Coiled tubing has become a popular technology in the petroleum industry. It can be used for a variety of tasks in oil and gas operations, such as drilling and well intervention. Compared to traditional methods, coiled tubing is cost-effective and versatile, making it become a preferable technique in upstream activity. Coiled tubing is widely used due to its ability to reach inaccessible areas in wells.
What Is Coiled Tubing?
In the petroleum industry, coiled tubing is a continuous metal pipe with no joints ranging from 1 to 3.25 inches (25 to 83 mm) in diameter conveniently supplied spooled on a large reel. This coiled tubing serves multiple purposes, including interventions in oil and gas wells and production tubing in depleted gas wells.
What Is Coiled Tubing Operation?
In the oil and gas sector, coiled tubing operation is a technique used for well intervention without using traditional drill pipes. It employs a continuous coil of tubing, typically made of steel or composite material, wound onto a large spool and then inserted into the wellbore. This method allows for various tasks to be performed in the wellbore efficiently. Coil tubing is sometimes needed when the well completion and workover are performed.
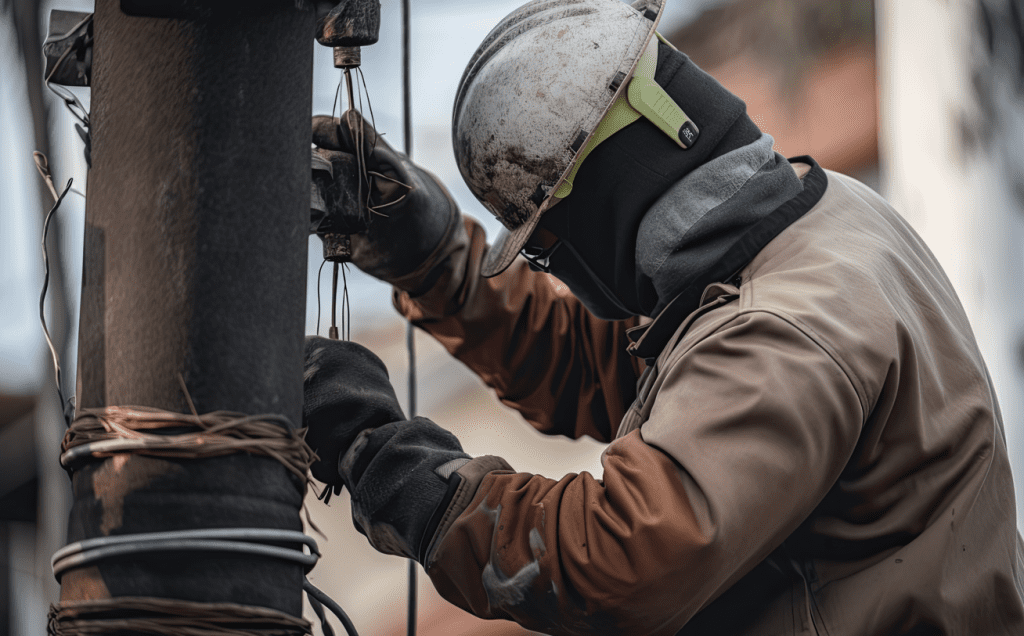
Coiled tubing operations can be used for a wide range of tasks, including well cleanouts, acid stimulation, fracturing, cementing, logging, plug setting or retrieval, and stuck pipe prevention. The coiled tubing is typically deployed into the wellbore through a specialized injector head, which controls the speed and tension of the tubing as it is fed into the well. Once the desired depth is reached, various tools and equipment can be run through the coiled tubing to perform the required tasks.
What Are The Application of Coiled Tubing?
Since coiled tubing is a versatile tool that finds numerous applications in the oil and gas industry, there are diverse applications of coiled tubing that help the drilling procedure to be done easier. Circulating, pumping, coiled tubing drilling, production, logging and perforating commonly apply coiled tubing.
1. Circulation
Coiled tubing is a beneficial tool for circulation in well interventions due to its continuous length ability to navigate complex wellbores. In some cases, the flow of formation fluids in a well may be impeded by the weight of a hydrostatic head. To restore the flow, coiled tubing can be inserted into the wellbore allowing production to resume.
