Corrosion is a natural phenomenon that has significant implications for businesses including oil and gas, petrochemicals plant, and energy. Addressing corrosion issues requires a full understanding of the causes, types, and prevention methods. This page discusses the basics of corrosion, its various manifestations, and effective solutions such as corrosion engineering and monitoring.
What is a Corrosion Mechanism?
Corrosion mechanisms is the gradual degradation of materials, particularly metals, due to chemical, electrochemical, or physical interactions with their environment. A corrosion mechanisms describes the processes behind this deterioration. These mechanisms commonly lead to compromised structural integrity, which can have major safety and economical consequences in industrial applications.
Understanding these pathways is critical in corrosion engineering for building systems that can withstand degradation. Specialized corrosion materials and coatings, for example, are commonly utilized to decrease metal-corrosive agent interactions.
What is the Principle of Corrosion?
Electrochemical processes are the primary mechanism of corrosion. It occurs when a metal surface interacts with substances in the environment, such as oxygen, moisture, or salts, causing the material to deteriorate.
The principle of corrosion can be summarized as:
- Anodic Reaction: Metal atoms lose electrons and form ions (oxidation).
- Cathodic Reaction: Electrons released during oxidation are consumed, often combining with water and oxygen to form hydroxide ions.
- Electrolyte Medium: Ions move through a conductive environment, such as water or other solutions.
- Electrical Circuit: Completes the flow of electrons between anodic and cathodic sites.
In industrial settings, monitoring and inspecting corrosion are critical strategies for detecting early indicators of damage and taking appropriate action before problems grow.
What are the 4 Elements of Corrosion?
For corrosion to occur, four essential elements must be present:
1. Anode: The part of the metal where oxidation happens.
2. Cathode: The site where reduction reactions occur.
3. Electrolyte: A medium that facilitates ionic movement, often a liquid containing dissolved salts or acids.
4. Electrical Connection: A conductive path that allows electron flow between the anode and cathode.
Removing any of these factors will effectively prevent rusting. Corrosion protection measures, such as coatings and cathodic protection, disturb this process.
What are the 10 Types of Corrosion?
Understanding different types of corrosion is critical for determining the most effective preventive methods. The following are the most popular forms:
1. Uniform Corrosion: Affects the entire surface evenly, often predictable and manageable.
2. Galvanic Corrosion: Occurs between two dissimilar metals in contact within a corrosive environment.
3. Crevice Corrosion: Happens in confined spaces where stagnant fluids promote localized corrosion.
4. Pitting Corrosion: Results in small, deep pits that can compromise structural integrity.
5. Intergranular Corrosion: Targets the grain boundaries of metals, usually due to heat treatment.
6. Stress Corrosion Cracking (SCC): A combination of tensile stress and a corrosive environment causes cracks.
7. Corrosion Under Insulation (CUI): A hidden form of corrosion occurring under insulation materials on pipes or equipment.
8. Erosion Corrosion: Accelerated by the movement of corrosive fluids over metal surfaces.
9. Microbiologically Influenced Corrosion (MIC): Caused by microorganisms that produce corrosive substances.
10. Dealloying: Selective removal of one element from an alloy, such as dezincification in brass.
Each type presents specific issues that necessitate specialized solutions, which are frequently addressed via corrosion engineering approaches.
What are the 4 Stages of Corrosion?
Corrosion typically progresses through four stages:
- Initiation Stage: Surface damage begins due to exposure to corrosive agents.
- Propagation Stage: Corrosion spreads, causing visible and microscopic damage.
- Acceleration Stage: The rate of material degradation increases due to changing conditions, such as increased stress or temperature.
- Failure Stage: Structural integrity is compromised, potentially leading to catastrophic failure.
Early detection through corrosion inspection and monitoring is crucial for reducing dangers and increasing equipment life.
Join PetroSync Training: Advanced Corrosion Solutions for Maximum Efficiency
PetroSync provides a wide range of training and consulting services designed exclusively for the oil and gas, petrochemical, and energy industries. Our solutions are intended to enable experts to address and solve corrosion concerns with the greatest level of knowledge. We offer in-depth insights into corrosion mechanisms and preventative approaches.
