Drilling rigs are critical in the oil and gas business, acting as the foundation for exploration and extraction activities. Drilling rig technological improvements over the years have made it possible to extract subsurface resources faster, safer, and more efficiently. These advancements are crucial not only for increasing productivity.
But also for addressing issues like environmental concerns and operational safety. To reduce risks and costs, contemporary drilling rigs rely on automation, real-time monitoring systems, and superior design. Automated drilling methods, for example, have considerably decreased the need for manual labor while increasing on-site safety.
Furthermore, advances like directional drilling enable operators to explore previously inaccessible reserves, hence increasing resource recovery. Understanding the advantages of modern drilling rig technologies can help firms get a competitive edge in the energy market and meet the growing demand for energy resources.
What is the Drilling Rig?
Drilling rigs are pieces of equipment used to dig boreholes or wells in the ground for a variety of purposes, the most frequent of which is oil and gas extraction. The drilling rig’s significance goes beyond its function as a structural and mechanical system for complex drilling operations. These machines range from small.
Portable equipment designed for shallow wells to enormous, permanent structures capable of drilling thousands of feet beneath the Earth’s surface. Drilling rigs are made up of several components, including a derrick, drill string, and mud pumps, which work together to penetrate the Earth’s strata. Drilling rigs started off as manually operated instruments.
But technological improvements have converted them into incredibly sophisticated equipment. Drilling rigs, whether onshore or offshore drilling, continue to be an important part of resource discovery and development.
What is a Borehole Drilling Rig?
Borehole drilling rigs are specialized instruments used to drill small and deep holes in the ground. Borehole drilling rigs are widely used for water wells, geothermal projects, and small-scale exploration. These rigs are intended for precision and efficiency, with predictable pathways to subsurface minerals.
Borehole drilling rigs are smaller and more versatile than traditional oil rigs. They may work in remote areas, making them ideal for communities or businesses seeking locally sourced water or renewable energy solutions. Furthermore, these rigs typically incorporate current technologies, such as GPS guidance and lightweight materials, which improves their operational capability.
What are the Three Main Types of Drilling Rigs?
Drilling rigs can be classified into three main categories based on their design and usage. A drilling rig for land operations is typically stationary and used for onshore projects. These rigs are commonly found in oil fields, deserts, or other stable terrains where large-scale extraction is required.
Offshore drilling rigs, on the other hand, are intended for deepwater exploration and are mounted on platforms or vessels. These include jack-up rigs, semi-submersible rigs, and drillships, each tailored to various water depths and circumstances. Finally, portable drilling rigs increase mobility.
Making them excellent for exploratory efforts or short-term drilling operations in distant areas. These categories demonstrate the diversity of the drilling rig concept and the breadth of technology available to fulfill a variety of industry needs.
What are the 4 systems of a drilling rig?
Drilling rigs are built around four essential systems that assure their performance. The drilling rig’s power system provides the energy required to run the apparatus, whether through diesel engines or electric motors. This system is the foundation of any rig, powering lifting and rotating activities.
The hoisting system, another important component of a drilling rig, raises and lowers heavy equipment, including the drill string. The drill bit and other components needed to cut through rock formations comprise the rotary system.
Finally, the circulation system circulates drilling fluids, also known as “mud,” to keep the drill bit cold, stabilize the borehole, and remove debris. These systems outline the fundamental operation of a drilling rig and emphasize its significance in efficient resource extraction.
How many drilling rigs are working?
Thousands of drilling rigs are active around the world at any given time. The number of drilling rigs changes depending on industry demand, market trends, and technological improvements. For example, the Baker Hughes Rig Count, a common industry statistic, usually represents the health of the worldwide oil and gas industry.
Monitoring drilling rig activity offers valuable information into the global energy situation. Rig demand is high in North America, the Middle East, and Asia, owing to ongoing exploration and production activity. These assets, whether onshore or offshore, show the scope and importance of resource development in today’s economy.
PetroSync Training: Your Path to Drilling Expertise
Drilling rigs are complex equipment that require extensive knowledge and expertise to operate well. PetroSync provides industry-leading training programs for drilling rig terminology and operations. These courses are intended to provide professionals with the skills necessary to succeed in the oil and gas business.
