Rotating equipment is one of the types of equipment in the oil and gas industry that involves machinery with moving parts that spin or rotate during operation. In this article, we will delve into the world of rotating equipment, exploring its significance, functions, and applications within various industrial sectors.
What Is Rotating Equipment?
Rotating equipment refers to machinery that has a rotating component, such as pumps, motors, turbines, compressors, and fans, and these devices have moving parts and rotate during operation.
Unlike static equipment that remains stationary, these types of equipment are designed to convert energy into mechanical motion, often used for tasks like moving fluids, generating power, or driving mechanical systems.
This type of equipment is crucial in various industries such as manufacturing, energy production, transportation, and construction due to its ability to perform mechanical work through rotational motion.
How Many Types of Rotating Equipment Are There?
There are several types of rotating equipment used in different industries. Some common types include pumps, motors, turbines, compressors, fans, and generators. These rotating equipment types serve various purposes such as moving fluids, generating power, compressing gasses, circulating air, and converting mechanical energy into electrical energy
1. Compressors
A compressor in the industry is a type of machine that increases the pressure of gasses or air by reducing its volume. It works by drawing in the gas or air and then compressing it to a higher pressure before releasing it.
Compressors are considered rotating equipment because they have moving parts that rotate during operation, such as rotors or blades, which create the compression action. This rotational motion is essential for the compressor to perform its function of increasing the pressure of gasses or air, making it a crucial component in various industrial processes like refrigeration, air conditioning, power generation, and manufacturing.
2. Gas Turbines
Gas turbines are a type of equipment used in various industries, including power generation, aviation, and oil and gas. They are engines that utilize combustion to produce a high-velocity gas stream, which then drives a turbine to generate mechanical power.
In the industry, gas turbines are commonly used in power plants to produce electricity efficiently. They are also utilized in aircraft engines for propulsion and in oil and gas facilities for driving compressors and pumps.
The role of a gas turbine as rotating equipment is significant because it converts the chemical energy of fuel into mechanical energy through the combustion process and the rotation of the turbine blades.
This mechanical energy can then be used to drive generators, compressors, or other machinery, depending on the specific application. Gas turbines are relevant as rotating equipment due to their ability to provide reliable and high-power output, making them essential in various industrial processes and power generation systems.
3. Pumps
In the industry, pumps are devices used to move fluids such as liquids or gasses from one place to another. They operate by creating mechanical pressure or suction to push or pull the fluid through pipes or channels.
Pumps play a crucial role in various industrial processes by transferring substances like water, chemicals, oil, or gasses efficiently and reliably. As rotating equipment, pumps are essential for moving fluids in sectors such as manufacturing, water treatment, oil and gas production, and chemical processing. They help maintain the flow of materials within systems and are vital components in ensuring smooth operations across different industries.
4. Steam Turbines
Steam turbines are a type of rotating equipment used in various industries, including power generation, oil and gas, and manufacturing. They are machines that convert thermal energy from steam into mechanical energy, which can then be used to drive generators or other mechanical systems.
Steam turbines play a crucial role in power plants by using high-pressure steam to spin turbine blades, which are connected to a shaft. As the blades rotate, they drive a generator to produce electricity. In industries such as oil and gas, steam turbines can be used for processes like driving compressors or pumps. Their relevance as rotating equipment lies in their ability to efficiently convert steam energy into mechanical work, making them essential for power generation and industrial processes requiring mechanical energy.
5. Gearboxes
Gearboxes in the industry refer to mechanical devices that contain gears and shafts designed to transmit and control rotational speed and torque between rotating equipment components. They are commonly used in machinery and systems where there is a need to change the speed or direction of rotational motion.
Gearboxes play a crucial role in the operation of rotating equipment by ensuring efficient power transmission, enhancing performance, and maintaining desired operating speeds. They are relevant as rotating equipment because they are essential components in various machines such as motors, turbines, pumps, and compressors, contributing to their functionality and reliability in industrial processes.
6. Centrifugal Pump
A centrifugal pump is a type of rotating equipment used in various industries to move fluids, such as liquids or gasses, by utilizing centrifugal force. It consists of an impeller that rotates inside a casing, creating a high-velocity flow that increases the fluid’s kinetic energy. This energy is then converted into pressure, pushing the fluid through the pump and into the desired system or process.
The role of a centrifugal pump is crucial in many applications. It is commonly used for pumping water, chemicals, oils, and other fluids in industries such as oil and gas, water treatment, manufacturing, and HVAC (heating, ventilation, and air conditioning) systems. Centrifugal pumps are relevant as rotating equipment because they efficiently convert mechanical energy into fluid flow, providing a reliable and continuous supply of fluids within industrial processes.
11. Reciprocating Engine / Heat Engine
A reciprocating engine, also known as a heat engine, is a type of engine that converts heat energy into mechanical work through reciprocating (back-and-forth) motion. It operates based on the principles of thermodynamics, where heat from a fuel source is converted into mechanical energy to perform useful work. Reciprocating engines are commonly used in various industries as rotating equipment, powering machinery and equipment such as pumps, compressors, generators, and vehicles.
The role of a reciprocating engine or heat engine is crucial in industrial processes and transportation. These engines provide mechanical power for driving rotating equipment like pumps and compressors, which are essential for fluid handling and processing in industries such as oil and gas, manufacturing, and power generation.
