In the realm of maintenance practices, Reliability Centered Maintenance (RCM) emerges as a systematic approach to enhance the performance and lifespan of assets. Understanding and applying effective strategy requires navigating through three RCM phases. This article serves as a guide, providing a comprehensive introduction to these fundamental phases of Reliability Centered Maintenance.
What Is Reliability-Centered Maintenance?
Reliability-Centered Maintenance (RCM) is a structured maintenance strategy designed to ensure that maintenance tasks are performed in a safe, efficient, cost-effective, and reliable manner by systematically analyzing potential failure modes of equipment and prioritizing maintenance tasks based on their impact on safety, operations, and costs.
RCM aims to optimize maintenance efforts by identifying the most effective maintenance strategies for each asset, considering factors like criticality, risk, and the consequences of failure. Ultimately, RCM helps organizations transition from reactive maintenance practices to a proactive and strategic approach, enhancing overall asset reliability and performance.
What Is The Principle of Reliability-Centered Maintenance?
The principle of Reliability-Centered Maintenance (RCM) revolves around a systematic approach to ensure the reliability of operational systems. Let’s break down the key principles.
1. Preserve System Functions
This principle emphasizes maintaining the functions of a system. In RCM, the focus is on understanding and preserving the essential roles that systems play in the overall operation. The goal is to prevent failures that could impact these critical functions.
2. Identify Failure Modes Affecting System Functions
RCM involves a thorough examination to identify potential ways in which a system can fail. By understanding the various failure modes, organizations can proactively address vulnerabilities that might compromise system functions.
3. Prioritize Failure Modes Based on Risk and Cost Projections
Once failure modes are identified, RCM prioritizes them by considering the associated risks and projected costs. This step ensures that attention is directed towards addressing the most critical failure modes, balancing the importance of risk mitigation with cost-effectiveness.
4. Select the Most Effective Tasks to Control Failure Modes
RCM doesn’t apply a one-size-fits-all approach. Instead, it selects tailored maintenance tasks that are most effective in controlling the identified failure modes. This involves choosing tasks that strike the right balance between mitigating risk and managing costs.
What Is The Benefit of Applying Reliability-Centered Maintenance?
Applying Reliability-Centered Maintenance (RCM) offers several valuable benefits
1. Enhanced Reliability
RCM helps improve the reliability of operational assets by identifying and addressing potential failure modes before they impact system functions.
2. Cost Efficiency
By prioritizing maintenance tasks based on risk and cost projections, RCM ensures that resources are allocated efficiently, focusing on critical areas and avoiding unnecessary expenses.
3. Increased Safety
The systematic approach of RCM enhances safety by proactively addressing failure modes that could pose risks to personnel, the environment, or overall operations.
4. Extended Equipment Lifespan
RCM aids in identifying the most effective tasks to control failure modes, contributing to the longevity of equipment and reducing the need for premature replacements.
5. Optimized Maintenance Strategies
RCM shifts maintenance from a reactive to a proactive approach, allowing organizations to strategically plan and execute maintenance tasks, leading to better overall asset performance.
6. Improved Decision-Making
The prioritization of failure modes based on risk and cost projections provides a clearer understanding of where to focus efforts, enabling informed and effective decision-making in maintenance activities.
What Are The Three Phases of Reliability-Centered Maintenance?
In general, there are three RCM phases.
Phase 1 of RCM: Decision
The first RCM phase of Reliability-Centered Maintenance (RCM) is the Decision phase. In this phase, the focus is on justifying and planning based on the organization’s needs, readiness, and desired outcomes. Here are the key steps in this phase
1. Analysis Preparation
A successful RCM analysis requires an effective cross-functional team, including maintenance employees, project leaders, subject matter experts, and executive leadership. Documenting procedures and the project plan is crucial to keeping the team on track. This is the time to outline organizational goals, project management considerations, budget, timeline, and potential obstacles.
2. Select Equipment for RCM Analysis
Choose equipment critical to operations, subject to the repair vs. replace cost debate, and previously included in preventive maintenance spending. The selected equipment should meet criteria such as the potential difficulty of detecting failures, impact on safety, impact on operations, and impact on spending.
3. Identify Functionality
Create a comprehensive list of the equipment’s functionality, including as much data as possible. Specify desired asset performance levels rather than actual performance, as this may reveal operational or maintenance issues. The functionality of the system drives the required functions of the equipment supporting the system functions.
Phase 2 of RCM: Analysis
The second RCM phase of Reliability-Centered Maintenance (RCM) is focused on conducting a high-quality RCM study. Here are the key steps in this phase
1. Identify Functional Failures
Functional failures refer to the inability of an asset or system to meet acceptable standards of performance. This includes poor performance, overperformance, performing unintended functions, or complete failure. For instance, if a motor bearing is failing due to a lack of lubrication, a Total Functional Failure would be the motor not rotating and failing to function.
2. Identify and Evaluate the Effects of Failures
Document the actual consequences when failures occur. What can be observed? Assess the impact of failures on production and determine if there are significant safety concerns.
