Heat exchanger type are critical for evaluating energy efficiency, operational costs, and system longevity. Selecting the appropriate kind provides efficient heat transfer, whether for cooling, heating, or condensing fluids. Using the wrong type may result in poor performance or even system failure.
For example, in industries such as petrochemicals or power generation, the incorrect Heat exchanger type might cause corrosion, scaling, or decreased thermal efficiency. Understanding the definition of Heat exchanger type allows you to assure compatibility with your application, resulting in reliable performance and longer equipment life.
What Is A Heat Exchanger?
A heat exchanger is a system used to efficiently transfer heat between a source and a working fluid. It typically comprises a set of tubes or plates that enable one substance, such as a fluid or gas, to pass over or through another substance, facilitating the exchange of thermal energy. These devices play a crucial role in both cooling and heating processes.
Allowing precise temperature control for various applications in industries such as heating or cooling liquids and air conditioning. The design of heat exchangers ensures that the substances involved do not mix while optimizing the transfer of heat, making them essential components in diverse industrial settings.
What Are Some Heat Exchanger type??
1. Finned Tube Heat Exchanger Or Air Cooled Heat Exchanger
A finned tube heat exchanger, also known as an air-cooled heat exchanger, operates by transferring heat between a fluid (such as water or oil) flowing inside tubes and the surrounding air. The tubes have fins that increase the surface area, enhancing heat exchange efficiency through improved convective heat transfer.
This type is particularly useful in applications where limited water availability or environmental factors restrict the use of water-cooled systems. Air-cooled heat exchangers find extensive use in industrial settings, power plant, and HVAC systems. The following table summarizes the advantages and disadvantages of this type.
Advantages |
Disadvantages |
Effective in water-scarce environments | Reduced efficiency compared to water-cooled systems |
Suitable for remote or outdoor locations | Noise generated by fans can be a concern |
Minimal water consumption | Performance affected by ambient temperature fluctuations |
2. Shell And Tube Heat Exchanger
The shell and tube heat exchanger is a versatile and widely used design, consisting of a shell (pressure vessel) with a bundle of tubes inside. The two fluids exchange heat—one flows inside the tubes and the other flows over the outside.
This type effectively serves applications that require high thermal performance and commonly appears in industrial processes, power generation, and HVAC systems. Shell and tube heat exchanger are suitable for high-pressure and high-temperature operations. The table below outlines the advantages and disadvantages
Advantages |
Disadvantages |
Efficient heat transfer | More complex design compared to other types |
Suitable for high-pressure applications | Slower response to sudden temperature changes |
Resistant to thermal and mechanical stress | Higher initial costs |
3. Plate Heat Exchanger Or Gasket Plate Heat Exchanger
Plate heat exchanger, or gasket plate heat exchanger, consist of stacked plates with small channels through which fluids flow. The compact design allows for efficient heat transfer in a relatively small footprint.
This type is ideal for applications with space constraints or those requiring quick temperature adjustments. Plate heat exchangers are commonly used in the food and beverage industry, HVAC systems, and chemical processing. The advantages and disadvantages are summarized in the following table.
Advantages |
Disadvantages |
Compact and lightweight design | Limited to moderate pressure applications |
Quick response to temperature changes | Susceptible to fouling and clogging |
Energy-efficient and easy to maintain | Higher sensitivity to particulate matter in fluids |
Knowing heat exchanger from various perspectives is crucial for making informed decisions in your industrial applications. Understanding the different types, their advantages, and their limitations allows you to tailor your choice to specific operational requirements.
Whether it’s the efficiency of a shell and tube heat exchanger, the compact design of a plate heat exchanger, or the specialized applications of finned tube heat exchanger, a comprehensive knowledge base ensures you can make the optimal selection and achieve peak performance.
For you, seeking to deepen your expertise in the design and maintenance of heat exchanger, specialized training can be invaluable. Consider enrolling in Shell and Tube Heat Exchanger training by PetroSync that adheres to ASME and TEMA standards.
Our training provides in-depth insights into the intricacies of these heat exchanger, covering design principles, operational considerations, and maintenance practices. Equip yourself with the skills needed to navigate the complexities of heat exchanger systems and contribute to the efficient and safe operation of your industrial processes.
What are the 4 main types of plate type heat exchanger?
Plate heat exchangers are well-known for their small footprint and high thermal efficiency. These are divided into four major categories, each ideal for a certain application:
1. Gasketed Plate Heat Exchanger
This is one of the most popular heat exchanger kinds, with plates separated by gaskets for easy maintenance. They are extensively used in HVAC systems and industries that demand frequent cleaning.
2. Brazed Plate Heat Exchanger
This small and durable solution is permanently sealed, making it ideal for refrigeration and hydronic heating systems. Its robust design lowers leakage concerns, distinguishing it from other heat exchanger type.
3. Welded Plate Heat Exchanger
For high-pressure and high-temperature environments, this type stands out among heat exchanger type, offering unmatched durability in industrial processes.
4. Semi-Welded Plate Heat Exchanger
Combining features of gasketed and welded designs, these heat exchanger type are suitable for handling aggressive chemicals or high-pressure fluids.
Understanding these options ensures you choose the right heat exchanger type to match your system’s needs and demands.
What 3 types of material are heat exchanger made of?
Heat exchanger type are also distinguished by the materials used in their manufacture. The material choice has a direct impact on durability, efficiency, and compatibility with diverse applications :
1. Stainless Steel
Stainless steel is one of the most lasting heat exchanger materials, having excellent corrosion resistance and strength. This material is appropriate for businesses requiring strict cleanliness standards, such as food processing and pharmaceuticals.
