Equipment failure can disrupt operations, lead to costly repairs, and compromise safety. In this article, we explore the common 11 causes of equipment failure and provide actionable insights on how to prevent them. Drawing on expertise and real-world experiences, this article aims to empower you with the knowledge needed to keep your equipment running smoothly.
What Is Equipment Failure?
Equipment failure refers to the condition in which a machine or device does not operate as intended, experiencing problems or malfunctions that lead to a breakdown in its normal operation. It occurs when the equipment experiences issues such as wear and tear, electrical problems, mechanical issues, or other unexpected factors that hinder its proper functioning.
This situation necessitates a thorough examination and understanding of the root causes behind the equipment failure. A comprehensive analysis, considering factors like wear and tear, electrical malfunctions, mechanical issues, and unexpected challenges, is crucial for developing effective maintenance strategies.
By identifying and addressing these underlying issues, organizations can work towards enhancing the reliability and performance of their equipment, ultimately minimizing the risk of future breakdowns. Implementing regular maintenance practices and staying proactive in addressing potential concerns contribute to a more robust and dependable operational environment.
What Are Some Types of Equipment Failure?
1. Improper Maintenance
Improper maintenance is a common cause of equipment failure. When machinery is not regularly inspected, serviced, or repaired according to recommended guidelines, it becomes more susceptible to malfunctions. Regular and timely maintenance is essential to ensure that equipment operates at its best and to identify potential issues before they escalate.
Implementing a proactive and scheduled maintenance program is crucial to address improper maintenance issues. Establishing clear guidelines for regular inspections, servicing, and repairs, and ensuring that maintenance tasks are performed by trained personnel helps maintain equipment in optimal condition. Additionally, investing in a computerized maintenance management system (CMMS) can aid in tracking and scheduling maintenance activities efficiently.
2. Electrical Discharge
Electrical discharge, such as power surges or electrical shorts, can lead to equipment failure. These sudden bursts of electricity can damage electronic components, affecting the proper functioning of the equipment. Employing protective measures, such as surge protectors, can help mitigate the risk of electrical discharge-related failures.
To mitigate the risk of equipment failure due to electrical discharge, installing surge protectors is a preventive measure. Surge protectors act as a barrier against sudden bursts of electricity, safeguarding electronic components. Regularly checking and replacing surge protectors when needed is essential to ensure their continued effectiveness in preventing electrical discharge-related failures.
3. Erratic Failure
Erratic failures are unpredictable and can occur without warning. These failures often result from unexpected issues that are challenging to foresee or prevent. Understanding the patterns and potential causes of erratic failures can aid in developing strategies to minimize their occurrence.
Understanding patterns and potential causes of erratic failures requires a robust predictive maintenance program. Implementing condition monitoring technologies, such as sensors and predictive analytics, can help identify early signs of irregularities. This proactive approach enables timely intervention, reducing the occurrence of unpredictable failures.
4. Operator Error
Operator error, arising from mistakes made during equipment operation, can contribute to failures. Insufficient training, lack of attention, or misinterpretation of operational procedures can lead to accidents or malfunctions. Adequate training programs and clear operational guidelines are essential in reducing the likelihood of operator-related failures.
Preventing operator-related failures involves comprehensive training programs and clear operational guidelines. Investing in ongoing training to enhance operator skills and awareness of equipment functionality is crucial. Establishing a culture that encourages open communication about operational challenges and mistakes fosters continuous improvement and reduces the likelihood of errors.
5. Distorted Reliability Culture
A distorted reliability culture within an organization can undermine equipment performance. When there is a lack of emphasis on reliability, organizations may neglect necessary maintenance practices, leading to increased instances of equipment failure. Fostering a culture that prioritizes reliability and proactive maintenance is crucial in preventing such failures.
Addressing a distorted reliability culture involves leadership commitment and communication. Promoting the importance of reliability and proactive maintenance at all organizational levels helps establish a culture that prioritizes equipment performance. Providing resources and support for maintenance initiatives reinforces the value of reliability in the organization.
6. Physical Wear and Tear
Physical wear and tear occur over time as equipment components experience friction, stress, and deterioration. Regular usage without proper maintenance accelerates wear and tear, eventually leading to diminished performance and potential failures. Implementing routine inspections and timely replacements of worn-out parts can mitigate this issue.
Mitigating physical wear and tear requires a preventive maintenance approach. Implementing routine inspections to identify signs of wear, and scheduling timely replacements of worn-out parts, helps extend equipment lifespan. Lubrication programs and the use of predictive maintenance technologies can further minimize the impact of wear and tear.
7. Aging Equipment
Aging equipment is prone to breakdowns due to the natural degradation of materials over time. Older machines may experience more frequent failures as their components become more susceptible to wear, corrosion, and fatigue. Planning for equipment upgrades or replacements becomes essential to maintain reliability in the face of aging.
Planning for equipment upgrades or replacements is a preventive action against failures due to aging equipment. Conducting regular assessments of the remaining useful life of critical components helps in anticipating potential issues. Developing a long-term capital expenditure plan enables organizations to budget for and strategically replace aging equipment.
8. Common Types of Equipment Malfunctions
Common equipment malfunctions encompass a range of issues, including leaks, vibrations, overheating, or unusual noises. Identifying and categorizing these malfunctions helps in diagnosing root causes and implementing targeted maintenance measures to address specific problems promptly.
Addressing common equipment malfunctions involves a proactive approach to maintenance. Categorizing malfunctions and developing targeted maintenance measures based on identified issues ensures a more effective response. Regular training for maintenance personnel on troubleshooting and diagnosing common malfunctions enhances their ability to address problems promptly.
