Understanding well integrity is vital in drilling operations. It’s essential for ensuring the safety, reliability, and efficiency of oil and gas wells throughout their lifespan. In this article, we explore the concept of well integrity, including what it is, its different types, and the procedures for maintaining it. By examining these aspects, we aim to provide readers with a clear understanding of why well integrity matters and its importance in the oil and gas industry. Join us as we unravel the complexities of well integrity and its critical role in drilling operations.
What Is A Well Integrity?
As a multidisciplinary approach, well integrity refers to the ability of a well, typically an oil or gas well, to safely contain the fluids it is meant to hold within its intended boundaries. Think of it like a sturdy container that prevents any leaks or spills from occurring underground. Well integrity is crucial because any failure in it can lead to environmental damage, safety hazards, and even loss of valuable resources. Regular inspections and maintenance are necessary to ensure that a well maintains its integrity over time.
What Is A Well Integrity Engineer?
A well integrity engineer is a professional responsible for maintaining full control of fluids within a well at all times, in order to prevent unintended fluid movement or loss of containment to the environment, and ensuring the safety and reliability of oil and gas wells throughout their lifespan.
They focus on maintaining the integrity of well structures, including casing, tubing, and cementing, to prevent leaks or failures that could lead to environmental damage or safety hazards. Well integrity engineers conduct inspections, tests, and assessments to identify potential issues and implement corrective measures to ensure that wells operate safely and efficiently. They play a critical role in protecting the environment and ensuring compliance with regulatory standards in the oil and gas industry.
What Are The Primary and Secondary Barriers of Well Integrity?
There are two kinds of barriers in well integrity.
1. Primary Barriers
Primary barriers are the first line of defense in ensuring well integrity. They are designed to prevent the escape of fluids from the well into the surrounding environment. The primary barrier is typically the well casing, which is a large steel pipe inserted into the drilled hole and cemented in place. This casing creates a physical barrier between the wellbore and the surrounding rock formations.
The cement used to fix the casing in place also plays a crucial role in creating a secure seal. It fills the space between the casing and the rock wall, providing additional support and preventing any leakage. Overall, the primary barrier’s main purpose is to isolate the wellbore and contain any fluids or gasses within it.
2. Secondary Barriers
Secondary barriers act as a backup system to the primary barriers and provide an additional layer of protection to ensure well integrity. One of the main secondary barriers is the blowout preventer (BOP) system, which is installed on top of the wellhead. The BOP is a complex set of valves and equipment designed to control the flow of fluids in the event of an unexpected pressure surge or well control issue.
It can quickly seal off the wellbore to prevent a blowout, which is an uncontrolled release of fluids from the well. Additionally, secondary barriers may include safety valves and other pressure control devices installed both on the surface and downhole. These components work together to provide redundancy and ensure that even if the primary barriers fail, there are still measures in place to contain any potential leaks or blowouts. In summary, secondary barriers are backup systems that complement the primary barriers to enhance overall well integrity and safety.
How Can We Maintain The Well Integrity of The Well Throughout Its Entire Lifespan?
To maintain well integrity throughout its entire lifespan, various phases require careful attention and adherence to stringent standards.
1. The Planning Phase
During planning, critical decisions are made regarding the selection of well components like casing, cement, and tubing. These components must withstand extreme pressures, temperatures, erosion, and corrosion throughout the well’s expected lifetime. Any changes made during planning should be rigorously assessed for potential impacts on well integrity.
2. The Construction Phase
As the well is constructed, multiple barriers are put in place to prevent fluid flow from the reservoir to the surface. These barriers are composed of materials like steel pipe and cement, and stringent performance criteria ensure their effectiveness. Regular pressure testing and logging verify the integrity of these barriers.
3. The Production Phase
During production, ongoing monitoring and verification of barrier components, such as downhole safety valves and production trees, are essential. Pressure testing of casing and tubing annuli helps detect potential leaks or corrosion. Regular maintenance may involve replacing downhole components to ensure the safe operation of the well. Monitoring changes over time allows for early detection and resolution of issues.