Reciprocating engines are also used in vehicles such as cars, trucks, and ships, where they convert fuel energy into mechanical energy to propel the vehicle forward. Overall, reciprocating engines play a significant role in converting heat energy into mechanical work, making them relevant and essential rotating equipment in various sectors of industry and transportation.
12. Blowers
Blowers are mechanical devices used in various industries to move air or gasses. They are a type of rotating equipment that works by generating airflow through rotating blades or impellers. Blowers play a crucial role in processes that require air circulation, ventilation, or gas compression.
Blowers are relevant as rotating equipment because they use rotational motion to create airflow, providing essential services such as cooling, drying, aeration, and maintaining pressure levels in systems. In industrial settings, blowers are commonly used in HVAC systems, wastewater treatment plants, pneumatic conveying systems, and industrial processes where controlled airflow is necessary for efficient operations.
13. Pressure Enhancement
Pressure enhancement in the industry refers to the process of increasing the pressure of fluids or gasses within a system. This enhancement is important for various reasons such as improving efficiency, facilitating transportation, or meeting operational requirements.
Rotating equipment, such as pumps and compressors, plays a crucial role in pressure enhancement by mechanically increasing the pressure of fluids or gasses. For example, pumps are used to enhance the pressure of liquids, while compressors are used to enhance the pressure of gasses.
What Is The Difference between Static and Rotating Equipment?
The main difference between static and rotating equipment lies in their movement during operation. Static equipment stays in one place and doesn’t move, such as tanks and pipes. On the other hand, rotating equipment has moving parts that spin or rotate during operation, like pumps and compressors.
Static equipment is used for tasks like storage and containment, while rotating equipment is used for tasks like moving fluids or gases and generating mechanical power. Both types are important in industrial processes but serve different purposes based on their movement characteristics.
In conclusion, rotating equipment plays a crucial role in the oil and gas industry by performing tasks such as pumping fluids, compressing gasses, generating power, and facilitating mechanical processes. The design, creation, and inspection of rotating equipment are governed by stringent standards to ensure safety, reliability, and compliance with industry requirements.
Two prominent standards in this regard are API standards and ASME codes. These standards provide guidelines and best practices for the design, fabrication, installation, and maintenance of rotating equipment, contributing to the overall efficiency and integrity of operations across industries.
PetroSync offers specialized training programs in API standards and ASME codes to help engineers master the design, operation, and maintenance of rotating equipment in the oil and gas industry. These training courses cover a wide range of topics related to pumps, compressors, turbines, and other rotating machinery, providing you with valuable insights and practical skills to ensure safe and efficient operation of equipment.
By attending PetroSync’s API training and ASME training, you can enhance your knowledge, stay updated with industry standards, and improve your ability to manage and optimize rotating equipment in various industrial applications.
Credit header image: Vecteezy
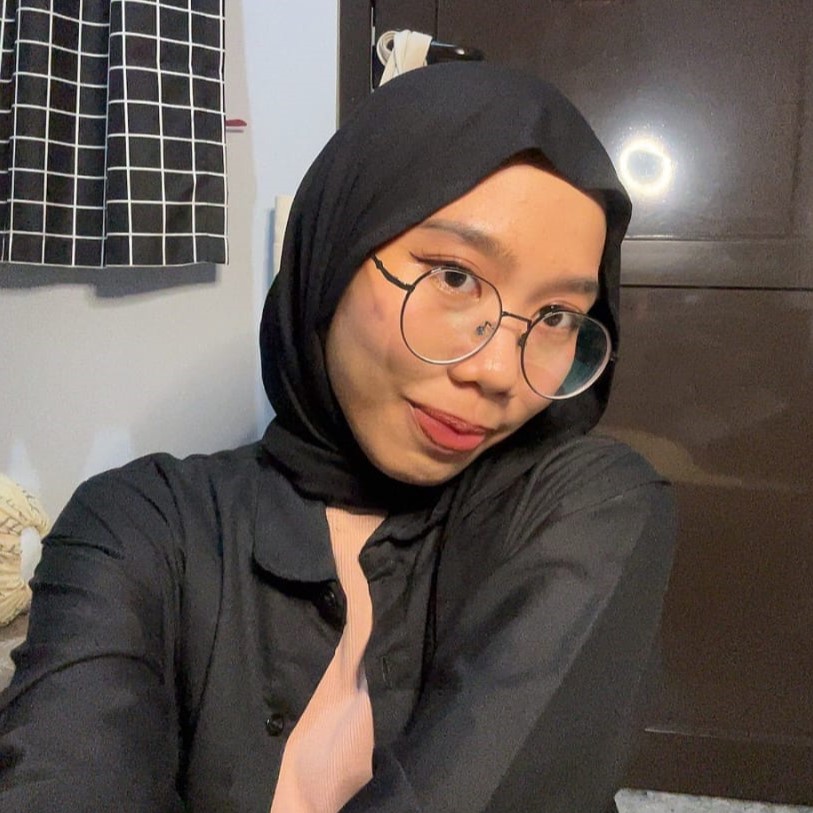
SEO specialist by day, fact-checker by night. An avid reader and content writer dedicated to delivering accurate and engaging articles through research and credible sources.