9. Failure to Perform Proper Maintenance
Failure to perform proper maintenance, either due to budget constraints or oversight, significantly increases the risk of equipment failure. Regularly scheduled maintenance, including lubrication, inspections, and component replacements, is crucial for sustaining optimal equipment performance.
Preventing failures due to a lack of proper maintenance involves establishing a robust preventive maintenance schedule. Ensuring that budgetary constraints do not compromise essential maintenance tasks is vital. Implementing a systematic approach to lubrication, inspections, and component replacements, even in resource-constrained environments, helps sustain optimal equipment performance.
10. Improper Operation
Improper operation, such as exceeding equipment capacity or using it in ways not intended by design, can lead to accelerated wear and unexpected failures. Proper training for equipment operators and clear guidelines on usage are vital to prevent issues stemming from improper operation.
Preventing failures stemming from improper operation requires a focus on operator training and adherence to guidelines. Ongoing training programs that emphasize safe and proper equipment operation are essential. Clear communication channels between operators and maintenance teams also facilitate the identification and resolution of issues related to improper operation.
11. Lack of Inspections
A lack of regular inspections can result in undetected issues that may lead to equipment failure. Inspections help identify potential problems before they escalate, allowing for timely intervention. Instituting a comprehensive inspection routine is essential for maintaining equipment reliability and preventing unforeseen breakdowns.
Instituting a comprehensive inspection routine is a preventive action against failures resulting from a lack of inspections. Regularly scheduled inspections, incorporating visual assessments and the use of diagnostic tools, help identify potential problems before they escalate. Establishing a culture that values and prioritizes routine inspections contributes to maintaining equipment reliability.
To sum up, preventing equipment failures is crucial for smooth operations and cost savings. A strong maintenance strategy, combining regular checks and targeted repairs, is vital to counter factors like improper maintenance, electrical issues, and operator errors.
Understanding asset management, which involves planning for equipment lifecycles and embracing reliability-centered approaches, guides informed decisions on upgrades and replacements. These strategies help organizations not only address immediate needs but also ensure long-term resilience and efficiency.
Embracing a proactive maintenance culture and leveraging asset management knowledge position organizations to adapt to evolving challenges, reduce risks, and prolong the lifespan of critical equipment, providing a competitive advantage in dynamic industries.
To enhance your understanding and application of reliability-centered maintenance principles, we strongly encourage you to consider undertaking training offered by PetroSync. This specialized training will empower you with the skills needed to implement effective maintenance strategies, identify critical failure modes, and optimize asset performance.
By enrolling in PetroSync’s reliability-centered maintenance training, you’ll gain valuable insights into preventive and predictive maintenance techniques, enabling us to make informed decisions that enhance equipment reliability and minimize downtime. The knowledge and expertise acquired through this training will not only benefit your professional development but will also contribute significantly to the operational efficiency and resilience of our organization’s assets.
Invest in your skills and the success of our organization by enrolling in reliability-centered maintenance training with PetroSync today!
Credit: Pexels
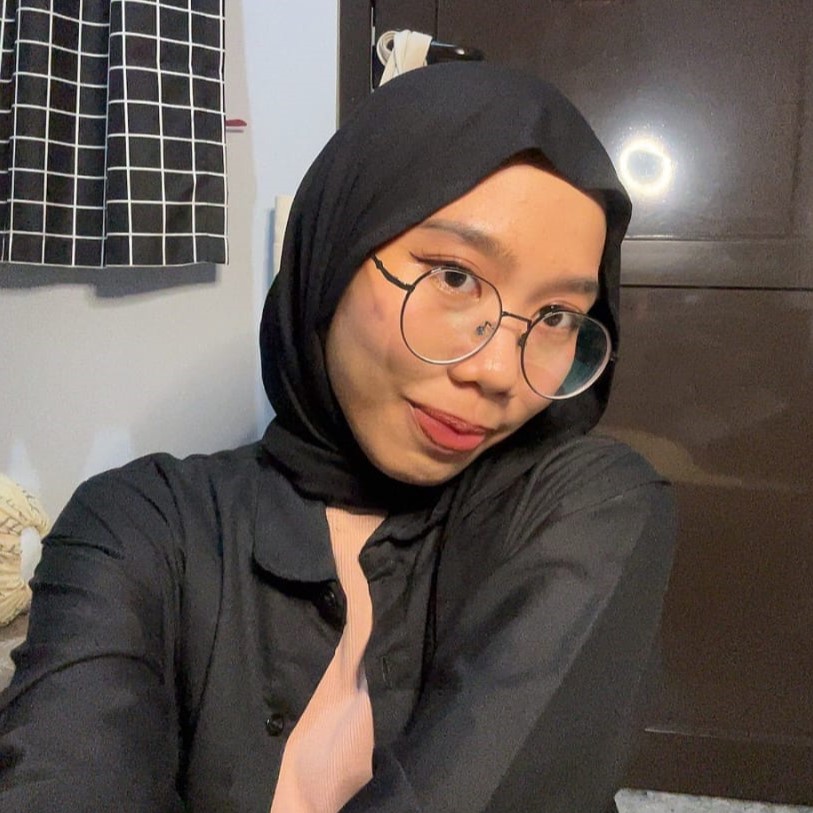
SEO specialist by day, fact-checker by night. An avid reader and content writer dedicated to delivering accurate and engaging articles through research and credible sources.