In today’s industry, where high temperatures and challenging conditions are frequent, Refractory Materials are vital. They play a crucial role in ensuring the smooth operation of various applications, from metallurgy to petrochemicals. In this detailed guide, we’ll delve into the world of refractory materials, exploring their types, applications, and maintenance, emphasizing their importance in modern manufacturing.
What Are Refractory Materials?
In the field of materials science, a refractory, also known as refractory materials, refers to a substance that can withstand high temperatures, pressure, and chemical exposure without breaking down. It maintains its strength and shape even when exposed to extreme heat.
Refractories are typically made up of various materials, including oxides, carbides, and nitrides. They are characterized as polycrystalline, polyphase, inorganic, non-metallic, porous, and heterogeneous. These materials often contain elements such as silicon, aluminum, magnesium, calcium, boron, chromium, and zirconium.
Refractory materials are employed to make protective linings for really hot furnaces, kilns, and reactors. These linings act as shields, safeguarding nearby machinery and structures from very high heat, chemical reactions, and damage.
What Are The Types of Refractory Materials in The Industry?
Refractory materials come in various forms to suit different industrial needs. Some common types of refractory based on their chemical composition, include:
1. Fireclay Refractories
Made primarily of clay minerals, these are versatile and can withstand moderate temperatures.
2. Silica Refractories
Composed of pure silica, silica refractories excel in resisting acidic environments. This type of refractory can handle extreme heat changes, resist melting substances and slag, and is very durable. They are commonly used in the iron and steel industry for furnace construction.
3. Magnesia Refractories
Comprising magnesium oxide, these are ideal for high-temperature applications, particularly in the steel industry. They can withstand lime and iron-rich slags well, are tough against wear and corrosion, and remain highly heat-resistant when under pressure.
4. Chrome-Magnesia Refractories
Combining chrome and magnesia properties, these offer durability and resistance to corrosive materials. These refractories can withstand very high heat and are quite resilient in harsh, corrosive surroundings.
5. Carbon Refractories
Made from carbonaceous materials, they are suitable for extreme temperatures and chemical resistance. Primarily composed of carbon, these refractories are frequently employed in extremely low-oxygen settings. Their high heat resistance provides exceptional thermal stability and resistance to melting substances.
5. Monolithic Refractories
Monolithic refractories are specialized materials used in high-temperature applications. Unlike traditional bricks or shapes, they come as a single, unified structure and can be easily installed. These materials are commonly used to line furnaces, kilns, and other industrial equipment to withstand extreme heat and harsh conditions.
Monolithic refractories offer several advantages over traditional refractory materials. They are easier to install, as they come in a ready-to-use form, reducing both installation time and labor costs. Additionally, monolithic refractories can be customized to fit specific shapes, reducing the number of joints and seams in the lining, which can weaken it.
The customization of monolithic refractories enhances their performance. They also provide improved thermal efficiency due to their continuous structure, resulting in better energy efficiency and reduced heat loss. Furthermore, they often exhibit better resistance to thermal shock, making them suitable for applications with rapid temperature changes.
Their versatility, high purity options, and lower maintenance requirements make monolithic refractories a preferred choice in various high-temperature industries, where durability and performance are critical. The inspection of monolithic refractories is regulated under API 936.
How Are The Applications of Refractory Materials in The Industries?
Refractory materials find widespread use across various industries:
1. Refineries & Petrochemical Industry
In the petrochemical sector, refractories line cracking units and reactors used in the production of various chemicals and fuels. Refractory materials are essential as they line the hot equipment used for processes like oil refining and chemical reactions, protecting them from extreme heat and harsh chemicals.
2. Power Plants
In power plants, refractories line boilers and furnaces where fuel burns to produce electricity. These linings endure intense heat, helping maintain stable temperatures for efficient energy generation.
3. Chemical Plants
Refractory materials play a vital role in chemical plants where high-temperature chemical reactions occur. They line vessels and reactors, shielding them from corrosive chemicals and maintaining the required heat for reactions.
4. Cement Plants
In cement manufacturing, refractories line kilns that operate at very high temperatures to make clinker. These materials ensure the durability of the kiln lining and efficient cement production.
5. Aluminium and Steel Industries
In steelmaking, refractories line furnaces and ladles used to melt and refine steel. Their ability to withstand high temperatures and chemical reactions is crucial for equipment integrity.
How To Perform Maintenance of Refractory Materials?
Proper maintenance is essential to extend the lifespan of refractory linings. This includes regular inspections, repairs, and the use of suitable coatings or patching materials to address any damage or erosion. Neglecting maintenance can result in costly downtime and reduced operational efficiency. Maintenance for refractories based on API 936 involves specific steps:
1. General Maintenance
For general maintenance, API 936 standards give guidance as follows:
- All repair materials and methods must be approved by the owner before any work begins.
- Before adding new refractory material, clean the adjacent sound refractory material, making it free of debris, roughened, and thoroughly wet with water, curing compound, or weak phosphoric acid.
- Clean anchors and shells from any debris, and replace anchor leg coverings where necessary.
- If anchors or attachment welds are damaged, they should be replaced following the original installation.
