Are you exploring the intricacies of shell and tube heat exchangers types in our guide? This resource provides a comprehensive overview of these crucial heat-exchanging devices. Whether you are new to heat exchangers or seeking a deeper understanding, this guide equips you with essential knowledge for selecting and maintaining these vital industrial components.
What Is Shell and Tube Heat Exchangers?
A shell and tube heat exchanger, as its name implies, consists of a shell (a large pressure vessel) with a bundle of tubes inside it. This device is utilized to transfer heat between two different fluids. One fluid flows through the tubes (tube side), while the other flows over the outside of the tubes (shell side).
The cylindrical shell and tube configuration enhances the efficiency of heat exchange, making it a widely used solution for both cooling and heating processes in various industrial applications.
The three most common types of shell-and-tube exchangers are (1) fixed tube sheet design, (2) U-tube design, and (3) floating-head type. Each design has its specific advantages and applications.
Fixed tubesheet exchangers are simple and cost-effective, u-tube exchangers allow for thermal expansion and contraction, while floating-head exchangers facilitate tube bundle removal for maintenance. Understanding these design variations is crucial for selecting the most suitable shell and tube heat exchanger for specific industrial requirements.
What Are The Types of Shell and Tube Heat Exchangers?
The three primary types of shell-and-tube exchangers include fixed tubesheet, U-tube, and floating-head designs, each with unique advantages and applications.
1. Fixed Tube
The fixed tube heat exchanger is a cost-effective solution with a straightforward design. In this type, the shell and tube sheet are welded together, preventing the removal of the tube bundle. Maintenance is simplified as the straight tubes can be easily cleaned with a brush or rod, though the shell side requires chemical cleaning or manual pressure washing.
While fixed tubes are suitable for many applications and remain a popular choice, they come with limitations. The fixed joint between the tube and shell may lead to challenges in dealing with temperature differences between them, requiring the incorporation of expansion bellows on the shell side. The advantages and disadvantages of fixed tube heat exchangers are summarized in the following table:
Advantages | Disadvantages |
– Cost-effective | – Limited thermal expansion |
– Simple maintenance with straight tubes | – Shell side requires chemical cleaning |
– Can be effective with a differences tailored design | – Potential for failure under temperature |
2. U-Tube
U-tube heat exchangers offer a design where the tubes are not connected with any fixed joint, allowing them to expand freely within the shell. This design eliminates the need for expansion bellows, simplifying the thermal expansion challenge.
However, U-tubes face limitations, particularly regarding temperature differences. They are suitable for applications with smaller temperature differentials, as larger differences may cause tube sheet warping. Mechanical cleaning technology advancements have addressed historical cleaning challenges, making U-tube heat exchangers more viable. The advantages and disadvantages are outlined in the following table:
Advantages | Disadvantages |
– Tubes can expand freely within the shell | – Limited suitability for large temperature |
– Mechanical cleaning technology advancements differences | – Tube sheet warping due to temperature differences |
– Can handle smaller temperature differences efficiency | – Reduced tubular surface area leading to lower |
3. Floating Head.
The floating head heat exchanger is characterized by its ability to withdraw the tube bundle from the shell for separate inspection. This design facilitates comprehensive cleaning, allowing access to the shell side, tube side, and both inside and outside of the tubes.
Floating head heat exchangers are widely used in industries requiring frequent cleaning, such as oil and gas. While they offer cleaning advantages, they come with higher manufacturing costs compared to fixed tube and U-tube designs.
Additionally, in specific cases, the floating head design may require the installation of expansion bellows. The table below summarizes the advantages and disadvantages:
Advantages | Disadvantages |
– Bundle can be withdrawn for separate inspection | – Higher manufacturing costs |
– Comprehensive cleaning accessibility | – Potentially requires expansion bellows in specific cases |
– Standard in industries requiring frequent cleaning |
What Are The Types of Shell and Tube Heat Exchangers based on Process and Phase Change?
Like all heat exchangers, you can categorize them based on the processes they are in.