2. Pumping
Another common application of coiled tubing is for pumping operations in oil and gas wells to deliver various fluids and treatments. It is employed in applications such as hydraulic fracturing, well stimulation, cementing, acidizing, and nitrogen purging.
To initiate pumping, the coiled tubing is connected to a surface pumping unit or a dedicated pumping system. Fluids are then pumped down the coiled tubing string, which is inserted into the well. The continuous length of coiled tubing enables uninterrupted pumping, ensuring a consistent and controlled flow rate.
3. Coiled Tubing Drilling
As the name conveys, coiled tubing can be employed for Coiled Tubing Drilling (CTD) operations that involve utilizing a coiled tubing string as a drill pipe to carry out drilling tasks in oil and gas wells.
In Coiled Tubing Drilling, the coiled tubing is inserted into the well and equipped with a bottom hole assembly that comprises a drill bit. The coiled tubing is then rotated and pushed into the rock formation, enabling the drill bit to cut through the rock and establish a wellbore.
4. Logging and Perforating
Coiled tubing is specifically employed in logging operations to lower specialized tools and instruments into the wellbore, enabling the collection of data for evaluating subsurface formations.
These tools, including logging tools and sensors, are connected to the coiled tubing string and utilized to measure formation pressure, temperature, fluid composition, and rock properties. The acquired data aids in assessing reservoir characteristics and making informed decisions regarding production strategies.
5. Production
Coiled tubing can be employed in production operations to support a range of activities to maximize well productivity. One prevalent application involves well stimulation, where fluids, chemicals, or proppants are injected through the coiled tubing string into the well. This process enhances the performance of the reservoir, leading to an increase in hydrocarbon production.
What Are The Physical Characteristics of Coiled Tubing Equipment?
Considered as flexible yet durable, coiled tubing has several physical characteristics.
1. Self Contained
Coiled tubing is labeled as self-contained because it contains all the essential components and equipment within the tubing, enabling it to operate autonomously without relying on external assistance or additional equipment.
2. Mobile/Modular
Coiled tubing is mobile and modular due to its design which facilitates convenient transportation and assembly. Its modular construction allows for easy setup and dismantling, enabling it to move and deploy in different locations as required.
3. Hydraulically Powered