2. Monolithic Lining
For monolithic lining repair, API 936 standards give guidance as follows:
- Remove unacceptable refractory lining perpendicular to the shell and horizontally to the acceptable lining without damaging the shell.
- The repair area should expose at least one anchor. If not, a new anchor should be installed. The removed area should be large enough to expose three separate anchors.
- Ensure that corners have smooth, rounded contours throughout the refractory depth.
- For repairing surface bubble defects, use a phosphate-bonded castable. Avoid using metal fibers in this type of repair, and make sure the surface is level with the adjacent refractory surface.
3. Thin Erosion-resistant Lining
Meanwhile, for thin erosion-resistant lining, you can refer to the following suggestions:
- Defective refractory in a hex metal lining requires the complete removal and replacement of all affected biscuits.
- Repairing defective areas in a hexalt lining should follow the guidelines set in 9.14.2.2 of the API 936 standard.
What Are Some FAQs Regarding Refractory Materials?
1. How Long Do Refractory Materials Typically Last?
The lifespan of refractory materials varies depending on factors such as the type of material, operating conditions, and maintenance. Well-maintained refractories can generally last several years in high-temperature environments.
2. Can Refractory Materials Be Recycled?
Yes, some refractory materials, especially those with high alumina content, can be recycled. Recycling helps reduce waste and environmental impact.
3. Are There Any Eco-Friendly Refractory Materials Available?
Efforts are ongoing to develop eco-friendly refractory materials with reduced environmental impact. Some options include alumina-silica materials and refractories made from recycled materials.
4. What Is The Role of Refractory Materials in Energy Conservation?
Refractory materials contribute to energy conservation by efficiently insulating high-temperature equipment, reducing heat loss, and optimizing energy use in industrial processes.
5. Are There Any Safety Precautions When Working With Refractory Materials?
Yes, working with refractory materials requires safety measures, including proper ventilation, the use of protective gear, and training in handling and installation.
Q: Can Refractory Materials be Repaired, or Do They Need To Be Replaced Entirely?
Refractory materials can often be repaired through patching or coating, extending their lifespan. However, extensive damage may require replacement to ensure safety and efficiency.
Refractory materials play a crucial role in high-temperature industries like steelmaking, glass production, cement manufacturing, and chemical processing. They can endure harsh conditions, ensuring these industries run smoothly. Learning about the different types, uses, and care of refractory materials provides a deeper understanding of how these materials support essential industrial processes.
PetroSync recognizes the vital role of trained inspectors in preserving the integrity of refractory materials in industrial settings. Our API 936 refractory training program equips you with the expertise to assess and maintain refractory linings effectively. Covering topics such as refractory identification, properties, and safety protocols, our training ensures inspectors can identify wear, damage, or degradation, contributing to the reliability and efficiency of various industries.
By enrolling in PetroSync’s API 936 training, you can improve your expertise, ensuring the continued success of high-temperature industrial processes.
Credit header image: Freepik
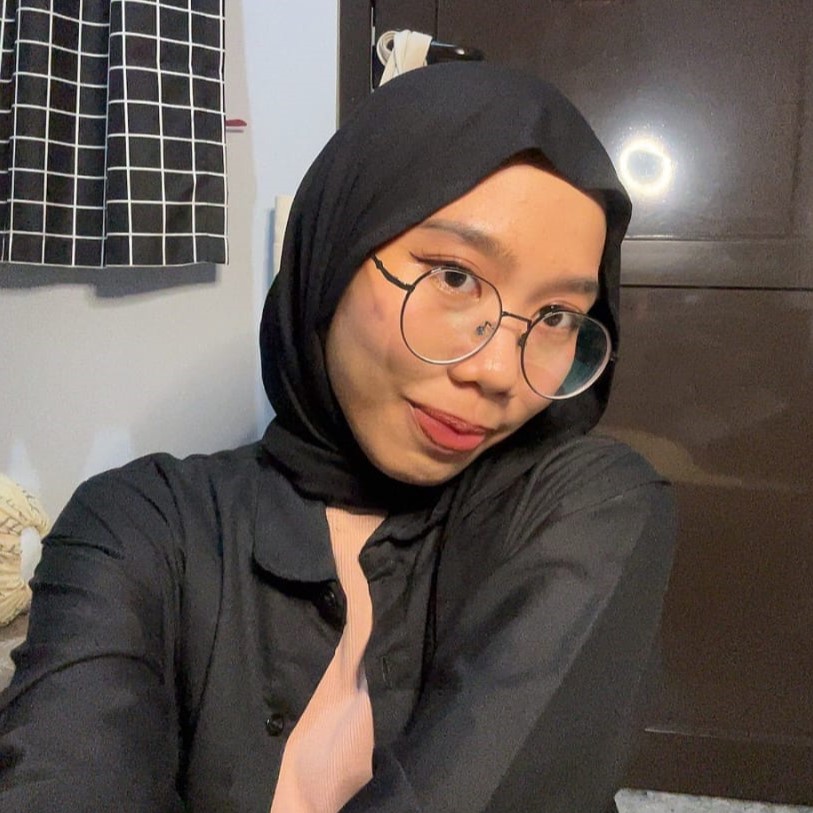
SEO specialist by day, fact-checker by night. An avid reader and content writer dedicated to delivering accurate and engaging articles through research and credible sources.