4. The Abandonment Phase
At the end of the well’s life, proper abandonment procedures are crucial. Components are removed to allow for the setting of permanent barriers, typically consisting of cement and steel. These barriers must be robust enough to contain any leaks from reservoirs or zones indefinitely, considering potential pressure recharging or CO2 injection. Re-entering an abandoned well for leak repairs can be costly, emphasizing the importance of thorough abandonment procedures.
Throughout each phase, competent personnel, adherence to industry standards, and proactive management are vital for successful well integrity management. By prioritizing safety and adherence to standards, operators can minimize risks and ensure the long-term integrity of oil and gas wells.
How To Successfully Achieve Well Integrity?
Achieving well integrity requires careful consideration of several key factors:
1. Planning and Design
During the planning and design phase, it’s essential to select robust well components capable of withstanding the expected pressures, temperatures, and environmental conditions over the well’s lifespan. This includes casing, cement, and tubing. Changes made during planning should be thoroughly assessed to ensure they do not compromise well integrity. Additionally, a comprehensive plan for well abandonment should be included in the design to address the end of the well’s life cycle.
2. Construction and Installation
Proper construction and installation practices are crucial for establishing well integrity. All components, including casing and cement, must be installed correctly to create effective barriers that prevent fluid movement between the reservoir and the surface. Regular pressure testing and logging should be conducted during construction to verify the integrity of these barriers and identify any potential issues early on.
3. Monitoring and Maintenance
Continuous monitoring and maintenance are essential throughout the well’s operational life to uphold well integrity. This includes regular inspections of barrier components, such as downhole safety valves and production trees, to ensure they are functioning properly.
Pressure monitoring of casing and tubing annuli helps detect leaks or corrosion. Maintenance activities, such as replacing downhole components or conducting chemical treatments, should be performed as needed to mitigate risks and maintain well integrity.
4. Compliance and Documentation
Adherence to industry standards and regulatory requirements is critical for achieving and maintaining well integrity. Operators must ensure that all activities related to well construction, operation, and maintenance comply with applicable regulations and industry best practices. Documentation of all well-related activities, including inspections, tests, and maintenance procedures, is essential for accountability and traceability.
By carefully considering these factors and implementing appropriate measures throughout the well’s lifecycle, operators can successfully achieve and maintain well integrity, ensuring safe and efficient operation while minimizing environmental and safety risks.
What Are Some FAQs Related to Well Integrity?
Get answers to common questions about well integrity that we already compile for you.
1. What Phase of The Well Is Well Integrity Important?
Well integrity is crucial during the production and/or injection phases of a well’s life, which typically last the longest. During this time, it’s essential to ensure the integrity of accessible barrier components, such as downhole safety valves and production trees. Regular pressure testing of these components is necessary to manage well integrity effectively.
By maintaining the integrity of these components, operators can prevent unintended fluid movement and ensure the safe and efficient operation of the well. This phase requires careful monitoring and verification to uphold the integrity of the well and minimize the risk of environmental damage or safety hazards.
2. What Are The Elements of a Well Barrier?
Before we explore well barriers further, it’s essential to grasp the basic components that make them effective in keeping the well safe. These elements are fundamental for ensuring that fluids stay securely contained within the well.
1. Casing
Casing is a steel pipe installed in the wellbore to provide structural support and prevent the collapse of the wellbore walls. It serves as the primary barrier between the formation fluids and the environment. Casing is typically installed in sections, with each section cemented in place to create a secure barrier.
2. Cementing
Cementing involves pumping cement into the wellbore around the casing to create a seal between the casing and the surrounding formation. This cement sheath reinforces the casing and prevents fluid migration between different geological layers. Proper cementing is essential for ensuring the integrity of the well barrier.
3. Completion Components
Completion components include various tools and equipment installed in the well to facilitate production or injection operations. These components may include tubing, packers, and valves. They play a crucial role in controlling the flow of fluids within the well and ensuring the integrity of the barrier system.