Coiled tubing is hydraulically powered, utilizing hydraulic pressure for efficient operation. It enables tasks such as fluid pumping, circulation, and tool manipulation, ensuring effective performance in various applications.
4. Environmentally Friendly
Coil tubing is recognized for its environmental friendliness as it contributes to minimizing ecological impacts. By reducing the requirement for extensive equipment and infrastructure, coiled tubing helps decrease emissions and disturbances to surrounding ecosystems.
What Are The Components of Coiled Tubing Equipment?
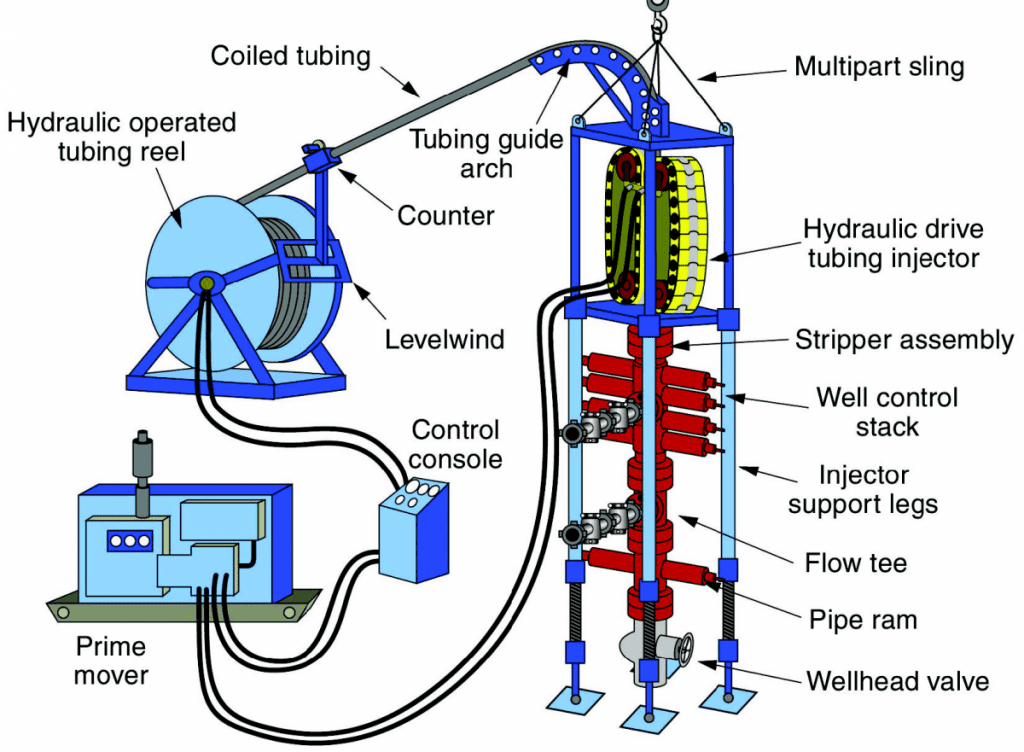
Ever since it was officially developed in late 1960, coiled tubing has become a crucial piece of equipment in the oil and gas industry for well-intervention purposes. It comes in various designs and types available in the market, but the components of a coiled tubing unit are generally similar. Here are the basic components of Coiled Tubing Units:
1. Injector and Tubing Guide Arch
The coiled tubing injector is a device that grasps and exerts the necessary force to deploy and retrieve the continuous tubing in and out of the wellbore.
2. Service Reel with CT
The coiled tubing injector is a device that grasps and exerts the necessary force to deploy and retrieve the continuous tubing in and out of the wellbore. It is an essential component of the equipment used.
3. Power Supply or Prime Mover
Most prime mover packages in coiled tubing units are powered by diesel engines and multistage hydraulic pumps with pressure ratings ranging from 3,000 to 5,000 psig. This is the general configuration of prime mover packages used in such units.
4. Control Console and Monitoring Equipment
The console contains the necessary controls and gauges to operate and monitor the components of the coiled tubing unit, including the red and injector heads, and the control system for regulating the drive chain, stripper rubber, and blowout preventers.
5. Downhole CT Connectors and Bottom Hole Assembly (BHA) Components
In coiled tubing (CT) services, various connections isolate pressure and transfer tension, compression, and torsional loads from tools and bottom hole assemblies to the tube.
6. Well-control Stack Equipment
The well-control stack system plays a crucial role in the pressure containment package of a coiled tubing (CT) unit, consisting of a stripper assembly and hydraulically operated rams.
How Does Coiled Tubing Work?
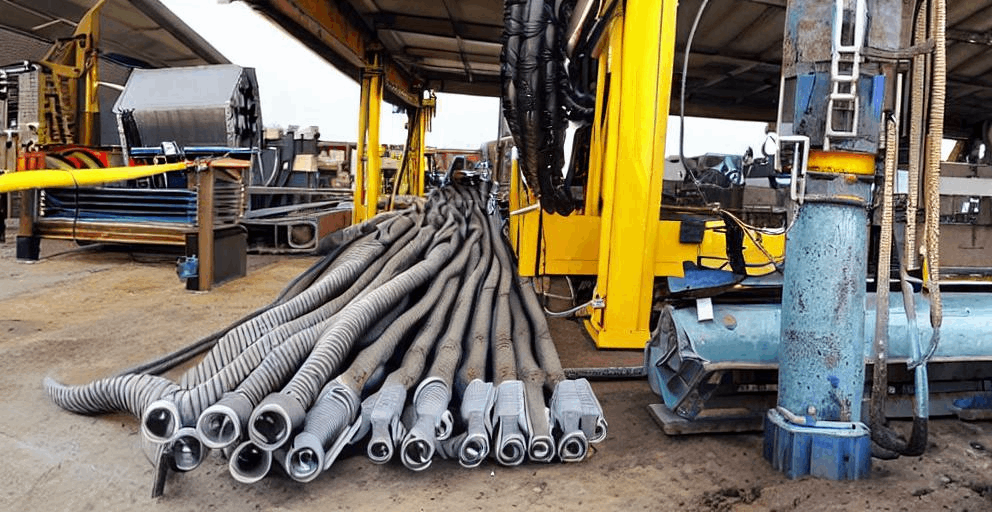
First, a coiled tubing unit (CTU) central to CT surface operations consists of a reel that holds a continuous length of flexible steel pipe. After that, the tubing is deployed downhole by spooling it off the reel and guiding it through a gooseneck, which directs the CT downward to an injector head. It becomes straight before it enters the borehole.