By joining PetroSync, you’ll gain practical insights into drilling rigs and their applications. The training covers essential topics such as drilling techniques, safety protocols, and equipment maintenance. With PetroSync’s support, you can build a rewarding career and stay ahead in this dynamic field.
Understanding the definition of drilling rig and its applications is crucial for anyone in the oil and gas industry. Let PetroSync guide your journey to expertise and help you unlock your potential in energy exploration.
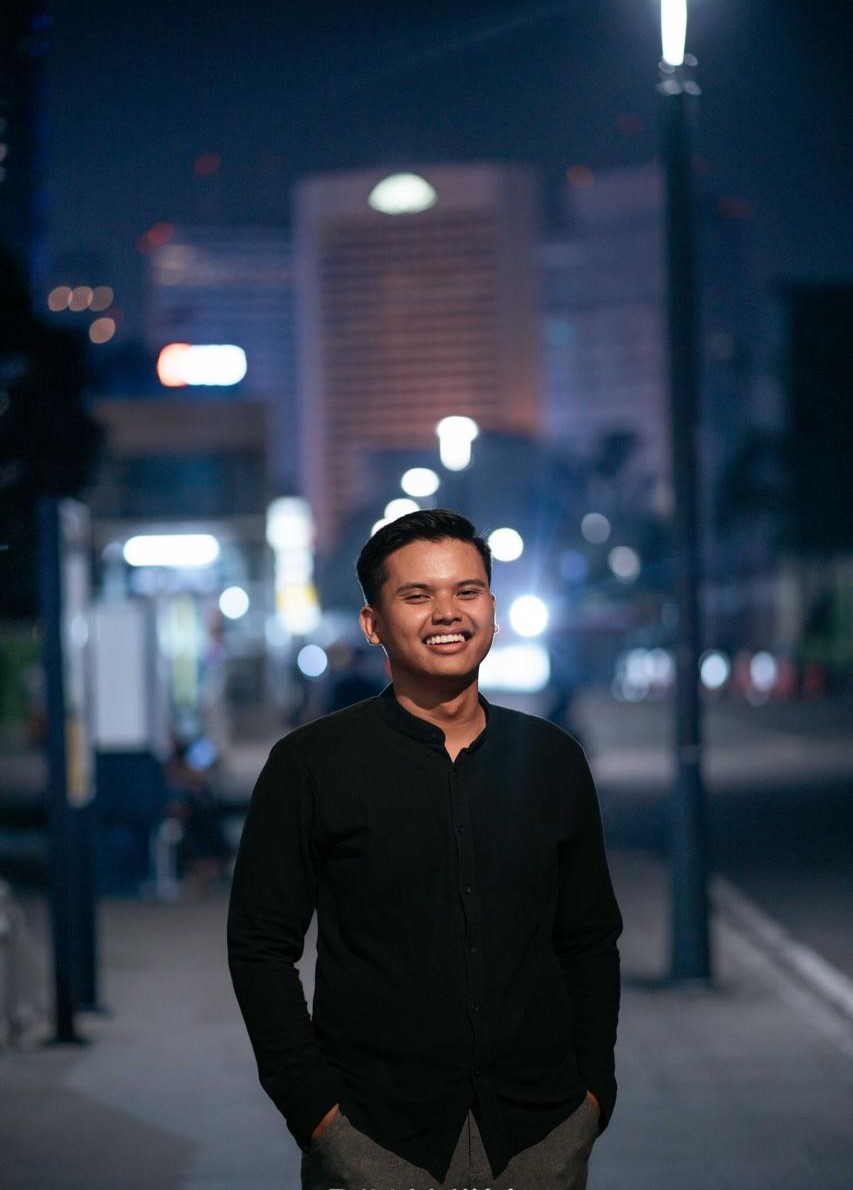
Results-oriented and thorough SEO specialist with extensive experience in conducting keyword research, developing and implementing digital website promotion strategies and plans, managing campaigns to develop company websites in the digital world, excellent knowledge of marketing techniques and principles, and attentive strong attention to detail.