3. Identify Failure Modes
Consider failure modes after identifying equipment and systematic functional failures. Use techniques like Failure Mode and Effects Analysis (FMEA) to systematically identify all possible failures. Understand the effects of failure by addressing questions such as safety concerns, impact on operation/production, and whether the failure results in full or partial outages.
In summary, the second phase of RCM involves pinpointing functional failures, understanding the effects of failures, and identifying failure modes through systematic analysis. This phase ensures a comprehensive understanding of potential issues and sets the stage for developing effective maintenance strategies to address these failures.
Phase 3 of RCM: Act
The third RCM phase of Reliability-Centered Maintenance (RCM) is the Act phase. In this phase, the focus is on implementing the study’s recommendations to update asset and maintenance systems, procedures, and design improvements. Here are the key steps in this phase:
1. Select Maintenance Tasks
Identify the most appropriate maintenance action based on the information about failure modes. Maintenance tasks can be categorized into two groups:
- Proactive Tasks: These involve preventive and predictive maintenance techniques to prevent equipment or system failures. Preventive maintenance is scheduled based on time or usage, reducing the risk of failure. Predictive maintenance, or condition monitoring, detects failures before they occur.
- Default Actions: This includes reactive maintenance or “run to failure” mode, where equipment is allowed to run until it fails, and then maintenance is performed. The choice between proactive tasks and default actions depends on the understanding of failure modes, equipment criticality, and the economic impact of failure.
In summary, the act phase involves taking action based on the analysis, updating maintenance tasks and system procedures, and making improvements to asset design. It encompasses choosing between proactive tasks and default actions, ensuring that the selected maintenance strategies align with the findings of the RCM analysis and contribute to overall production efficiency.
In conclusion, Reliability-Centered Maintenance (RCM) is a systematic and proactive approach that enhances the reliability, safety, and efficiency of operational assets. Through its three essential RCM phases—Decision, Analysis, and Act—RCM guides organizations in optimizing maintenance strategies.
By applying RCM phase, organizations prioritize critical maintenance tasks, ensuring resources are efficiently allocated. Proactive measures such as preventive and predictive maintenance are employed to prevent failures, while reactive actions are considered when appropriate.
The holistic approach aligns maintenance efforts with the specific needs and challenges of each asset, ultimately leading to enhanced reliability, prolonged equipment lifespan, and improved overall operational performance.
To empower organizations in implementing Reliability-Centered Maintenance (RCM) effectively, PetroSync offers specialized RCM training. This training program is designed to equip maintenance professionals, project leaders, and subject matter experts with the knowledge and skills needed to apply RCM principles successfully. As industry leaders, PetroSync provides a platform for continuous learning and development, enabling you to stay abreast of best practices and excel in the application of RCM methodologies.
Credit: iStock
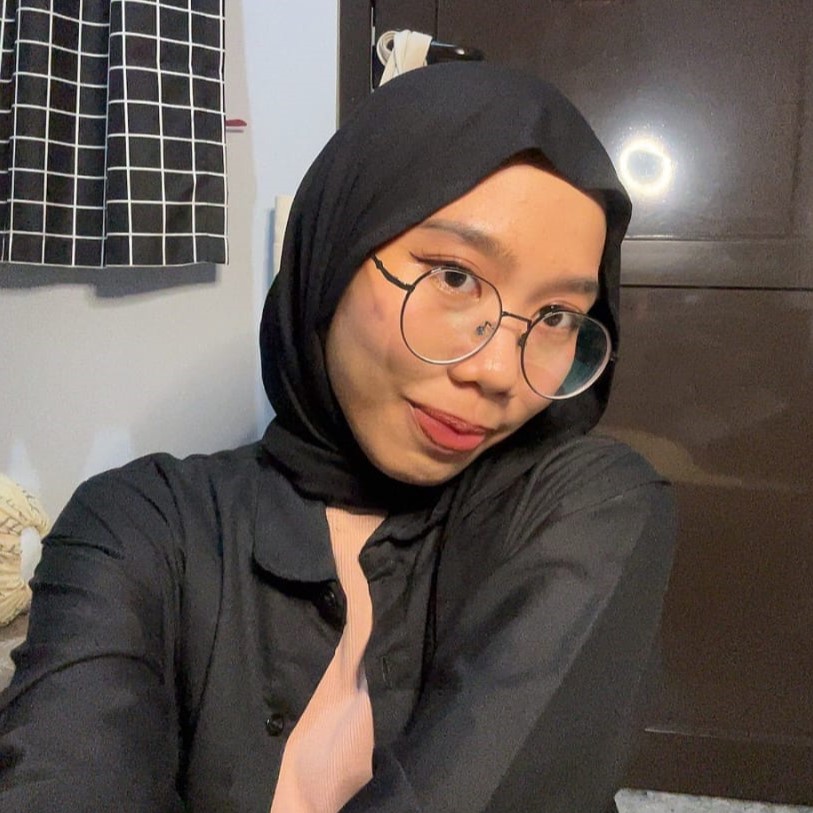
SEO specialist by day, fact-checker by night. An avid reader and content writer dedicated to delivering accurate and engaging articles through research and credible sources.