API 570 inspection is vital for ensuring the integrity and safety of piping systems in various industries. Piping plays a crucial role in transporting fluids and gases, making regular inspection and maintenance essential to prevent accidents, leaks, or failures. API developed the API 570 standard, which provides guidelines for inspecting, repairing, altering, and rerating in-service piping systems. This article explores the significance, classification, types, and relevant context of API 570 inspection in maintaining reliable and long-lasting piping systems.
What Is API Piping 570 Inspection?
API Piping 570 inspection refers to the inspection, rating, repair, and alteration of in-service metallic and fiberglass-reinforced plastic (FRP) piping systems and their associated pressure-relieving devices according to the API standard. This code applies to all hydrocarbon and chemical process piping stated in section 1.2.
The main objective of API 570 Inspection is to ensure the safety and integrity of piping systems. Qualified inspectors follow API 570 requirements to assess the condition of piping components, identify defects or deterioration, and ensure compliance with design and regulatory standards.
During the inspection process, inspectors may refer to additional codes like ASME B31.3 and ASME B31.4, which provide further requirements for the design, fabrication, and installation of piping systems.
What Is API 570 Piping Classification?
Except as specified in 1.2.2., API 570 applies to piping systems used for process fluids, hydrocarbons, and other flammable or toxic fluids:
- Raw, intermediate, and finished petroleum and chemical products;
- Catalyst lines;
- Hydrogen, natural gas, fuel gas, and flare systems;
- Sour water and hazardous waste streams;
- Hazardous fluid services;
- Cryogenic fluids such as liquid N2, H2, O2, and air;
- High-pressure gases greater than 150 psig such as: gaseous He, H2, O2, and N2.
The fluid services and piping system classes mentioned below are not mandatory according to the requirements of API 570.
- Hazardous fluid services below designated threshold limits, as defined by jurisdictional regulations;
- Water (including fire protection systems), steam, steam-condensate, boiler feed water, and Category D fluid services as defined in ASME B31.3;
- Other classes of piping which are exempted from the applicable process piping code.
What Are the Types of API 570 Inspection?
Different types of inspection and surveillance are appropriate depending on the circumstances and the piping system. These include the following types of inspections and inspection focus areas:
1. Internal Visual Inspection
Internal Visual Inspection in API 570 involves visually examining the inside of piping systems to assess their condition. Qualified inspectors use tools like borescopes and remote cameras to inspect the interior surfaces for damage, corrosion, and defects.
Internal visual inspections are typically conducted for large-diameter transfer lines, ducts, catalyst lines, and other large piping systems. Remote visual inspection techniques are used for smaller pipes that are inaccessible for direct entry. This method is essential for identifying issues that may not be visible externally.
2. On-stream Inspection
On-stream inspection in API 570 involves inspecting piping systems while they are in operation. This inspection method allows for continuous monitoring and timely identification of defects or potential failures without causing significant disruptions to the production process.
During on-stream inspection, various non-destructive examination (NDE) techniques are employed to detect specific types of damage relevant to the piping system. These techniques are selected based on their ability to identify damage mechanisms from the outside and their suitability for on-stream conditions, including metal temperatures.
3. Thickness Measurement Inspection
Thickness Measurement Inspection involves measuring the thickness of piping components to assess their integrity and compliance with minimum thickness standards. This inspection method uses tools like ultrasonic thickness gauges to determine the thickness of pipe walls.
The purpose of thickness measurement inspection is to detect wall thinning, corrosion, erosion, or other types of deterioration that can compromise the structural integrity of the piping system. Regular measurements help track changes over time and determine if the remaining thickness meets safety requirements. When there is a significant change in the short-term corrosion rate, they should consult a corrosion specialist to determine the cause.
4. Various NDE Examinations
Various NDE (Non-Destructive Examination) techniques in API 570 are used to inspect piping systems without causing damage. These examinations include:
- Ultrasonic Testing (UT): Uses high-frequency sound waves to detect flaws and measure thickness.
- Magnetic Particle Testing (MT): Utilizes magnetic fields and iron particles to find surface defects in ferromagnetic materials.
- Liquid Penetrant Testing (PT): Uses dyes or fluorescent liquids to detect surface defects.
- Radiographic Testing (RT): Utilizes X-rays or gamma rays to reveal internal defects.
- Visual Testing (VT): Involves direct visual observation to identify visible defects, corrosion, or leaks.
The choice of NDE techniques depends on factors such as defect type, accessibility, material properties, and system requirements. These examinations help inspectors assess the condition of piping systems and determine necessary actions to ensure their integrity and safety.
5. External Visual Inspection
External Visual Inspection means visually examining the outside surfaces of piping systems to assess their condition. This inspection method helps identify any visible damage, corrosion, or defects that may require further attention or corrective measures.
During external inspections, it is important to survey the condition of piping hangers and supports. If there is corrosion product buildup or debris observed at the contact areas of pipe supports, it may be necessary to lift the pipe off these supports for a thorough inspection. Any cracked or broken hangers, spring supports “bottoming out,” displaced support shoes or other improper restraints should be reported and promptly corrected.
6. Vibrating Piping Inspection
When doing a vibrating piping inspection, it is important to examine piping systems to assess the risks associated with vibrations. This inspection aims to identify potential sources of excessive vibrations that can lead to equipment damage and safety hazards.
Based on the inspection findings, recommendations are provided for corrective actions, such as adding supports or implementing vibration-dampening methods. These measures aim to minimize vibration risks and ensure the safe operation of the piping system.
