Metallurgy, the science of working with metals, plays a significant role in shaping our world. This knowledge becomes the key to creating things we use daily, like buildings and electronics. Industries worldwide rely on metallurgy to make strong and versatile materials. Read on to learn more about metallurgy and why it is so important in the industrial world.
What Is Metallurgy?
Metallurgy is a branch of material science and engineering that studies the physical and chemical properties of metal. It comprises evaluating the properties of current materials and determining how they might be combined to create new materials. This technology is incredibly useful in numerous industries, including healthcare, transportation, defense, and entertainment.
It generates and refines metals for a wide range of purposes. Metallurgy is the application of science and technology to metal. It comprises using scientific knowledge to fabricate metals and develop metal components for a wide range of consumer and industrial applications. It is critical to understand that metallurgy and metalworking are not interchangeable.
Just as medical science and practice are not. Metalworking, like medicine, relies on scientific advancements for technological advancement. Metallurgists are professionals that specialize in metallurgy.
What Does Modern Metallurgy Focus On?
Modern metallurgists focus on understanding and enhancing the properties of metals, ensuring they meet the high standards required in industries like construction, technology, and manufacturing. This branch of science is dedicated to making sure the metals we use are not just strong, but also smart and tailored to suit the needs of various applications. In general, there are two studies of metal.
1. Ferrous
Ferrous metallurgy focuses on metals containing iron, primarily iron and steel. These metals are known for their strength and durability, making them essential in industries like construction, automotive manufacturing, and heavy machinery.
2. Non-Ferrous Metallurgy
Conversely, non-ferrous metallurgy focuses on metals that lack iron, such as copper, and aluminium, and precious metals like gold and silver. People favor these materials for their lightweight properties, electrical conductivity, and corrosion resistance, making them ideal for applications in electronics, aerospace, and jewelry-making, among others.
A grasp of non-ferrous metallurgy is pivotal for producing a diverse range of items, from electronic components to aircraft parts, and for crafting intricate and valuable pieces like jewellery. Both ferrous and non-ferrous metallurgy play vital roles in modern technology and production processes, each with its unique contributions to various industries.
What Are The Key Aspects of Metallurgy?
They key aspects of metallurgy can be classified into two: extractive metallurgy and physical metallurgy.
1. Extractive Metallurgy
This aspect focuses on the extraction of metals from ores or other forms, followed by processes to refine and purify these metals. It involves two common following techniques:
Pyrometallurgy
This is a fundamental branch of extractive metallurgy that involves using heat, or thermal treatment, to extract metals from their ore or mineral forms. During pyrometallurgical processes, applying high temperatures triggers physical and chemical transformations in the materials, allowing for the separation and extraction of metals.
Standard pyrometallurgical techniques include roasting, where they heat ores in the presence of air to remove impurities, and smelting, which melts the ore to extract the metal and refine it further.
Hydrometallurgy
In contrast, hydrometallurgy employs water-based processes for the extraction and purification of metals from ores or other compounds. This method is particularly useful for metals that may not respond well to high-temperature treatments. Hydrometallurgical techniques include leaching.
Metals are extracted using a suitable solvent, followed by the precipitation of insoluble compounds to separate metals and pressure reduction processes. Hydrometallurgy commonly extracts metals like gold, copper, and uranium because it provides efficient and environmentally friendly methods for metal recovery.
2. Physical Metallurgy
Physical metallurgy deals with the science of shaping and enhancing metallic materials. It delves into the study of metallic crystal structures, mechanical properties, electrical and magnetic properties, and chemical properties of metals. Key elements within physical metallurgy include:
- Powder metallurgy, which involves creating materials or components from metal powders, and
- Alloying or known as the process of mixing different elements to enhance the properties of metals.
These key aspects of metallurgy are vital for understanding how scientists source, process, and transform metals into materials with diverse properties and applications in various industries.
What are Metallurgy Products?
Metallurgical goods are frequently utilized and highly valued in practically every industry. Metallurgy is the process of refining metals to produce a range of products, each designed for a specific application. This method is extremely important in industries such as oil and gas, because it produces materials that are both long-lasting and resistant to corrosion.
Some popular metallurgical goods include:
1. Metal Alloys:
Alloys are combinations of two or more metals designed to combine their qualities. Steel, an iron-carbon alloy, is extensively used in the building, manufacturing, and oil and gas industries due to its high strength and adaptability. Engineers use other alloys, such as titanium alloys, in aerospace and oil and gas applications that demand high strength and resistance to heat and corrosion.
2. Plates, Sheets, and Foils:
These thin, flat items constructed of various metals are commonly utilized in manufacturing, construction, and transportation. Metal sheets, for example, are utilized in the structural frames of oil and gas platforms to endure heavy weights and harsh weather.
3. Pipes and Tubes:
Metallurgy plays a crucial role in the production of pipes and tubes for sectors like oil and gas, where materials must withstand corrosion and high-pressure conditions. Stainless steel pipes are frequently used to carry oil, gas, and chemicals, while specialized alloys are utilized in deep-sea drilling and pipelines exposed to corrosive environments.
4. Castings:
Metals can also be poured into molds to form intricate designs. Casting is a standard method for manufacturing engine blocks, turbines, and valves. Castings are critical in the oil and gas industry for generating long-lasting equipment capable of withstanding high-stress conditions.
5. Welding and Joining Materials:
Metallurgy also involves the creation of materials for welding and connecting metals. This is critical for constructing and maintaining pipelines, offshore platforms, and refineries in the oil and gas industry. Metallurgical improvements have resulted in the creation of stronger welding rods and joining procedures, ensuring long-lasting, leak-free seals in crucial equipment.
What Processes Are Involved in Metallurgy Production?