4. Wellhead
The wellhead is the equipment installed at the surface of the well to support the casing and provide a connection point for surface equipment. It includes valves and fittings that allow for the control of fluid flow and pressure. The wellhead serves as a vital part of the well barrier by providing a secure interface between the downhole components and the surface equipment.
5. XTree
The XTree, or Christmas tree, is an assembly of valves, fittings, and sensors installed on top of the wellhead to control the flow of fluids during production or injection operations. It provides a means of accessing the well and monitoring its performance. The XTree plays a critical role in maintaining the integrity of the well barrier by allowing for safe and efficient operation of the well.
In conclusion, maintaining well integrity is essential for ensuring the safety, reliability, and efficiency of upstream operations in the oil and gas industry. Well integrity safeguards against potential hazards such as fluid leaks, blowouts, and environmental contamination. By upholding well integrity, operators can minimize risks, protect the environment, and ensure the uninterrupted production of hydrocarbon resources.
PetroSync understands the critical importance of maintaining well integrity in the oil and gas sector. That’s why we develop specialized training programs specifically designed to provide professionals like you with the necessary knowledge and skills to effectively address well integrity challenges.
Our Well Integrity Cased Hole Logging and Reservoir Monitoring training offers comprehensive insights into the latest techniques and best practices for assessing and monitoring well integrity. By participating in our training, you will acquire valuable expertise that will enable you to enhance safety, optimize production, and protect the environment in your upstream operations.
credit header image: Bloomberg
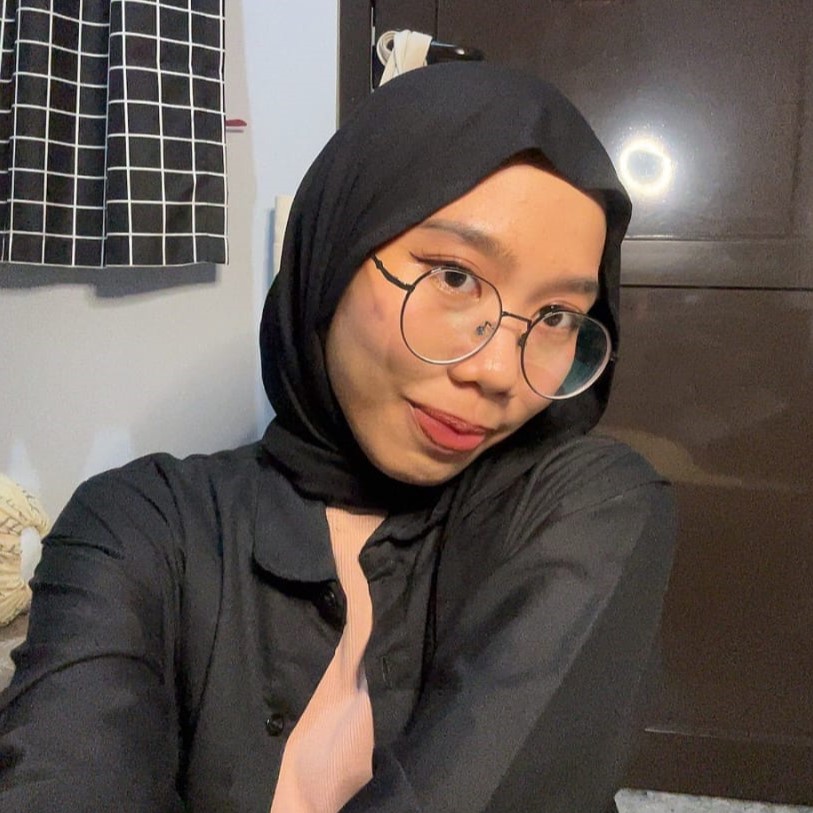
SEO specialist by day, fact-checker by night. An avid reader and content writer dedicated to delivering accurate and engaging articles through research and credible sources.