The refining business typically faces issues associated with equipment wear and tear caused by numerous degradation processes. When not addressed effectively, these concerns can result in expensive maintenance costs, operational disruptions, and potential safety hazards.
Engineers, inspectors, and maintenance teams must have a thorough understanding of these damage mechanisms in order to ensure the reliability and lifetime of fixed equipment. API 571, developed by the American Petroleum Institute (API), is a comprehensive standard that offers guidelines on damage processes that affect fixed equipment in the refinery industry.
The most recent edition of API 571 is an essential resource for industry experts who want to expand their expertise and maintain refinery safety and efficiency.
What Is API 571?
API 571 is commonly known as “Damage Mechanisms Affecting Fixed Equipment in the Refining Industry,” is a standard developed by the American Petroleum Institute that addresses the most common damage mechanisms seen in the refining industry. API 571’s primary purpose is to provide instructions for discovering, understanding, and mitigating.
These damage mechanisms in order to increase the service life of equipment and prevent unscheduled downtime.API 571 addresses damage processes such as corrosion, erosion, cracking, and mechanical failures that might jeopardize the integrity of fixed equipment such as pressure vessel, pipes, and tanks.
The publication is an invaluable resource for plant engineers, inspectors, and other experts in charge of assuring the structural integrity and safety of refinery equipment. Following the API 571 principles allows these professionals to take proactive measures to prevent damage and reduce the chance of equipment failure.
What Is API 571 Standard?
The API 571 standard is a comprehensive reference that describes the various forms of damage processes impacting fixed equipment in the refining sector. It addresses many types of corrosion, including uniform, localized, and galvanic corrosion, as well as mechanical damage mechanisms including fatigue and creep.
The standard also includes recommendations on recognizing damage using inspection and monitoring techniques, which are crucial for preserving equipment integrity. API 571 categorizes damage modes according to temperature, pressure, and chemical environment. It provides in-depth descriptions of each damage process, including its causes, characteristics, and potential outcomes.
The standard also makes advice for minimizing or preventing damage through correct material selection, design considerations, and maintenance procedures. One of the most distinguishing elements of the API 571 standard is its emphasis on risk-based inspection. RBI is a system for prioritizing inspections based on their likelihood and severity of failure.
API 571 integrates RBI principles, allowing professionals to make informed decisions about where and when to conduct inspections, ensuring that resources are used wisely in the most critical areas.
What Are API571 guidelines?
The API 571 standards provide a framework for analyzing and managing damage processes in the refining sector. These standards are founded on considerable research and industry experience, making them an accurate source of knowledge for experts in the sector.
API 571’s key guidelines are as follows:
1. Identification of Damage Mechanisms:
The standard includes extensive descriptions of the numerous damage mechanisms that can impact permanent equipment in refineries. This covers details on the causes, symptoms, and potential consequences of each damage mechanism, as well as the environmental elements that influence their development.
2. Inspection and Monitoring:
API 571 emphasizes the need of doing frequent inspections and monitoring to detect damage mechanisms early on. The standard suggests that ultrasonic testing, radiographic testing, and visual inspections be used to detect corrosion, cracking, and other types of damage.
3. Mitigation Strategies:
API 571 provides instructions for adopting appropriate mitigation measures to avoid damage mechanisms jeopardizing equipment integrity. Material upgrades, protective coatings, and cathodic protection systems are examples of such strategies.
4. Risk-Based Inspection (RBI):
As previously noted, API 571 advocates using RBI to prioritize inspection and maintenance duties. This technique allows specialists to focus their efforts on areas with the highest risk of failure, ensuring that critical equipment is kept in good working order.
Following these rules can help experts efficiently reduce the risk of equipment failure and extend the service life of essential refinery assets.
How Many Updated Versions of API 571 Since The First Launch?
1. API 571 – First Version (December 2003)
The initial release of API 571 in December 2003 marked a significant milestone in the field of industrial equipment inspection and evaluation. This first version laid down the foundational principles and guidelines for professionals in the oil, gas, and petrochemical industries.