2. Aluminum
Aluminum, being lightweight and thermally conductive, stands out as a heat exchanger material for applications requiring rapid heat transmission. It is widely used in the automobile and aerospace industries.
3. Copper
Copper’s high thermal conductivity makes it an appropriate material for some types of heat exchanger, particularly in HVAC systems and electronics cooling. However, it is not as corrosion-resistant as stainless steel.
Choosing the right material ensures that your Heat exchanger type are appropriate for the work environment while also enhancing performance.
What are the three types of flow in a heat exchanger?
Heat exchanger type use a variety of flow arrangements, each with substantial advantages for heat transfer efficiency :
1. Counterflow
Counterflow designs, in which hot and cold fluids flow in opposite directions, are among the most efficient forms of heat exchangers.
2. Parallel Flow
This design is simpler than other heat exchanger types since both fluids flow in the same direction. Although less efficient, it is appropriate for applications like as air conditioning.
3. Crossflow
This flow pattern, which is typically found in air-cooled heat exchanger, allows fluids to move perpendicular to one another. It is small and extremely effective in cooling gasses.
By understanding these flow arrangements, you can select the heat exchanger type best suited to your system’s specific requirements.
Join PetroSync Training for Professional Growth in Engineering
Heat exchanger type are a cornerstone of engineering systems, and mastering them can elevate your career. PetroSync provides personalized training programs for professionals in areas such as oil and gas, petrochemicals, and energy.
PetroSync focuses on practical learning, covering everything from heat exchanger type definitions to advanced design and maintenance procedures. Joining PetroSync will provide you with the knowledge and experience you need to boldly face complicated issues.
Improve your abilities with PetroSync’s comprehensive training. Begin today by exploring the world of heat exchanger type to stay ahead in your field.
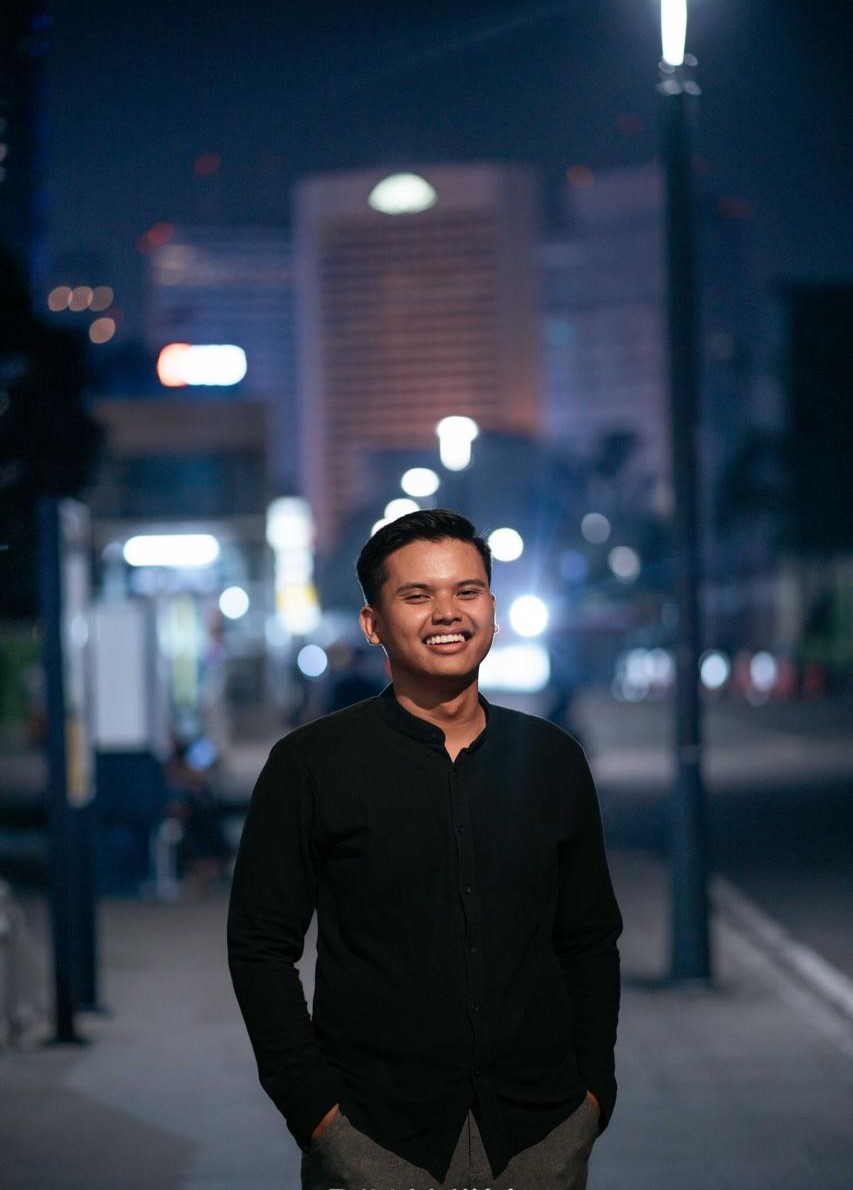
Results-oriented and thorough SEO specialist with extensive experience in conducting keyword research, developing and implementing digital website promotion strategies and plans, managing campaigns to develop company websites in the digital world, excellent knowledge of marketing techniques and principles, and attentive strong attention to detail.