The oil and gas industry, a vital component of the world energy supply, relies on complex systems to extract, process, and transport precious resources. Pipe systems are essential for guaranteeing smooth and effective operations, from carrying crude oil to refining petrochemical products. Pipe systems are vital to industrial safety and productivity.
Necessitating high-performance pipe design and long-lasting pipeline supports. In this post, we’ll go over the foundations of pipe systems, including their different forms, the differences between pipe and pipelines, and the importance of pipe in the oil and gas industry. We will also talk about PetroSync’s training program.
What is a Piping System?
Piping system is a network of pipes and fittings used in industrial environments to transfer fluids, gases, and, on occasion, solids. These systems are built to withstand exact pressures and temperatures, ensuring that products are transported securely and effectively. A pipe system generally includes components such as:
- Pipes: The main channels for material transport.
- Valves: To control the flow of fluids.
- Flanges: Connecting various parts of the pipe system.
- Fittings: Changing the direction or size of pipes as needed.
- Supports: Providing stability to avoid strain and distortion.
These components work together to ensure that the pipe system is durable, reliable, and safe under a variety of operating conditions.
What are the Types of Piping Systems?
In the oil and gas business, many types of pipe systems are used for different purposes. The primary types are:
1. Process Piping
Process piping is used in refineries and chemical plants to transport raw materials and finished products throughout the facility. This sort of piping must resist high temperatures and pressures associated with industrial activities.
2. Pressure Piping
Pressure piping, which is widely used in power plant and industrial facilities, is designed to transfer materials under high pressure, ensuring safety and reliability in high-stress conditions.
3. Cryogenic Piping
Engineered for extremely low temperatures, cryogenic pipe is critical for carrying liquefied gases such as LNG (liquefied natural gas), necessitating specialized piping design to avoid freezing or damage.
4. Utility Piping
Supporting the daily operations of facilities, utility pipe systems carry water, compressed air, and other essential utilities.
5. Oil and Gas Transmission Piping
These pipelines transport crude oil, natural gas, and related products over long distances from production sites to refineries and distribution networks.
Each pipe type must adhere to specific industry standards, such as ASME (American Society of Mechanical Engineers) and API (American Petroleum Institute), to ensure safety, efficiency, and reliability.
What is the Difference between Piping and Pipeline?
Although the terms pipe and pipeline are frequently used interchangeably, they represent distinct systems with unique functions and characteristics:
Piping vs Pipeline Comparison
Aspect | Piping | Pipeline |
---|---|---|
Purpose | Transports materials within a facility. | Transports materials over long distances. |
Location | Primarily inside plants or industrial sites. | Extends across large geographical areas. |
Design Standards | Governed by ASME codes for internal systems. | Governed by API standards for cross-country transport. |
Material | Alloy steel, stainless steel. | Carbon steel, which offers durability for long distances. |
Size | Typically smaller in diameter. | Often larger for bulk transport. |
Pipelines are typically utilized for long-distance transportation of hydrocarbons, whereas pipe systems are designed to manage materials within industrial sites, such as refineries or petrochemical plant.
What Jobs Involve Piping in the Oil and Gas Industry?
Piping specialists have a number of job options. The following are some important roles in the oil and gas business :
1. Piping Engineers
Piping engineers design and plan pipe systems to meet stringent project requirements while conforming to pipe engineering standards. This role requires a solid understanding of piping design and pipe engineer certification criteria.
2. Piping Designers
Piping designers utilize software like AutoCAD or SolidWorks to create precise models of pipe layouts, specify pipe support structures, and assure system reliability.
3. Piping Inspectors
Piping inspectors conduct frequent pipe inspections and assessments to ensure that systems meet industry standards and identify potential problems. They play an important role in ensuring industrial safety and efficiency.
4. Welders and Fabricators
Welders and fabricators work closely with pipe components to ensure that each segment is securely fastened, hence strengthening structure and safety.
5. Maintenance Technicians
Maintenance specialists oversee frequent inspections and repairs to ensure that systems are in good operating condition, particularly in high-stress locations such as pressure pipe systems.
6. Project Managers
Project managers plan and manage pipe projects to ensure that timelines, budgets, and quality standards are met.
Each position requires a full understanding of pipe systems, materials, and industry standards, highlighting the value of professional certification and training.