The production of metals involves a series of carefully designed steps to transform raw materials into the sturdy and versatile materials we use in our daily lives. Metallurgy production processes encompass activities like extracting metals from ores, refining them, and shaping them into useful forms.
These structured procedures ensure that the metals meet specific quality standards and are ready for application in a wide range of industries.
1. Metalworking Processes
These processes involve shaping, cutting, and joining metals to create various components and products. Metalworking includes techniques such as forging, welding, and machining.
2. Heat Treatment
Heat treatment processes alter the physical and mechanical properties of metals by subjecting them to controlled heating and cooling. This helps enhance their hardness, toughness, and other characteristics.
3. Plating
Plating involves applying a layer of one metal onto the surface of another. This process enhances the appearance, corrosion resistance, and durability of metal objects.
4. Shot Peening
Shot peening improves the fatigue life and durability of metal components by bombarding them with tiny metal pellets or “shots.”
5. Thermal Spraying
Thermal spraying involves melting metal or ceramic materials and spraying them onto surfaces to create protective coatings or restore worn parts.
6. Surface Treatment
Surface treatments aim to modify the outer layer of metals, often to improve corrosion resistance or adhesion for paint or other coatings.
These processes collectively produce various metal components and products, catering to various industries and applications.
Metallurgy is a fundamental knowledge base that provides a crucial foundation for standards like API 571. This standard, dedicated to addressing damage mechanisms in the refining and petrochemical industries, heavily relies on metallurgical principles.
Understanding metallurgy is essential if you are an engineer. It equips you with the expertise to comprehensively assess how materials behave under varying operational conditions. This knowledge helps identify risks, assess equipment integrity, and make informed decisions to ensure safety and reliability.
Join PetroSync Training: Enhance Your Skills for Success
PetroSync offers comprehensive API 571 training tailored to equip you with the specialized knowledge and skills required to navigate API 571 course. Our training course provides in-depth insights into metallurgy, giving you the fundamental knowledge to thoroughly assess equipment integrity, identify damage mechanisms, and apply effective mitigation strategies.
By bridging the gap between metallurgical knowledge and the practical application of API standards, PetroSync empowers you to enhance the safety, reliability, and efficiency of equipment and processes in the refining and petrochemical industries.
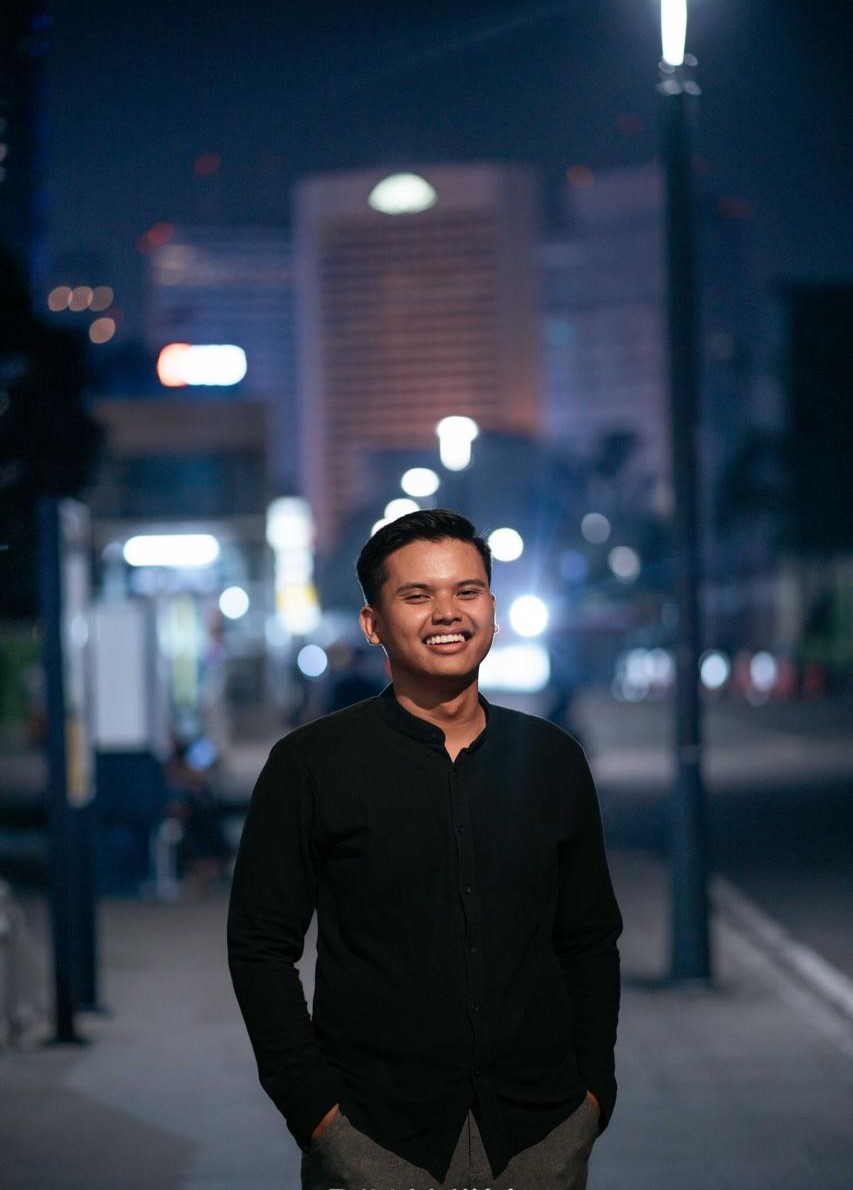
Results-oriented and thorough SEO specialist with extensive experience in conducting keyword research, developing and implementing digital website promotion strategies and plans, managing campaigns to develop company websites in the digital world, excellent knowledge of marketing techniques and principles, and attentive strong attention to detail.