Fired heaters are used extensively in industries such as oil and gas, petrochemicals, and energy generation. They are used to heat process fluids, speed up chemical reactions, and perform a variety of other high-temperature functions. Fired heaters are critical components of process heating and necessitate a thorough understanding of safety, efficiency, and operating variability.
Training on fired heaters course fee provides considerable benefits to people looking to expand their experience and operational skills in the high-energy business. This article delves into the major characteristics of fired heaters, such as safety concerns, efficiency, classifications, and the advantages of specialist training.
Are Direct Fired Heaters Safe?
Safety is a primary consideration in any industry that uses high-temperature equipment, and direct fired heaters are no different. Direct fired heaters are generally safe when used correctly, but their operation entails inherent risks because fuel combustion occurs directly within the heater chamber.
To avoid overheating, combustion-related risks, and gas leaks, these heaters must adhere to strict safety regulations and undergo frequent inspections. Operators are taught to monitor and control oxygen levels, combustion airflow, and fuel supply to ensure safe and efficient operation.
Furthermore, safety measures such as flame detection sensors, emergency shutdown systems, and controlled ventilation can greatly improve safety. Proper training ensures that operators can respond quickly and efficiently to avoid or reduce possible hazards, making direct fired heaters a safe choice in well-regulated environments.
What is the Efficiency of a Fired Heater?
The efficiency of fired heaters course fee is a crucial factor in industries with high energy demands, as fuel consumption impacts both operating expenses and environmental outcomes. Efficiency is usually measured by assessing the amount of heat transferred to the process fluid relative to the total energy provided by the fuel.
Ideally, fired heaters attain 80-90% efficiency, however this might vary based on design, fuel type, and operating conditions. Heat loss from stack gases, partial combustion, and radiation all improve efficiency. Advanced design features, such as heat recovery systems, efficient burner designs, and insulation.
Can boost efficiency while cutting operating costs and emissions.Professionals that receive fired heater training understand how to maximize efficiency by improving combustion processes, monitoring fuel usage, and adhering to best maintenance practices.
What is the Difference Between Direct and Indirect Fired Heaters?
Direct and indirect fired heaters provide comparable heating tasks, although they differ significantly in design and functioning. Direct fired heaters bring combustion gases into direct contact with the material being heated, allowing for quick and efficient heating, which is excellent for high-capacity applications.
These heaters are often chosen for applications where there is minimal risk of the heated material becoming contaminated by combustion byproducts. In contrast, indirect fired heaters use a heat exchanger to transfer heat from combustion gases to the medium, eliminating the requirement for direct contact.
This arrangement is appropriate for applications requiring clean, uncontaminated heating, such as delicate chemical operations. Each heater type has advantages, and the choice is influenced by specific operational requirements, the need for thermal purity, and energy efficiency issues.
What are the Classifications of Fired Heaters?
Fired heaters are classified based on a variety of factors, including configuration, fuel type, and heating mechanism. Some common classifications are:
Box Heaters: Enclosed constructions in which combustion happens in a rectangular box, resulting in a high heat concentration.
Cylindrical Heaters: These heaters have a circular structure and are often used for applications requiring consistent radial heating.
Direct Fired Heaters: Heat is directly applied to the process fluid, with combustion gases coming into direct contact with the fluid.
Indirect Fired Heaters: Heat is supplied through a media that separates combustion gasses from the fluid being heated.
Fuel-Based Classifications: Fired heaters can also be categorized based on the type of fuel they use, including gas-fired, oil-fired, or dual-fired systems, each offering different levels of efficiency and associated costs.
Understanding these classes aids in the selection of the appropriate heater for certain applications while balancing cost, efficiency, and operating needs. Training courses delve into these classifications, providing participants with understanding of heater selection, customization, and maintenance procedures for a variety of industrial environments.
What is the Temperature of a Fired Heater?
Fired heaters typically operate at temperatures ranging from 500°C to 1,500°C (932°F to 2,732°F), depending on the application and design criteria. The specific temperature is determined by factors such as heater type, fuel source, and process requirements. In high-temperature applications such as petrochemical cracking or crude oil refining.
Fired heaters course fee at the upper end of this range are frequently used. Maintaining the proper temperature is crucial for optimizing chemical reactions and lowering system stress. Temperature regulation involves regular monitoring and fine-tuning since high temperatures can cause system damage or constitute a safety risk.