Right after the end of the operation, the flexible tubing is taken out of the well and spooled back onto the reel using a high-pressure swivel joint on the reel hub that allows for the pumping of fluids while the reel rotates. Throughout the process, the CT operator controls the movement and depth of the CT string from the CTU control cabin using a hydraulically driven injector head.
It is important to note that a dynamic seal around the tubing string is provided by a stripper assembly beneath the injector head, which is crucial for running the CT in and out of live wells. A secondary and backup pressure-control system is provided by a blowout preventer assembly positioned between the stripper and wellhead.
The CTU control cabin oversees and coordinates the entire process of managing the deployment and retrieval of flexible tubing during CT surface operations, making it a crucial component in the overall process.
What Are The Disadvantages of Coiled Tubing?
One disadvantage of CT is its inability to rotate. This means you can not turn the pipe, which limits its flexibility and capability in certain operations.
Another disadvantage is the risk of fatigue and wear on the tubing due to repeated bending and straightening during use. Over time, this can weaken the tubing and increase the likelihood of failure, leading to potential safety hazards and increased maintenance costs.
What Are The Advantages of Using Coiled Tubing?
Utilizing coiled tubing provides numerous benefits across different industries and applications. Here are some of the key advantages of using coiled tubing:
1. Versatility
Coiled tubing is highly adaptable and can be utilized for various operations such as well intervention, stimulation, cleanouts, logging, and production enhancement. Its flexible nature allows it to navigate complex wellbore configurations efficiently.
2. Cost-Effectiveness
Coiled tubing operations often require smaller crews and equipment since killing well is unnecessary, leading to cost reductions. It enables faster deployment, minimizing the need for time-consuming rigging-up processes and enhancing overall operational efficiency.
3. Time Savings
Coiled tubing operations are generally faster compared to traditional methods as there is no need for frequent trips in and out of the wellbore. This enables swift mobilization, increases well productivity, and reduces downtime.
4. Enhanced Well Control
The continuous length of coiled tubing minimizes the risk of connection failures, ensuring better well control during operations. Real-time monitoring and control capabilities allow for immediate response to well conditions.
What Are Some FAQs Regarding Coiled Tubing?
Frequently asked questions regarding coil tubing revolve around the size and the components of the tools itself.
1. What Are The Unit Sizes of Coil Tubing?
The unit sizes of coiled tubing are measured by their outside diameter (OD). These sizes vary from 0.750 inches (19.1 mm) to 5.00 inches (127 mm). Additionally, the wall thicknesses of coiled tubing range from 0.087 inches (2.00 mm) to 0.337 inches (8.60 mm).
