Pressure vessels are vital components in many industries, playing a crucial role in processes that involve storing and transporting gases and liquids under pressure. Ensuring the safety and integrity of these vessels is vital to prevent accidents, injuries, and environmental damage. In this article, we will explore the Pressure Vessel Inspection Requirement for Industry Safety, providing valuable insights and guidelines for maintaining the highest safety standards.
What Is Pressure Vessel Inspection?
Pressure vessel inspections are comprehensive checks that evaluate the vessel’s condition, whether from the outside, inside, or both. These inspections, guided by regulations like ASME Section VIII and API 510, require a skilled inspector to:
- Visually examine the vessel to assess its overall condition, looking closely at details like insulation, welds, joints, and structural connections.
- Measure the thickness of the vessel’s walls to monitor any changes that may have occurred over time due to use.
- Analyze the stress the vessel is under to ensure it remains safe for its intended purpose.
- Inspect the pressure release valves to confirm they are in proper working order.
- Conduct a hydrostatic pressure test, which helps ensure the integrity and safety of the vessel. These inspections play a crucial role in maintaining the reliability and safety of pressure vessels in various industries.
What Is Pressure Vessel Inspection Requirement?
While safety standards for pressure vessels can differ by country, some basic expectations apply to most pressure vessels worldwide. Here are four types of checks and tests that pressure vessels need to go through to meet safety standards and regulations:
1. Post-Installation Inspection
After setting up a pressure vessel, inspecting it before use is essential. In general, below is the checklist for the post-installation inspection:
- Check that the nameplate information matches what the manufacturer provided and what the design requires.
- Ensure the equipment is put correctly, with suitable supports, secure ladders and platforms, correctly installed insulation, well-assembled connections, and a clean and dry vessel.
- Verify that the pressure-relief devices meet the design requirements, such as having the right device and set pressure, and that they’re correctly installed.
This inspection also gathers important starting information and takes initial thickness readings at specific points. It’s all about ensuring everything’s in good shape and safe to use.
2. Routine Check-Ups
Pressure vessels should undergo inspections at least every five years or even more frequently since inspections for pressure vessels need to happen at specific intervals. An RBI (Risk-Based Inspection) assessment can help determine when these inspections should occur.
- Sometimes, the RBI assessment might suggest that the usual inspection intervals can be extended. This includes inspections like the annual one or those related to the remaining life of the vessel.
- If the interval suggested by RBI goes beyond the usual annual limit, the engineer and inspector should review and approve it. They should do this at least once a year or more frequently if there are changes in the process, equipment, or potential consequences.
When extending the inspection interval based on an RBI assessment, it’s important to consider the vessel’s inspection history and whether the pressure-relieving device(s) could get clogged or fouled. This helps ensure the vessel stays safe and well-maintained.
3. Identifying Possible Issues
Regular visual inspections and tests help find any potential problems. External Inspections: Usually, these are carried out by an inspector, but in some cases, qualified personnel can do it if the inspector approves. Those who perform external inspections according to API 510 need the right training.
1. External inspections
External Inspections look at the vessel’s outside surface, insulation systems, paint and coatings, supports, associated structures, and more. They also check for things like leaks, hot spots, and vibrations, and make sure there’s enough room for the vessel to expand. They also make sure the vessel is properly aligned on its supports. During this inspection, special attention is given to the welds used to attach various components for any signs of cracking or defects.
2. Further Investigation
If any leaks are noticed, they need to be investigated to figure out where they’re coming from. Weep holes in reinforcing plates should stay open because they help show if there’s a leak and prevent pressure from building up behind the plate.
3. Looking for Distortion
Inspectors also check for signs of bulging, out-of-roundness, sagging, or distortion in the vessel. If they suspect or see any distortion, they measure the vessel to figure out how extensive the distortion is.
4. API 572 standard
For more detailed guidance on pressure vessel inspection requirement, it’s a good idea to refer to the API 572 standard.
5. Reporting Issues
If anyone notices that a vessel is deteriorating, they should report it to the inspector. It’s all about keeping a close eye on the vessel’s condition.
4. Stress and Pressure Tests
Specialized tests are sometimes necessary to ensure the vessel’s integrity. Regular testing is crucial to ensure that a pressure vessel operates safely, mainly because these vessels often contain flammable materials like compressed natural gas, fuel oil, or liquefied hydrogen. It’s all about keeping things safe:
- The minimum test pressure should align with the rules of the rating code, which is used to determine the Maximum Allowable Working Pressure (MAWP).
- If a vessel has been rerated using the design allowable stress from the 1999 addendum or later of ASME Section VIII: Division I, Code Case 2290, or Code Case 2278, the minimum test pressure should be set at 130% of the MAWP and adjusted for temperature.
- For vessels that have been rerated using the design allowable stress from ASME Section VIII: Division 1, published before the 1999 addendum, the minimum test pressure should be 150% of the MAWP, also adjusted for temperature.
- Pressure tests aren’t usually done during regular inspections. Instead, they typically happen when there are changes made to the vessel. If there have been repairs, a pressure test might be needed, but other options are mentioned in section 5.8.7 if a pressure test isn’t suitable.