The standard addressed issues related to corrosion, damage mechanisms, and inspection techniques. This version aimed to enhance safety and the longevity of equipment, providing a crucial resource for industry experts.
2. API 571 – Second Version (April 2011)
The second edition of API 571, released in April 2011, brought about important updates and refinements to the standards. It reflected advancements in the industry’s understanding of corrosion mechanisms, damage assessment, and risk-based inspection practices.
This version aimed to align with the latest technological and methodological developments, making it an even more robust tool for professionals. By addressing new challenges and incorporating the latest knowledge, the second edition ensured that industry experts remained well-equipped to manage equipment integrity effectively.
3. API 571 – Latest Version (March 2020)
The most recent release of API 571 in March 2020 represents the cutting edge of industry knowledge and best practices. This version incorporates the latest insights into corrosion mitigation, damage mechanisms, and the integration of risk-based inspection principles. It reflects the industry’s ongoing commitment to safety, quality, and operational efficiency.
The latest edition ensures that professionals have access to the most up-to-date information, enabling them to make informed decisions and prioritize inspections effectively. It continues to be an invaluable resource for industry experts, ensuring that they stay ahead of the curve in an ever-evolving industrial landscape.
What Updates Contained in The Latest Version of API 571?
Here are the updates to API 571 in its latest edition:
1. Structure Changes
The document organizers modified the structure by removing specific subcategories of damage mechanisms. Instead of having separate sections for things like mechanical and metallurgical failures, uniform or localized loss of thickness, high-temperature corrosion, and more, they combined these into a more streamlined format.
2. ANSI Approval
The document received approval from the American National Standards Institute (ANSI), indicating its adherence to recognized industry standards.
3. Damage Mechanism Changes
Three damage mechanisms were removed, with two of them being combined with other damage mechanisms. For example, “Steam blanketing” was combined with “Short-term Overheating-Stress Rupture,” and “Vibration-induced fatigue” was combined with “Mechanical Fatigue.” “Sulfate Stress Corrosion Cracking” was completely removed.
4. New Damage Mechanisms
The update introduced four new damage mechanisms, including “Brine Corrosion,” “Concentration Cell Corrosion,” “Hydrofluoric Acid Stress Corrosion of Nickel Alloys,” and “Oxygenated Water Corrosion (Non-boiler).”
5. Reordered Damage Mechanisms
In the 2020 edition, they changed the order in which damage mechanisms are presented. In the 2011 edition, they arranged them by their relative importance, but in 2020, they ordered them alphabetically.
6. New Annex Added
They added a new annex (Annex A), listing relevant standards and references that can be helpful when using API RP 571.
7. Introduction Paragraph
A new paragraph was added in the introduction section, emphasizing the role of identifying flaws as the first step in processes like Fitness for Service (FFS) and Risk-Based Inspection (RBI), as per API 579 and API 580.
8. Category Removal
The 2020 edition removed the previous categorization of damage mechanisms encountered in petrochemical equipment. This included five categories, like general and local metal loss, surface-connected cracking, subsurface cracking, microfissuring/microvoid formation, and metallurgical changes.
9. Metallurgical Terminology
The new edition uses more specific metallurgical terms, like mentioning the type of heat treatment (e.g., tempering, annealing) and the specific terms for metallic phases (e.g., alpha prime).
10. Statement Relocation
The team moved several statements from one part of the document to another, making it clearer and better representing their meaning.
11. US and SI Unit Changes
The 2020 edition updated the equivalent values between the US and SI units. In the 2011 edition, they directly converted the values, but in 2020, they adjusted them to reflect the nearest integer value. Additionally, the 2020 edition corrected some mistakes in the conversion values..
API 571 Latest Edition Update 2020 is essential for professionals in oil, gas, and petrochemical industries, offering crucial updates.
Enhance Your Expertise with PetroSync’s API 571 Training Program
API 571 offers essential guidelines for maintaining equipment integrity in refineries, focusing on damage mechanisms and best practices. At PetroSync, we provide a comprehensive API 571 training program to help professionals improve their understanding of damage mechanisms affecting fixed equipment.
