As one of the oldest standards-developing organizations, ASME is concerned with the importance of pressure equipment fitness in supporting industrial activities. One of ASME’s widely recognized standards is ASME PCC-2 discussing how repaired equipment meets the safety and performance criteria. After extensive research involving subject-matter experts and equipment manufacturers, existed to solve the pressure equipment.
What is ASME PCC?
The ASME Post Construction Committee (PCC), a division of the American Society of Mechanical Engineers, establishes standardized procedures for repairing, inspecting, and modifying pressure-containing equipment that has been in service. These standards, which are commonly used in industries such as oil and gas, petrochemicals, and energy.
Ensure that repairs preserve the original design integrity and extend the equipment’s operating lifespan. Within this framework, PCC-1 specifies standards for “Pressure Boundary Bolted Flange Joint Assembly,” which address the critical bolting and sealing of joints to prevent leaks and ensure operational safety.
Companies that adhere to both PCC-1 and PCC-2 standards can reduce the risk of equipment failure, meet regulatory requirements, and enhance the safety, dependability, and performance of their assets.
What does ASME PCC-2 stand for?
ASME PCC-2, or “Repair of Pressure Equipment and Piping,” is a standard developed by the American Society of Mechanical Engineers (ASME). It provides detailed methods for repairing equipment and piping that fall under the ASME Pressure Technology Codes and Standards after the equipment has been put into service.
This standard describes both temporary and permanent repair procedures, such as welding, mechanical clamps, and the use of composite materials. PCC-2 is critical in industries like oil and gas, where pressure-containing equipment operates in extreme conditions. Companies who adhere to these standards ensure that repairs are completed safely, efficiently.
Compliance with the equipment’s operational and design specifications. This not only extends the equipment’s life, but also lowers the risk of failure, ensuring safe and dependable operations.
What Is ASME PCC-2 Repair of Pressure Equipment?
ASME PCC-2 is a standard that provides guidelines for repairing pressure equipment, heat exchanger, piping, pipelines, and all related mechanics included under ASME Pressure Technology Codes and Standards once the equipment is in operation. The PCC-2 covers design, fabrication, inspection, and testing practices, either temporary or permanent, depending on the circumstance.
The standard applies when an inspection and flaw assessment indicate that equipment requires repair. Though ASME PCC-2 is a thorough standard, it does not address inspection and flaw evaluation procedures. The related inspection and flaw assessment information exists in the other ASME standard. As stated in the official document.
ASME PCC-2 advises the standard is used for general purposes and may not be suitable for all applications. Engineers and subject-matter experts should determine the applicability of a specific method based on sound engineering practices and judgment.
What Are ASME PCC-2 Scope and Organizations?
The repair of pressure equipment components exists in the ASME PCC-2 standards, even though it does not contain all of the safety concerns that may arise from its usage. ASME PCC-2 consists of five parts:
- The first part applies to all articles in this standard while covering the scope, organization, and purpose.
- The next part discusses the repair methods involving metal deposits, such as welding, brazing, soldering, or other similar techniques.
- The third part regulates mechanical repairs, with or without using sealants, such as bolted clamps or fixtures, and covers all repair methods not included in Part 2 or 4.
- The fourth part modulates repairs with non-metallic materials, such as non-metallic liners and wraps, and bonding using epoxy or joining metallic components.
- The last part talks about testing and examination methods.
The scope of ASME PCC-2 only provides technical procedures and information while diminishing the administrative and policy requirements regarding inspection, documentation, and quality control. Thus, joining the ASME PCC-2 training course will help engineers thoroughly understand ASME PCC-2 and its limitations.
How Does ASME PCC-2 Regulate Welding Reparation?
Pressure equipment such as pressure vessels, steam boilers, autoclaves, pressure piping, and compressed air receivers are classified as high-risk plants due to their potential to cause severe injury and fatalities. Mishaps like explosions, fires, and toxic releases can happen if a company neglects the pressure equipment’s regular inspections, testing, and maintenance.
Such accidents amplify the importance of ASME PCC-2 application in the industry. Following the standardized regulation can extend the lifespan of pressure equipment and keep the environment safe. ASME PCC-2 gives detailed guidance on how the utilization of welding as a repair process is necessary. There are several types of repair welding to fix pressure vessels and equipment damage.
Shielded Metal Arc Welding (SMAW)
SMAW is a manual arc welding. The required equipment to perform SMAW is affordable, portable, and widely used. SMAW can be completed in various welding positions, such as horizontal, vertical, overhead, and flat. However, only highly skilled welders can deliver high-quality outcomes.
Flux Cored Arc Welding (FCAW)
FCAW is similar to SMAW but more automated. FCAW applies to thick metals since it provides solid and durable welds. The industry considers FCAW high-speed welding with minimal spatter.. The operator of FCAW does not have to possess skills as high compared to the SMAW welder.