Elevate Your Career with PetroSync’s World-Class Piping Training Program
In the highly competitive oil and gas business, solid skills in pipe systems, design, and inspection are critical for standing out and securing top positions. PetroSync provides extensive training programs designed to arm professionals with advanced knowledge and hands-on expertise, paving the way for roles like pipe engineer, pipe inspector, and project manager.
These programs adhere to globally recognized standards such as ASME and API, guaranteeing that participants learn how to effectively design, oversee, and assess complex industrial and pressure systems. PetroSync distinguishes itself with a focus on real-world applications. Our hands-on training, delivered by experienced industry professional.
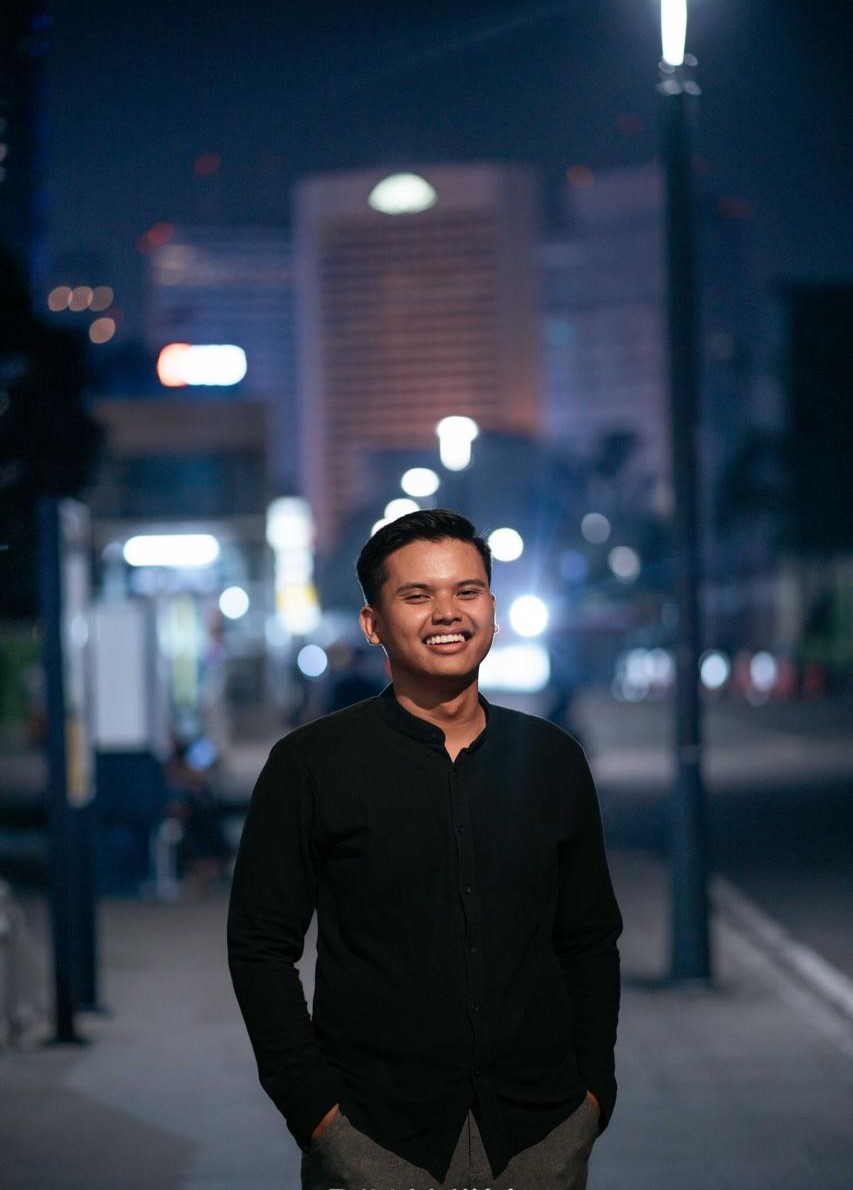
Results-oriented and thorough SEO specialist with extensive experience in conducting keyword research, developing and implementing digital website promotion strategies and plans, managing campaigns to develop company websites in the digital world, excellent knowledge of marketing techniques and principles, and attentive strong attention to detail.