Our training program covers the most recent edition of API 571, giving participants the information and skills needed to effectively manage the risks associated with equipment damage. Whether you’re new to the field or a seasoned pro, our API 571 training program will provide you with the tools and strategies you need to succeed in your position. With PetroSync’s training program, you may advance your profession. Join us today.
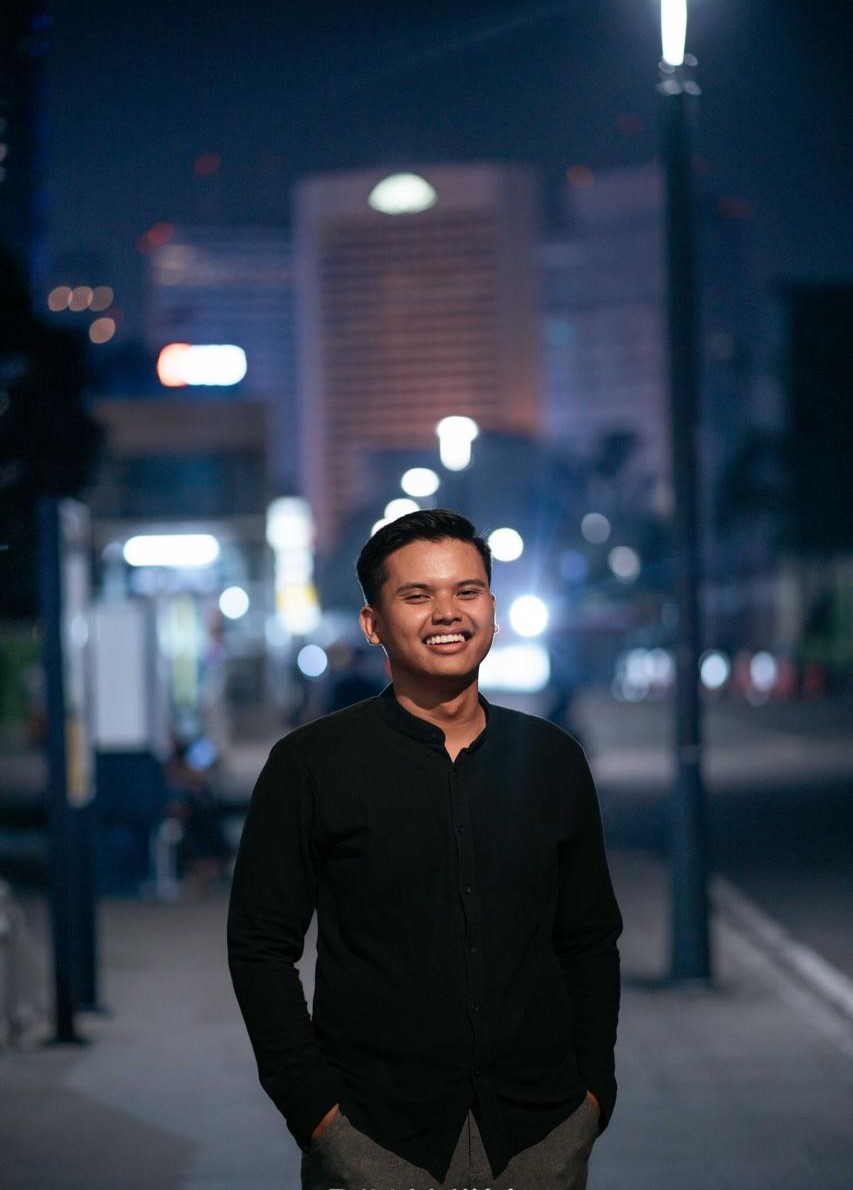
Results-oriented and thorough SEO specialist with extensive experience in conducting keyword research, developing and implementing digital website promotion strategies and plans, managing campaigns to develop company websites in the digital world, excellent knowledge of marketing techniques and principles, and attentive strong attention to detail.