1. Coolers and Heaters
Coolers and heaters are heat exchangers involved in processes where a temperature change occurs without a phase change in the fluids. In these applications, the fluids, such as hot water on one side and cold water on the other, or hot air cooling cold air, undergo temperature alterations without transitioning between liquid and gas phases. The table below outlines the advantages and disadvantages of coolers and heaters:
Advantages | Disadvantages |
– Efficient temperature change | – Limited to processes without phase change |
– Versatile applications | – Not suitable for condensation processes |
2. Condensers
Condensers are designed for processes where the fluid undergoes a phase change, transitioning from a gas to a liquid. In applications like these, the primary goal is to facilitate condensation. An example is the condensation of steam into water. The table below summarizes the advantages and disadvantages of condensers:
Advantages | Disadvantages |
– Efficient phase change process | – Limited to processes involving condensation |
– Suitable for vapor recovery | – Not optimal for processes without phase change |
3. Reboilers
Reboilers are utilized in processes where there is a hot fluid (such as steam) that condenses on one side, while on the other side, a fluid boils off. This means that liquid is introduced at one end, and at the other end, there is either 100% vapor (as in a kettle reboiler) or a vapor/liquid mixture (as in thermosyphon reboilers). The table below outlines the advantages and disadvantages of reboilers:
Advantages | Disadvantages |
– Facilitates vaporization | – Limited to processes involving vaporization |
– Common in distillation processes | – May require complex control systems |
Shell and tube heat exchangers play a crucial role in various industrial applications, facilitating efficient heat exchange between two fluids. Understanding the variations of these heat exchangers is vital for selecting the most suitable heat exchanger. Further, each type has specific advantages and limitations, ensuring suitability for diverse applications.
If you are seeking in-depth knowledge and skills in shell and tube heat exchangers, PetroSync offers training programs compliant with ASME/TEMA standards. Our shell and tube heat exchangers training covers proper design, maintenance, and operational aspects, providing valuable insights for professionals in the field. Investing in this training can enhance your understanding and expertise, improving efficiency and reliability in the operation of shell and tube heat exchangers.
Credit header image: iStock
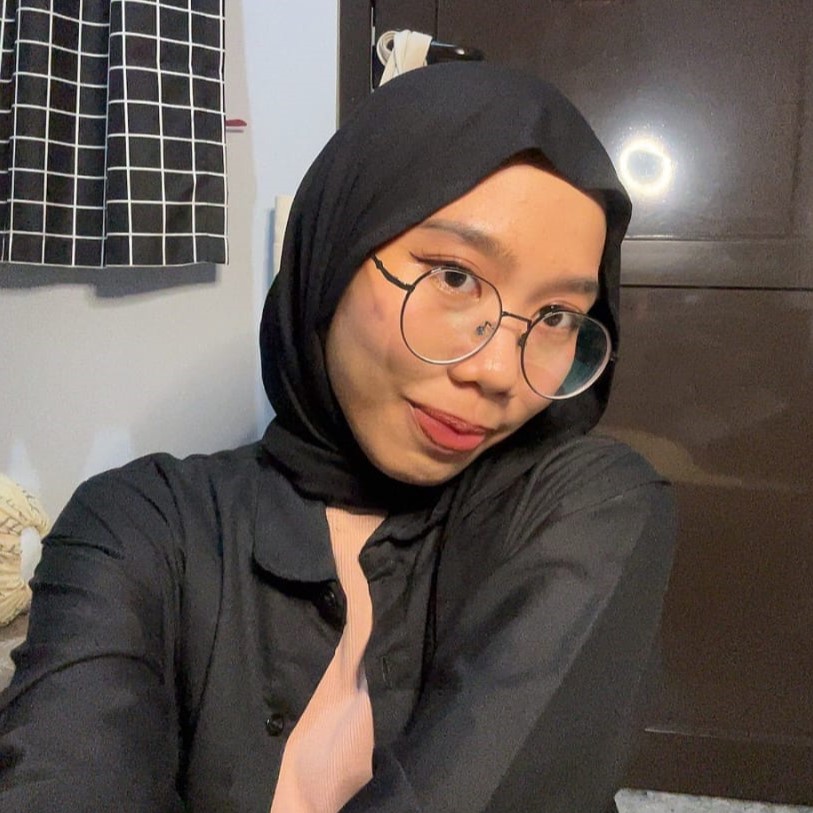
SEO specialist by day, fact-checker by night. An avid reader and content writer dedicated to delivering accurate and engaging articles through research and credible sources.