitness for service evaluations.
2. Gathering of Information
The second step involves collecting relevant data and details about the equipment or component being assessed. This includes information about its design, materials, operating conditions, and any historical performance records. This step ensures a comprehensive understanding of the equipment, enabling a thorough fitness for service evaluation.
3. Assessment Technique and Acceptance Criteria
In assessment technique and acceptance criteria, the inspectors must select methods and criteria to evaluate fitness for service. It ensures a systematic and reliable process to determine if equipment meets the required standards for safe operation.
4. Remaining Life Assessment
Remaining Life Assessment involves estimating the remaining useful lifespan of equipment or components. This assessment considers factors like material properties, operating conditions, and identified damage or degradation.
5. Remediation
Remediation in API 579 assessment refers to taking necessary actions based on assessment results to address issues and ensure equipment fitness. It includes repairs, maintenance, and mitigation measures to enhance structural integrity, prevent failures, and ensure safe operation.
6. In-service Monitoring
In-service Monitoring involves ongoing surveillance of equipment during operation. It includes regular inspections and data analysis to detect changes or deterioration. This helps ensure safe and reliable operation by allowing timely maintenance or further assessments based on API 579 guidelines.
7. Documentation
The last step involves maintaining records of the assessment process. It includes inspection results, analysis findings, and decisions made. Documentation ensures traceability and supports future reference and decision-making based on API 579 guidelines.
What Are The Benefits of Fitness-for-Service?
Advantages of Fitness-for-Service (FFS) Assessment Fitness-for-Service assessment offers advantages that extend beyond the asset’s operating stage and can be applied throughout its life cycle, including design and fabrication. The key benefits provided by FFS are:
1. Increased Asset Operating Life
FFS is applicable in plant life management, enabling the extension of the asset’s operating life through accurate assessment of its fitness for service.
2. Reduction in Unnecessary Repairs and Replacements
FFS assessment helps minimize the need for unnecessary repairs and replacements by identifying the true condition of the equipment, leading to cost savings and improved resource allocation.
3. Enhanced Plant Safety
By evaluating the structural integrity of the asset, FFS assessment contributes to improved plant safety by identifying potential risks and ensuring equipment meets safety standards.
4. Improved Asset Utilization
FFS assessment provides knowledge of the equipment’s residual life, allowing for optimized asset utilization and planning for future maintenance or replacement strategies.
5. Optimization of Maintenance and Inspection Plans
With prior knowledge from FFS assessment, maintenance and inspection plans can be optimized to maximize plant operating time and minimize downtime, resulting in increased efficiency and productivity.
6. Reduction in Capital Expenditure
FFS assessment aids in minimizing capital expenditure by enabling informed decisions regarding equipment repair, replacement, or refurbishment, resulting in cost-effective asset management.
Overall, Fitness-for-Service assessment offers significant advantages by extending the asset’s life, reducing unnecessary costs, improving safety, optimizing maintenance plans, and minimizing capital expenditure throughout the asset’s life cycle.
When is Fitness-for-Service Used?
Fitness-for-Service (FFS) is used in various situations across industries, including:
1. Inspection-Based Maintenance
FFS assessments are frequently used to inspect vital equipment, like pipelines and pressure vessels, to ensure their integrity. For instance, in the oil and gas industry, FFS assessments evaluate the fitness of aging pipelines for continued safe operation. These assessments confirm their ability to function properly without jeopardizing system integrity.
2. Post-Failure Analysis
After an equipment failure, FFS assessments are conducted to understand the root cause and determine the remaining fitness for service. For instance, in the power generation sector, if a turbine blade fails, an FFS assessment would be performed to examine the remaining life of the remaining blades and assess if they can continue operating safely or require repair/replacement.
3. Life Extension Studies
Following equipment failures, FFS assessments are conducted to identify the root cause and evaluate the remaining fitness for service. For example, in the power generation industry, if a turbine blade fails, an FFS assessment would analyze the remaining blades’ lifespan and assess their suitability for continued operation.
4. Plant Turnaround Maintenance
During plant turnaround maintenance, the equipment undergoes FFS assessments to assess its condition for safe reintegration into service. In the chemical industry, pressure vessels and storage tanks are subject to FFS assessments before being returned to operation.
These examples showcase the diverse application of FFS assessments across industries. They ensure the safe operation of vital equipment and enable informed decisions regarding maintenance, repairs, and life extension strategies.