However, it’s important to note that fatigue cracking is typically a design-related issue. Once a crack initiates, it can grow unpredictably, and inspection alone is insufficient to manage the risk of failure. By the time a fatigue crack becomes detectable, approximately 80% of its lifespan has already been consumed, and failure can occur before the next scheduled inspection cycle without careful engineering assessment and analysis.
7. Supplemental Inspection.
Supplemental Inspection in API 570 involves conducting additional inspections beyond the routine ones specified by the standard. These inspections are performed to address specific concerns or conditions that require further evaluation.
Examples of such inspections include periodic use of radiography and thermography to detect fouling or internal blockages, thermography to identify hot spots in refractory lined systems, additional inspections following process unit upsets, verification of previously measured data, inspections for environmental cracking, and any other inspections specific to piping damage mechanisms.
What Concepts Does API 570 Acknowledge As Relevant Within Its Scope?
In API 570 Body of Knowledge, API 570 acknowledges the significance of two key concepts: Fitness for Service (FFS) and Risk-Based Inspection (RBI).
1. Fitness-For-Service (FFS)
This standard acknowledges the application of Fitness-For-Service principles to assess the damage in pressure-containing piping components during their service life. It references API 579-1/ASME FFS-1, which outlines specific assessment procedures for evaluating the fitness-for-service of piping components affected by various types of damage.
2. Risk-Based Inspection (RBI)
This standard acknowledges the use of Risk-Based Inspection (RBI) concepts for determining inspection intervals, due dates, and strategies. API 580 outlines the minimum requirements and recommended elements for establishing and maintaining a risk-based inspection program, including piping.
Additionally, API 581 provides methodologies for assessing risk, considering both Probability of Failure (POF) and Consequence of Failure (COF), and developing inspection plans based on those assessments.
In conclusion, having a strong grasp of API 570 and acquiring a deep understanding is of utmost significance for professionals engaged in the inspection and maintenance of piping systems. With the ever-increasing complexity and criticality of piping systems, possessing knowledge of API 570 becomes an invaluable asset that not only enhances career prospects but also contributes significantly to the overall safety, reliability, and efficiency of industrial operations.
To further enrich your knowledge and expertise in the realm of API 570 and expand your proficiency in piping inspection, enrolling in the API 570 training offered by Petrosync emerges as the perfect choice. Petrosync is renowned for delivering comprehensive and highly-regarded training programs that encompass the fundamental concepts, methodologies, and practical aspects of API 570 inspection.
API 570 course by PetroSync, facilitated by experienced instructors, provides you with a well-rounded learning experience, incorporating both theoretical knowledge and hands-on practical exercises. By opting for PetroSync’s API 570 Prep Course, you can confidently deepen your understanding of the standard, refine your inspection techniques, and make substantial contributions to enhancing the integrity and longevity of piping systems in your industry.
Embrace this opportunity to broaden your expertise, advance your career, and make a lasting impact on the reliability and safety of piping infrastructure.
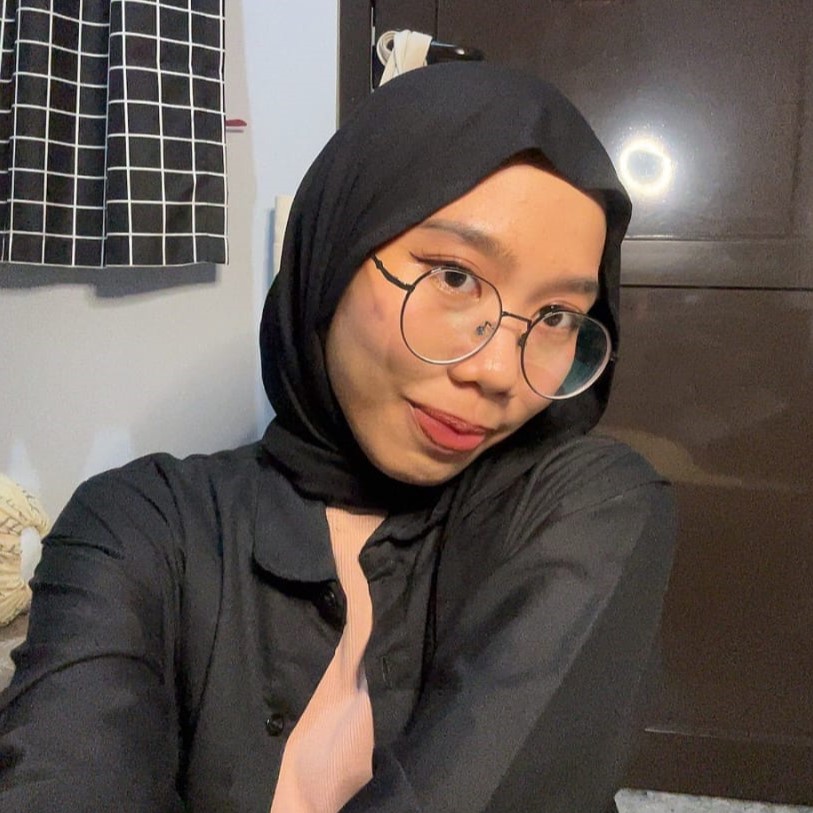
SEO specialist by day, fact-checker by night. An avid reader and content writer dedicated to delivering accurate and engaging articles through research and credible sources.