Gas Tungsten Arc Welding (GTAW)
GTAW is a welding process with tungsten electrodes and inert shielding gas. A wide range of metals in any position can apply GTAW for its welding process. This method produces high-quality welds with excellent fusion and penetration but in a relatively slow process. GTAW is the proper welding process for thin sections.
Gas Metal Arc Welding (GMAW)
GMAW is a welding technique entailing electrode inert, shielding gas, and using wire-fed electrodes continuously. Compared to SMAW and FCAW, this technique offers cleaner welds with the simplest process possible. However, it requires a clean workpiece surface.
Submerged Arc Welding (SAW)
SAW has a high deposition rate but delivers a clean welding process. Like FCAW, this welding process is suitable for welding thick metal sections. With minimal spatter and large-scale welding compatibility, SAW has high-quality welds.
Selecting the appropriate welding process affects the success of a pressure vessel equipment repair. The general procedure for welding, which involves qualification of the welding processes, welders, and welders operators, had been arranged and specified under ASME PCC-2 standard. The standard is meant to bring the desired outcome where certified engineers carry out every step of reparation safely.
Join PetroSync Training: Master ASME PCC-2 for Enhanced Performance
If you want to familiarize yourself with the concepts and technical terms of the standards and dive deep into mastering the in-service problems in pressure equipment and piping, taking ASME PCC-2 Repair of Pressure Equipment training course should be your stepping stone. Join PetroSync’s ASME PCC-2 training course and start mastering the latest industry standards with our international instructors!
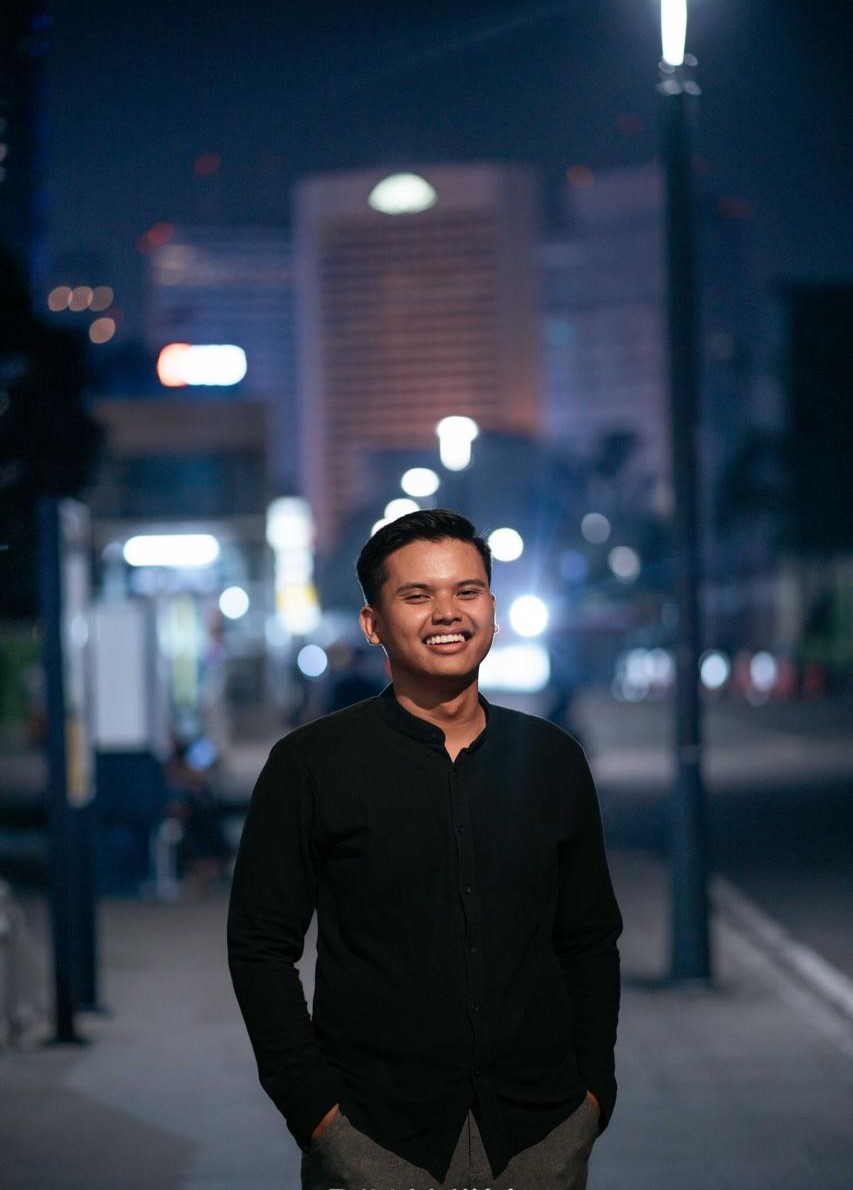
Results-oriented and thorough SEO specialist with extensive experience in conducting keyword research, developing and implementing digital website promotion strategies and plans, managing campaigns to develop company websites in the digital world, excellent knowledge of marketing techniques and principles, and attentive strong attention to detail.