Ensuring that teams have the information they need to protect critical infrastructure and assets. Our training programs cover both theoretical and practical aspects of corrosion, ensuring a comprehensive approach to corrosion control. Corrosion Engineer Training, which teaches participants how to identify, analyze, and mitigate corrosion risks.
Advanced Corrosion Monitoring, which allows for real-time corrosion detection and equipment lifespan predictions; and Corrosion Protection Strategies, which include cathodic protection, coatings, and material selection. We also specialize in Corrosion Under Insulation (CUI) and Stress Corrosion Cracking (SCC), offering industry-specific solutions to these challenging issues.
Our hands-on training and material expertise enable experts to implement the most efficient corrosion management solutions, eventually improving operating efficiency and asset longevity.
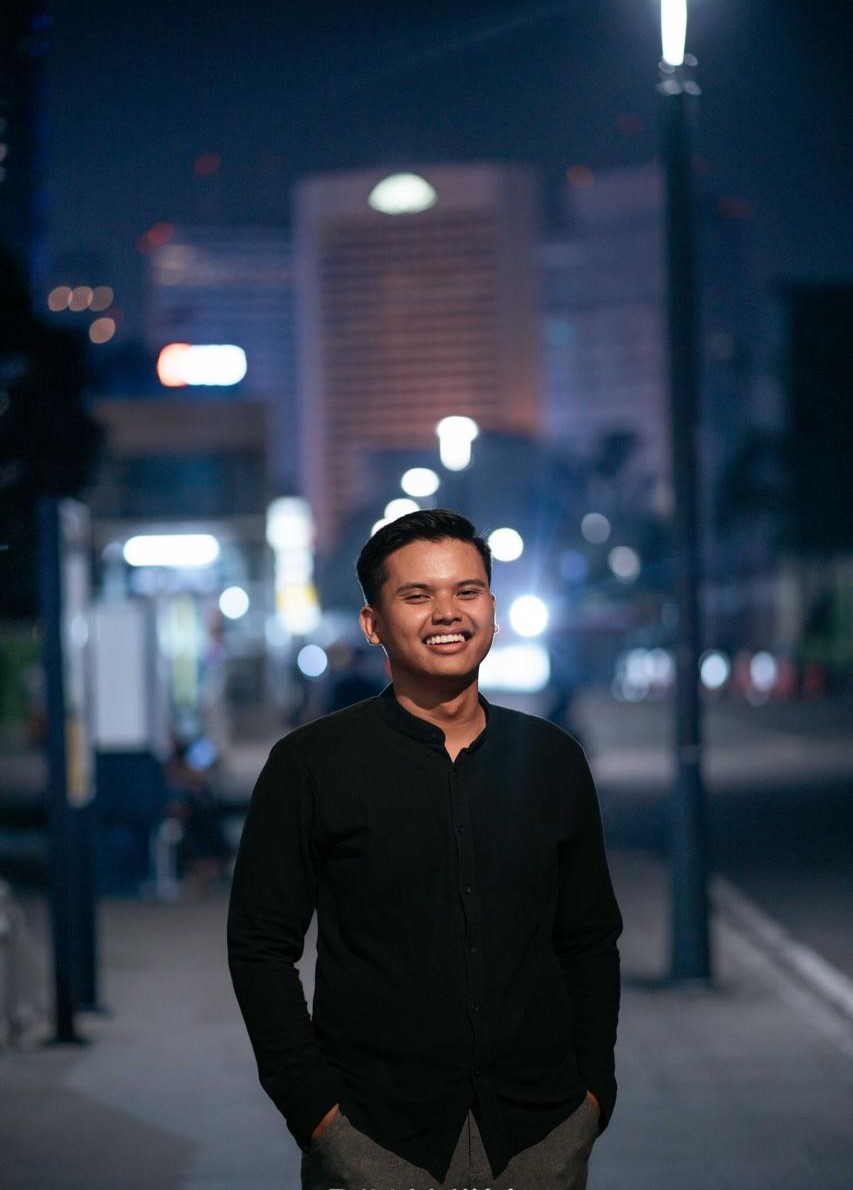
Results-oriented and thorough SEO specialist with extensive experience in conducting keyword research, developing and implementing digital website promotion strategies and plans, managing campaigns to develop company websites in the digital world, excellent knowledge of marketing techniques and principles, and attentive strong attention to detail.