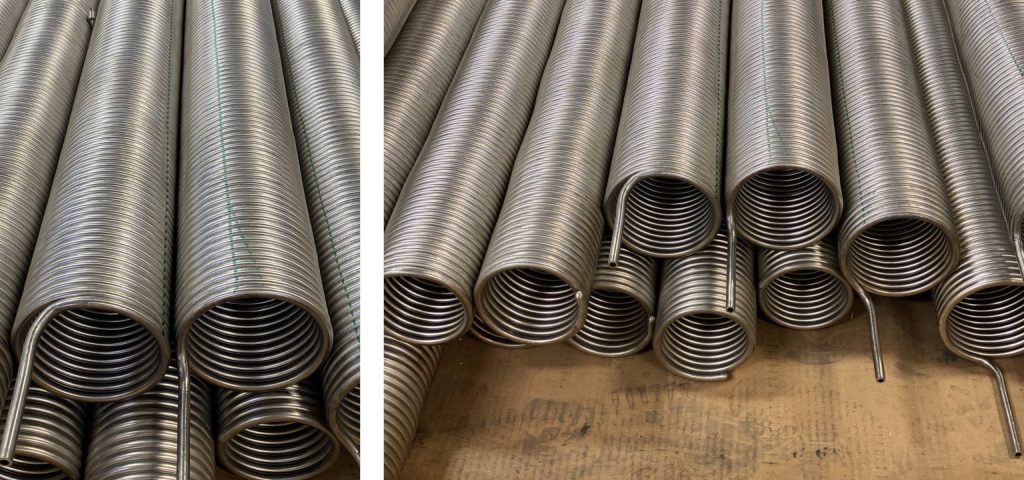
2. What Is The Length of Coiled Tubing?
The length of coiled tubing can vary depending on the diameter of the pipe, which ranges from 1 inch to 4-1/2 inches, and the size of the spool. Typically, coiled tubing can range from 2,000 feet to 15,000 feet or even longer, which is approximately 610 to 4,570 meters. For further information, you can refer to “The Defining Series: Introduction to Coiled Tubing.”
Coiled tubing is a complex process with strict regulations and standards that must be followed during operation. If you want to know more about coiled tubing operations, you should consider undergoing proper training to enhance your skills and expertise in this specialized field.
Our Coiled Tubing Operation training course provides an introductory overview of coiled tubing operations in oil fields, including its concept and applications. PetroSync crafts a thorough outline covering various coiled tubing technologies, focusing on surface equipment and downhole tools. It also addresses the main components, application envelope, special coiled tubing applications, and contingency planning for different operational situations.
PetroSync aims to enhance your understanding, knowledge, and decision-making abilities related to wellbore treatments for well performance improvement through presentations, case studies, group discussions, exercises, and practical videos of real-world cases. Join us and gain a comprehensive understanding of coiled tubing operations and their applications in oil and gas from our expert instructor!
Credit header image: stimline.com
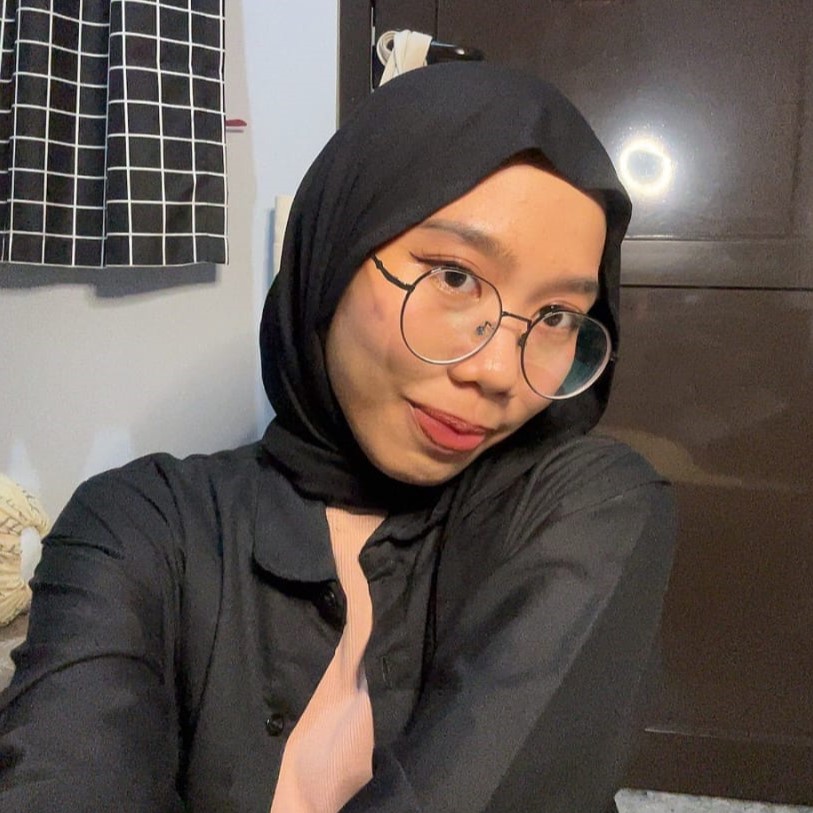
SEO specialist by day, fact-checker by night. An avid reader and content writer dedicated to delivering accurate and engaging articles through research and credible sources.