Trained operators understand how to correctly regulate these important parameters, ensuring that operations are both efficient and secure.
Gain Expert Knowledge with PetroSync’s Fired Heaters Training
Professionals in the oil, gas, and energy sectors can benefit greatly from specialized training programs like those offered by PetroSync. PetroSync’s fired heater training courses cover fundamental and advanced aspects of fired heater operation, from design and safety protocols to efficiency optimization and troubleshooting techniques.
Professionals that participate in a fired heater training program increase their technical knowledge and operational skills, resulting in safer and more efficient practices in their fields. This knowledge is particularly valuable for engineers, plant operators, and maintenance personnel seeking to develop their careers in the energy industry.
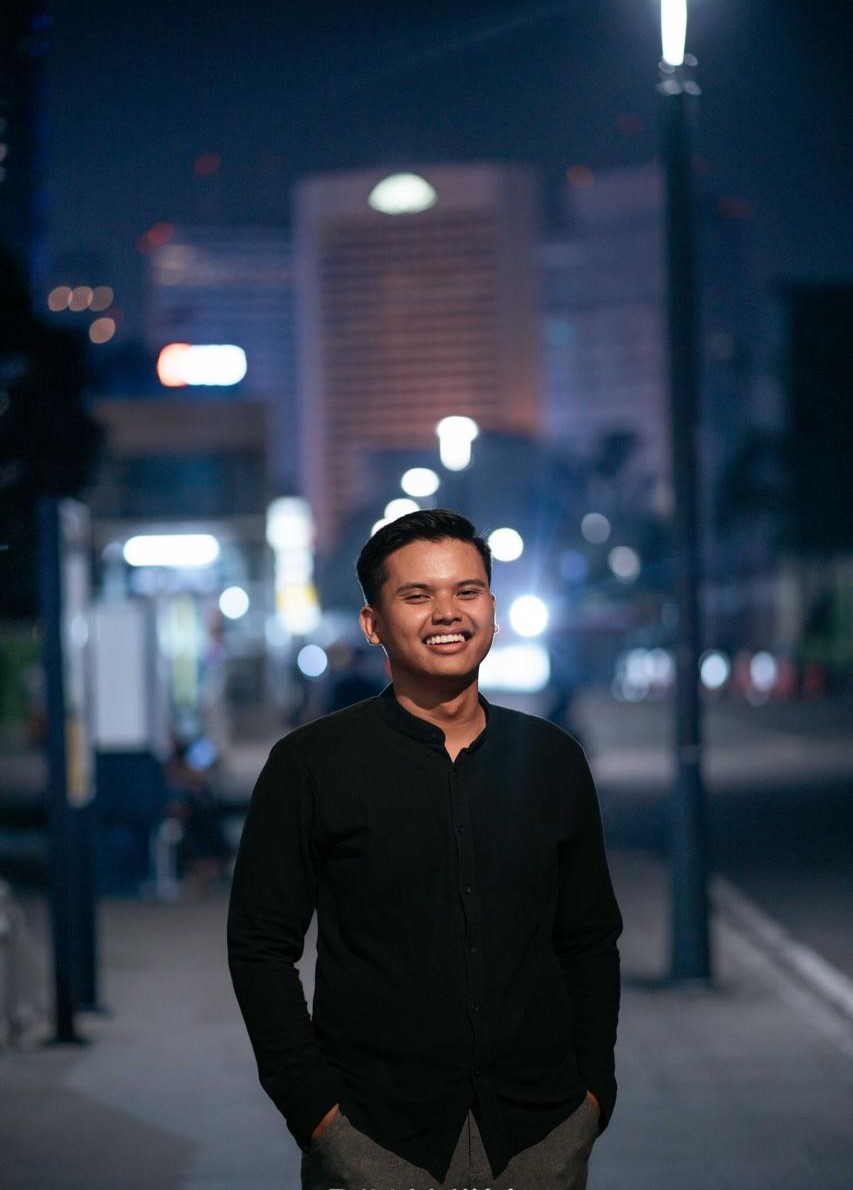
Results-oriented and thorough SEO specialist with extensive experience in conducting keyword research, developing and implementing digital website promotion strategies and plans, managing campaigns to develop company websites in the digital world, excellent knowledge of marketing techniques and principles, and attentive strong attention to detail.