- For vessels originally designed using ASME Section VIII: Division I, the minimum test pressure should be determined as follows:

These recommendations ensure that pressure vessel inspections are conducted with the appropriate test pressures in line with industry standards.
What Are The Consequences of Improper Pressure Vessel Inspections?
Suppose a company or manufacturer fails to perform pressure vessel inspections properly. In that case, it can lead to various potentially catastrophic consequences, particularly in industries like refineries or chemical plants where pressure vessels play a vital role.
1. Safety Risk
Inadequate inspections can fail pressure vessels, leading to leaks or even explosions. These incidents can cause severe injuries or fatalities to personnel working in the vicinity.
For example, a pressure vessel in a chemical plant that has not been thoroughly inspected might develop undetected cracks, leading to a sudden rupture that releases toxic chemicals into the environment, endangering the safety of workers and the surrounding community.
2. Environmental Hazards
Improperly inspected pressure vessels can result in environmental pollution. For instance, a faulty container in a refinery may leak hazardous chemicals, causing soil and water contamination. Such incidents can lead to costly cleanup operations and legal liabilities.
3. Financial Loss
Pressure vessel failures due to inadequate inspections can result in costly downtime, repair, or replacement. Moreover, it may lead to legal actions, fines, and damage to a company’s reputation, causing financial losses.
4. Regulatory Compliance
Companies that fail to conduct proper pressure vessel inspections can also face regulatory penalties and legal consequences. Regulatory authorities require strict adherence to inspection standards to ensure the safety of workers and the environment.
In summary, proper pressure vessel inspections are crucial for ensuring the safety of workers, protecting the environment, preventing financial losses, and maintaining compliance with regulations. Neglecting these inspections can have severe consequences, both in terms of safety and financial implications, especially in high-risk industries like refineries and chemical plants.
Pressure vessel inspection requirement is paramount to ensure safety, environmental protection, and regulatory compliance in industries such as refineries and chemical plants. These requirements encompass thorough examinations of pressure vessels, including visual inspections, measurement of wall thickness, analysis of stress levels, and pressure release valve assessments. Neglecting these inspections can lead to catastrophic consequences, including safety risks, environmental hazards, financial losses, and legal penalties.
To perform proper and thorough pressure vessel inspections, it is highly recommended for you to consider API 510 training. This training equips inspectors and professionals with the essential knowledge and skills required to carry out inspections effectively and in adherence to industry standards.
API 510 training covers various aspects of pressure vessel inspection, including examination techniques, understanding design codes, and safety protocols. By taking API 510 training, you can contribute to the safety and integrity of pressure vessels within your respective industries, ensuring that inspections are conducted to uphold the highest safety standards.
Credit: istockphoto
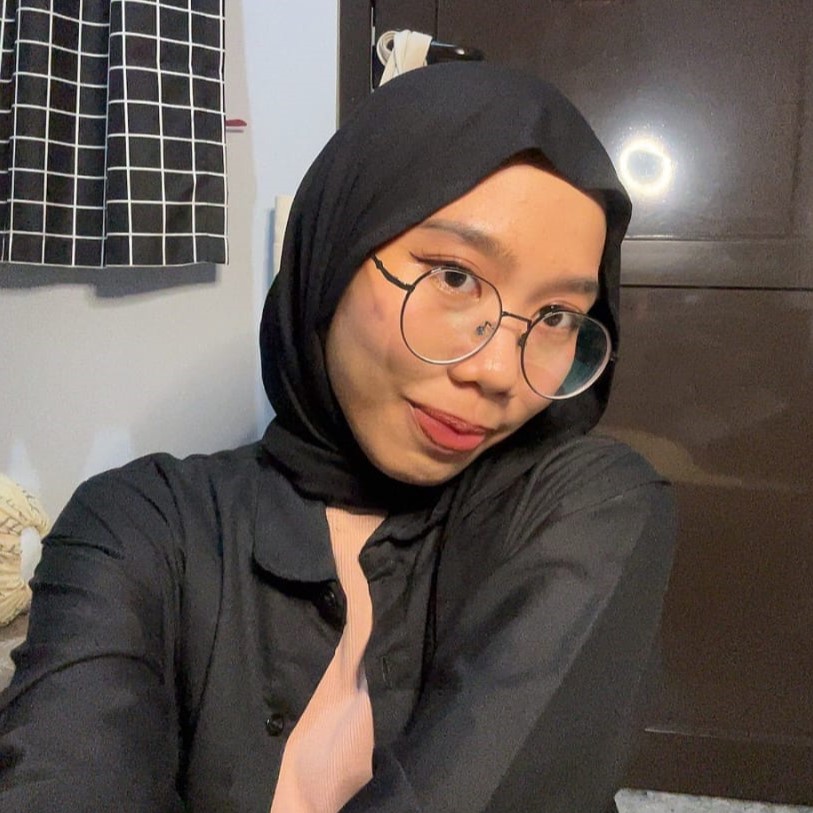
SEO specialist by day, fact-checker by night. An avid reader and content writer dedicated to delivering accurate and engaging articles through research and credible sources.