What Are The International Engineering Standards and Practices That Apply FFS Approach?
The Fitness-for-Service (FFS) approach is supported by various international engineering standards and practices. Notable examples include:
1. API 570
Though API 570 does not strictly follow the FFS approach, it provides guidelines for inspecting, repairing, and maintaining piping systems, contributing to their integrity and safety. In PetroSync, we combine API 570 training with FFS principles to enable you to have comprehensive evaluations for informed fitness-for-service decisions.
2. ISO 16809
This international standard focuses on assessing damaged structures and components, offering methodologies and criteria to evaluate the fitness for service of different equipment types.
3. ASME B31G
Specifically addressing pipeline assessments, this ASME standard provides methodologies to evaluate the remaining strength of corroded pipelines and determine their fitness for continued operation.
4. API 579-1/ASME FFS-1
API 579 is a widely recognized standard, developed jointly by API and ASME, and provides comprehensive guidelines for FFS assessment methodologies and procedures.
These international standards and practices play a critical role in ensuring consistent and reliable evaluations of equipment’s fitness for service. They offer guidelines, methodologies, and acceptance criteria that assist engineers and inspectors in assessing structural integrity, remaining life, and safety across diverse industries.
If you are an engineer, it is vital to grasp the importance of understanding Fitness-for-Service (FFS) principles. FFS offers a framework to assess equipment integrity and fitness throughout its lifespan, ensuring safe and reliable operation.
The significance of Fitness For Service lies in its applicability across diverse engineering disciplines, including mechanical, structural, and materials engineering. By embracing FFS principles, you can make informed decisions on maintenance, repairs, and life extension strategies, ultimately improving equipment reliability and performance.
Hence, acquiring proficiency in FFS is essential for you to optimize operations, mitigate risks, and uphold the long-term safety and efficiency of industrial assets. Take your API 579 training and make the best decision to run, repair, or replace the following Fitness-for-Service standard with PetroSync!
Credit header image: Freepik
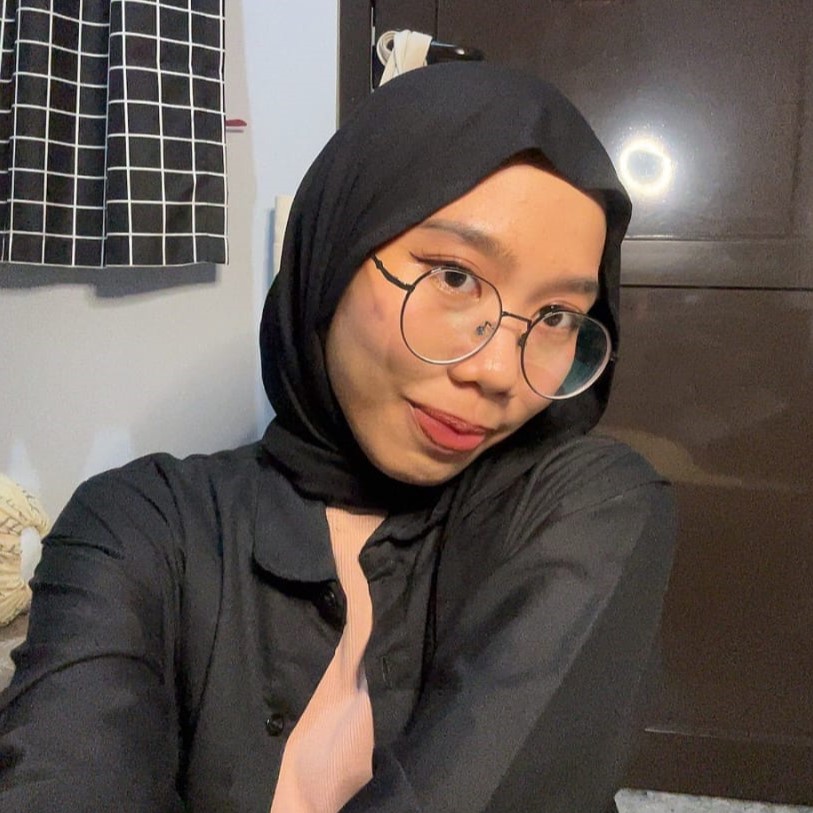
SEO specialist by day, fact-checker by night. An avid reader and content writer dedicated to delivering accurate and engaging articles through research and credible sources.